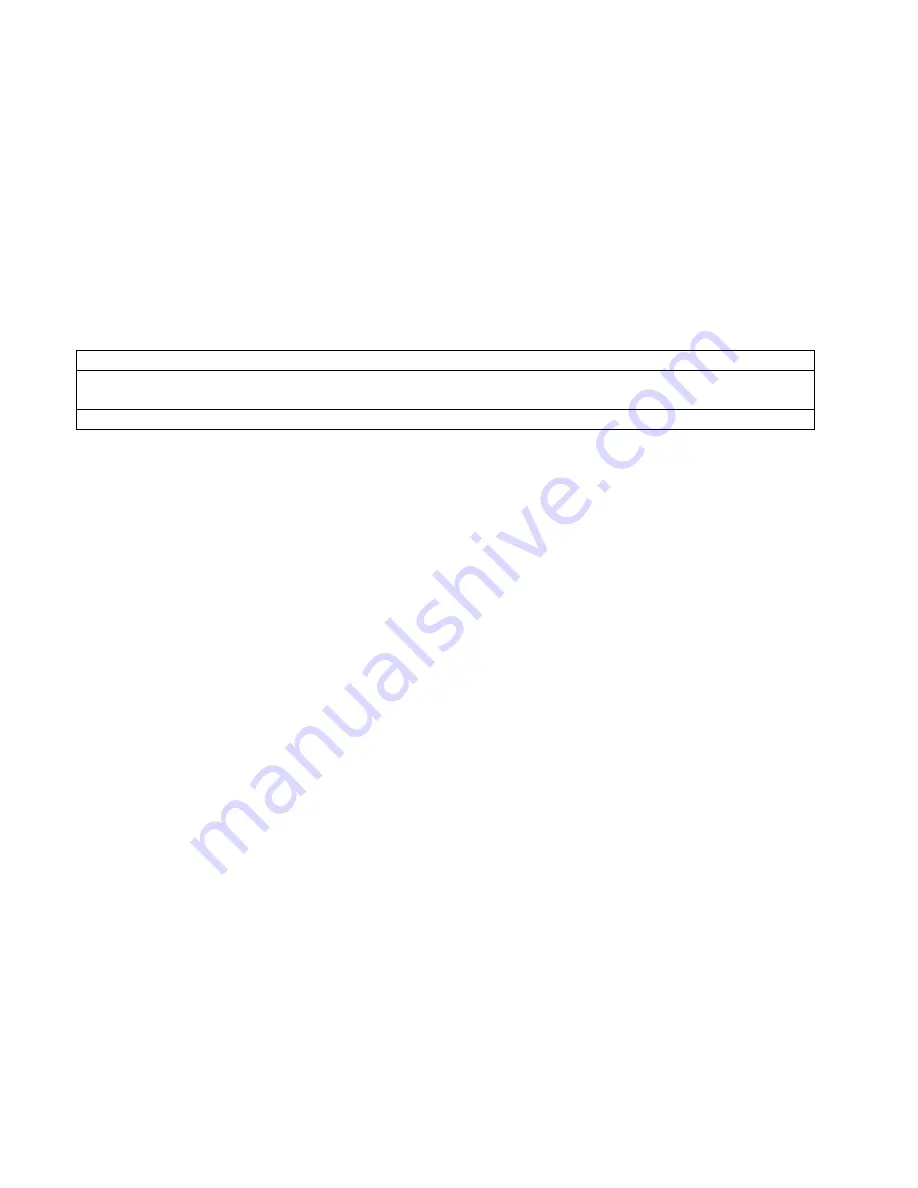
P118F Service Manual
SERVICE OPERATIONS
1/6/09
9-7
Electronic Motor Protector High-Potential Testing.
The solid state sensors and the electronic
components in the solid state module are delicate and can be damaged by exposure to high voltage.
Under no circumstances should a high potential test be made at the sensor terminals with the sensor
leads connected to the solid state module. Even though the power and pilot circuit leads are not
connected, the module can be damaged.
Electronic Motor Protector Field Trouble Shooting.
In the event the motor compressor is
inoperable or is not operating properly, the solid state control circuit may be checked as follows:
1. If the compressor has been operating and tripped on the protector, allow the compressor to cool
for at least one hour before checking. This allows time for the motor to cool and the control
circuit to reset.
! WARNING !
Before checking the TI31AA model for its attached wiring sensor, be aware
that the sensor terminal “C” has the same voltage as terminal L1.
! WARNING !
2. Disconnect control circuit power to deenergize the module. Connect a jumper wire across the
"control circuit" ("M1-M2") terminals on the module control circuit terminal board. This will
bypass the "control contact" of the module.
3. Reconnect control circuit power. If the compressor will not operate with the jumper wire
installed, then the problem is external to the solid state protection system. If the compressor
operates with the module bypassed, but will not operate when the jumper wire is removed, then
the control circuit relay or triac in the module is open.
4. If after allowing time for motor cooling, the protector still remains open, the motor sensors may
be checked as follows.
a) Disconnect control circuit power to deenergize the module. Remove the jumper of Step 2.
Remove wiring connections from the sensor and common terminals on the module control
circuit terminal board.
b) CAUTION: Use Ohmmeter with a maximum of 9 VAC for checking. The sensors are
sensitive, easily damaged, and no attempt should be made to check continuity through them
with other than an ohmmeter. Any external voltage or current applied to the sensors may
cause damage requiring compressor replacement.
c) Measure the resistance from each sensor terminal to the common terminal. The resistance
should be in the following range:
500
ohms (cold) to 20,000 + ohms (hot. compressor tripped)
Resistance readings in this range indicate the sensors are good. A resistance approaching
zero indicates a short; a resistance approaching infinity indicates an open connection.
Proper operation of the control system is dependent on a continuous parallel circuit through
all three sensors with no individual resistance reading higher than 10,000 ohms. On initial
start-up, and after any module trip due to high temperatures, the resistance of the sensors
must be below the module reset point before the module circuit will close. Reset values are
2700-4500 ohms.
Summary of Contents for TUBE-ICE P-118F
Page 1: ...P 118F TUBE ICE MACHINE Service Manual 5000 1 6 09 ...
Page 4: ......
Page 6: ......
Page 14: ...P118F Service Manual INTRODUCTION 1 6 09 1 4 FIGURE 1 1 Assembly Air Cooled Front View ...
Page 15: ...P118F Service Manual INTRODUCTION 1 6 09 1 5 FIGURE 1 2 Assembly Air Cooled Rear View ...
Page 16: ...P118F Service Manual INTRODUCTION 1 6 09 1 6 FIGURE 1 3 Assembly Air Cooled Right Side View ...
Page 17: ...P118F Service Manual INTRODUCTION 1 6 09 1 7 FIGURE 1 4 Assembly Water Cooled Front View ...
Page 18: ...P118F Service Manual INTRODUCTION 1 6 09 1 8 FIGURE 1 5 Assembly Water Cooled Rear View ...
Page 19: ...P118F Service Manual INTRODUCTION 1 6 09 1 9 FIGURE 1 6 Assembly Water Cooled Right Side View ...
Page 20: ...P118F Service Manual INTRODUCTION 1 6 09 1 10 ...
Page 23: ...P118F Service Manual RECEIPT OF YOUR TUBE ICE MACHINE 1 6 09 2 3 ...
Page 37: ......
Page 38: ...1 6 09 ...
Page 48: ......
Page 49: ...1 6 09 ...
Page 88: ...P118F Service Manual SERVICE OPERATIONS 1 6 09 9 18 FIGURE 9 8 Cutter Water Tank Assembly ...
Page 89: ...P118F Service Manual SERVICE OPERATIONS 1 6 09 9 19 FIGURE 9 9 Cutter Tank Parts cylinder ice ...
Page 90: ...P118F Service Manual SERVICE OPERATIONS 1 6 09 9 20 FIGURE 9 10 Cutter Drive Parts ...
Page 102: ...P118F Service Manual TABLES CHARTS 1 6 09 11 1 11 Tables Charts ...
Page 111: ...P118F Service Manual TABLES CHARTS 1 6 09 11 10 ...