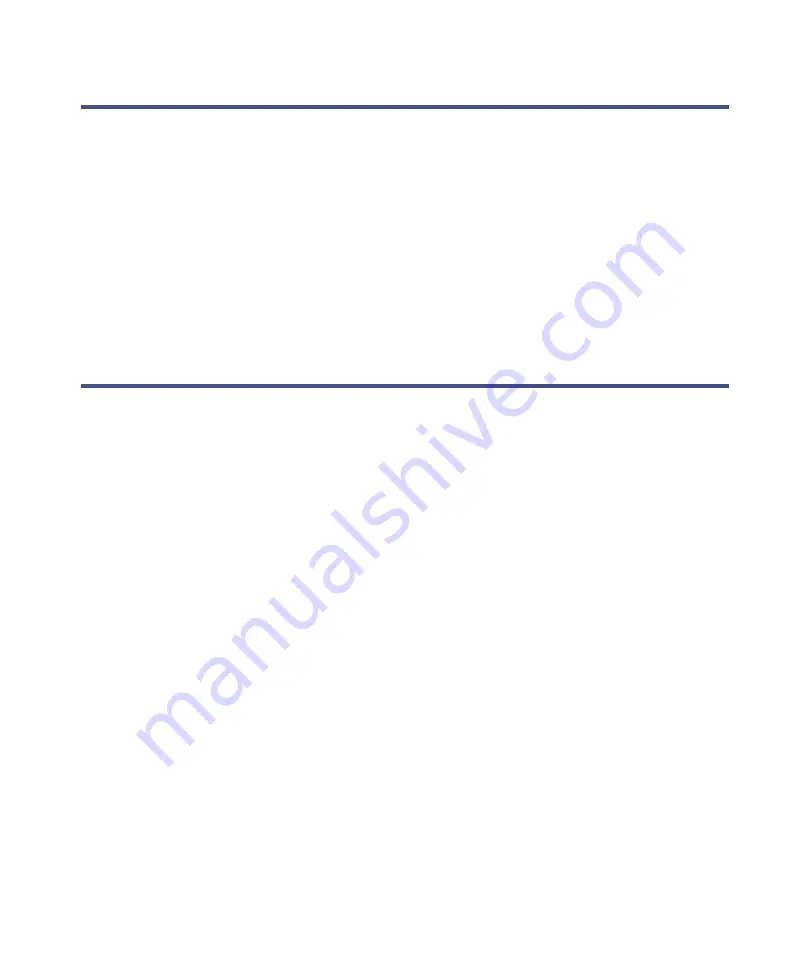
ii
Copyright notice
© 2006
−
2009 WATERS CORPORATION. PRINTED IN THE UNITED
STATES OF AMERICA AND IN IRELAND. ALL RIGHTS RESERVED. THIS
DOCUMENT OR PARTS THEREOF MAY NOT BE REPRODUCED IN ANY
FORM WITHOUT THE WRITTEN PERMISSION OF THE PUBLISHER.
The information in this document is subject to change without notice and
should not be construed as a commitment by Waters Corporation. Waters
Corporation assumes no responsibility for any errors that may appear in this
document. This document is believed to be complete and accurate at the time
of publication. In no event shall Waters Corporation be liable for incidental or
consequential damages in connection with, or arising from, its use.
Trademarks
Millennium, PIC, and Waters are registered trademarks, and busLAC/E,
PowerStation, and “THE SCIENCE OF WHAT’S POSSIBLE.” are trademarks
of Waters Corporation.
Micromass is a registered trademark, and MassLynx is a trademark of
Micromass Ltd.
Phillips is a registered trademark of Phillips Screw Company.
Other registered trademarks or trademarks are the sole property of their
owners.
Summary of Contents for 2424
Page 8: ...viii...
Page 30: ...1 16 2424 ELS Detector Optics Principles...
Page 64: ...2 34 Setting up the Detector...
Page 110: ...3 46 Operating the Detector...
Page 126: ...4 16 Maintaining the Detector...
Page 182: ...A 14 Safety Advisories...
Page 186: ...B 4 Specifications...
Page 196: ...Index 10...