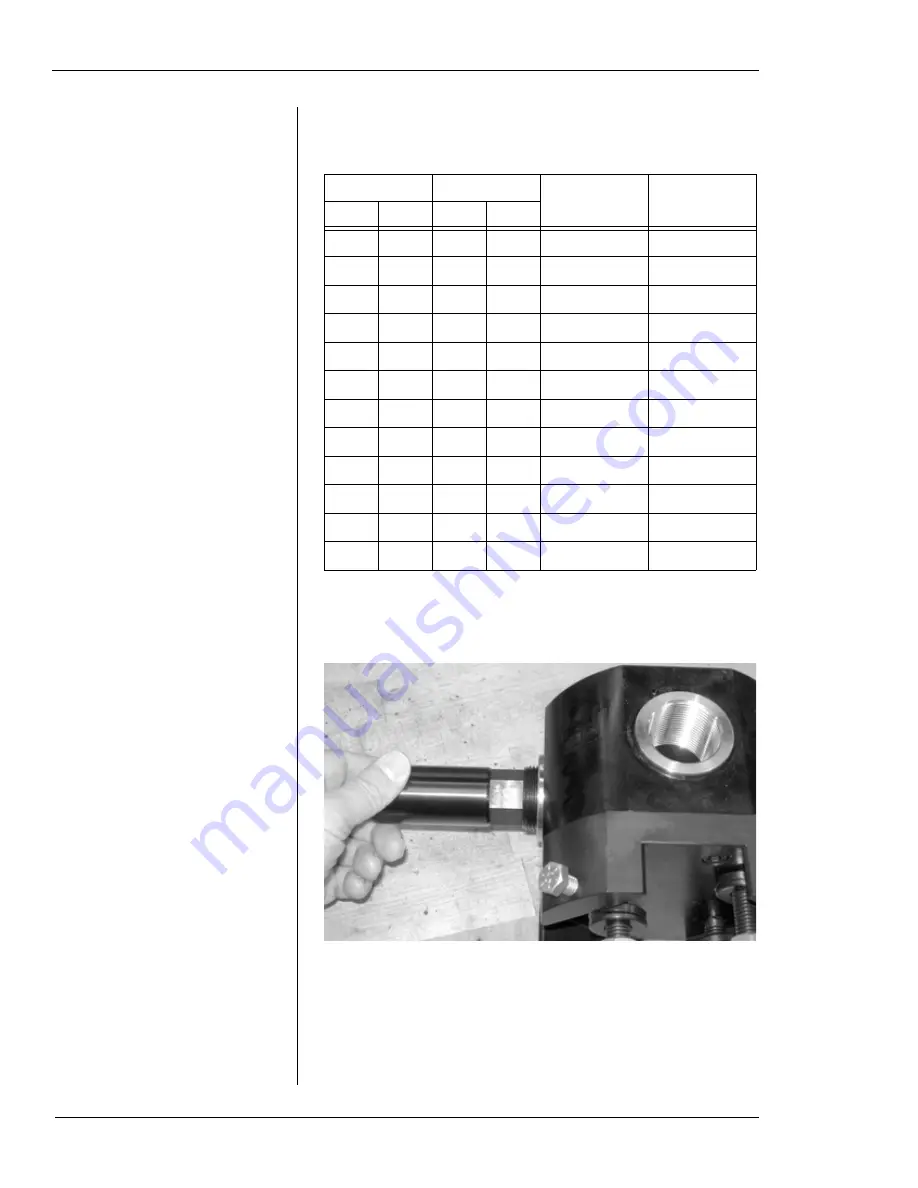
EP 424 End Prep Machine
38
Part No. 81-MAN-00, Rev. 0-0610
E.H. Wachs
3.
Screw the 4 chuck legs into the chuck body. Leave
about 1/2” of threads exposed for the jam nut.
Figure 5-9. Screw the chuck legs into the chuck.
4.
Put a jam nut over each leg, with the “shoulder” side
of it toward the chuck body. Thread it a few turns onto
the chuck leg.
Table 2: Independent Chuck Clamping Leg Chart
I.D. Inches
I.D. mm
Leg Set Used
Spacer (23-221-
00) Used
Min
Max
Min
Max
8.50
10.50
215.9
266.7
23-313-00
No
9.50
11.50
241.3
292.1
23-313-00
Yes
11.18
13.15
284.0
334.0
23-214-01
No
12.18
14.15
309.4
359.4
23-214-01
Yes
14.43
16.50
366.5
419.1
23-214-02
No
15.43
17.50
391.9
444.5
23-214-02
Yes
16.87
18.81
428.5
477.8
23-214-03
No
17.87
19.81
453.9
503.2
23-214-03
Yes
19.31
21.30
490.5
541.0
23-214-04
No
20.31
22.30
515.9
566.4
23-214-04
Yes
22.28
24.28
565.9
616.7
23-214-05
No
23.28
25.28
591.3
642.1
23-214-05
Yes
Summary of Contents for EP 424
Page 2: ...EP 424 End Prep Machine Part No 81 MAN 00 Rev 0 0610 E H Wachs...
Page 8: ...EP 424 End Prep Machine 4 Part No 81 MAN 00 Rev 0 0610 E H Wachs...
Page 14: ...EP 424 End Prep Machine 10 Part No 81 MAN 00 Rev 0 0610 E H Wachs...
Page 92: ...EP 424 End Prep Machine 88 Part No 81 MAN 00 Rev 0 0610 E H Wachs...
Page 98: ...EP 424 End Prep Machine 94 Part No 81 MAN 00 Rev 0 0610 E H Wachs...
Page 100: ...EP 424 End Prep Machine 96 Part No 81 MAN 00 Rev 0 0610 E H Wachs...