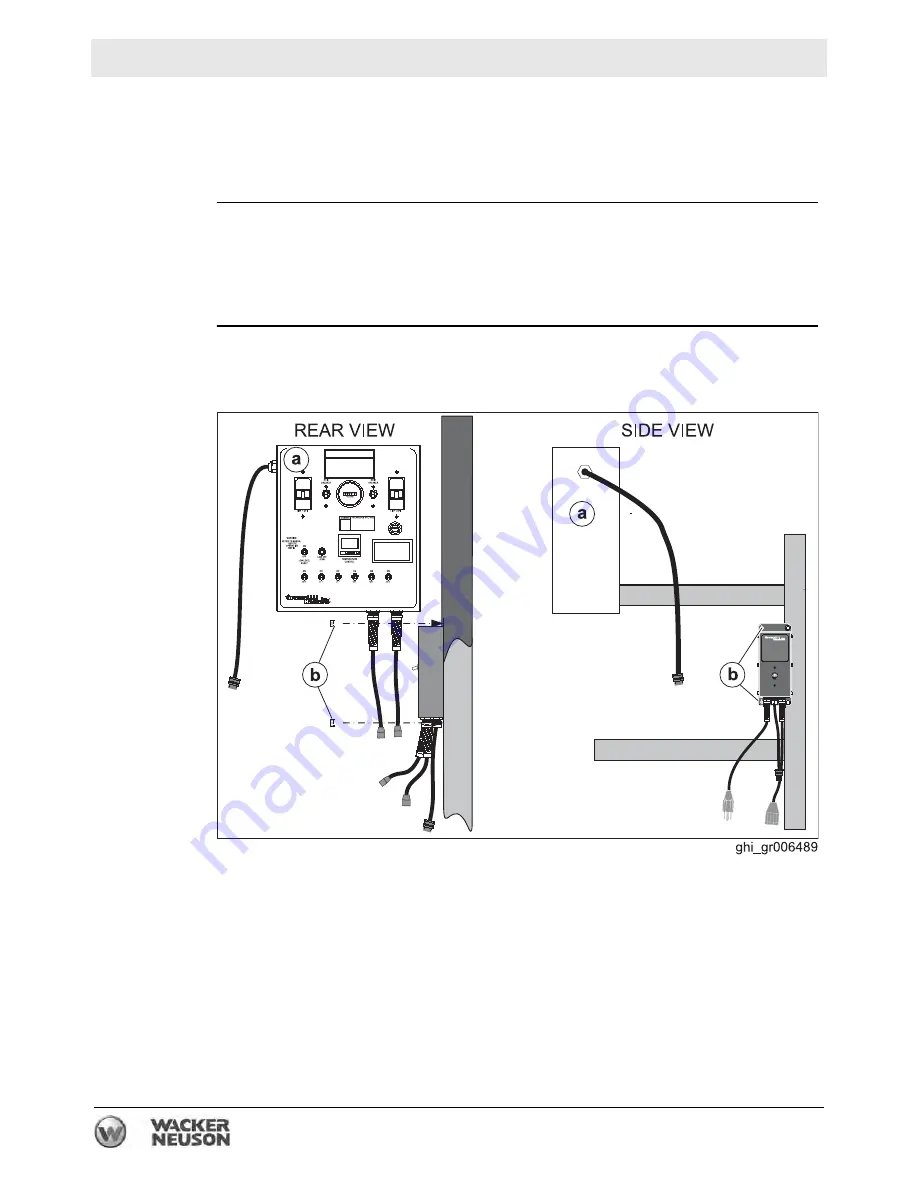
Accessories
E 2200, E 3000ES
76
wc_tx001668gb.fm
5.7
Mounting the Auxiliary Pump Panel
Requirments
Machine shut down
Power disconnected
Auxiliary Pump Panel
Background
The Wacker Neuson Auxiliary Pump Panel (APP) is an electrical device that
communicates with the main machine’s systems to provide protection for any
additional Pump Packs that are connected to the machine. If the machine
experiences a low level fault condition, the APP will cut off power to the external
components. This power cut-off protects the pumps from damage.
Guidelines
Follow the guidelines below when mounting the APP. Refer to the diagram below.
Install the APP inside the machine, near the main control panel
(a)
.
Install APP using included hardware
(b)
.
Summary of Contents for E 2200
Page 1: ...0192779 001 1210 0 1 9 2 7 7 9 Operator s Manual Hydronic Surface Heater E 2200 E 3000ES...
Page 4: ...Foreword 4 wc_tx001665gb fm...
Page 8: ...8 wc_bo0192779en_001TOC fm Table of Contents E 2200 E 3000ES...
Page 19: ...E 2200 E 3000ES Safety Information wc_si000540gb fm 19 Notes...
Page 64: ...Operation E 2200 E 3000ES 64 wc_tx001667gb fm Notes...
Page 90: ...Burner Setup E 2200 E 3000ES 90 wc_tx001669gb fm Notes...
Page 107: ...E 2200 E 3000ES Maintenance wc_tx001670gb fm 107 Notes...
Page 113: ...E 2200 E 3000ES Technical Data wc_td000422gb fm 113 9 4 Dimensions cm in...
Page 124: ...Schematics E 2200 E 3000ES 124 wc_tx001672gb fm 10 Schematics 10 1 Electrical Schematic...
Page 128: ...Schematics E 2200 E 3000ES 128 wc_tx001672gb fm 10 3 Burner System Circuit...
Page 129: ...E 2200 E 3000ES Schematics wc_tx001672gb fm 129 10 4 Circulation System Circuit ghi_gr005662...
Page 130: ...Schematics E 2200 E 3000ES 130 wc_tx001672gb fm 10 5 Rewind System Circuit...
Page 131: ......