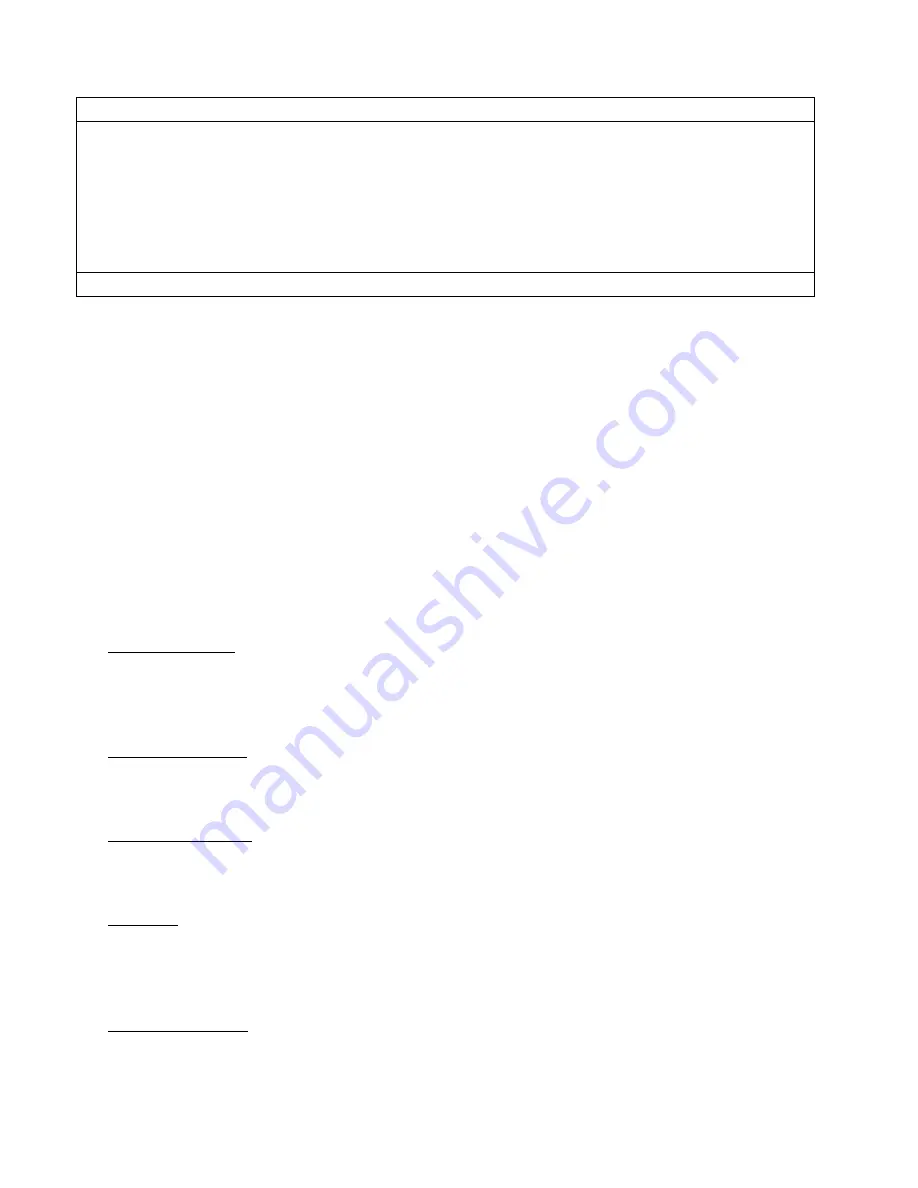
P118F Service Manual
SERVICE OPERATIONS
1/6/09
9-12
! WARNING !
It is not recommended that refrigerant be transferred from a
refrigeration system into a cylinder. If such a transfer is made,
the refrigerant cylinder must be an approved CLEAN cylinder--
free of any contaminants or foreign materials--and must be
weighed continuously to assure contents do not exceed net weight
specified by cylinder manufacturer or any applicable
code requirements.
! WARNING !
Refrigerant Leaks.
In addition to testing the machine for leaks as instructed under “Refrigerant
Charge”, it is advisable to again make a leak test after the unit has been in operation approximately
one week. Any noticeable change in operating conditions, other than shown on the “Certificate of
Test” may indicate a loss of refrigerant due to a leak. Always remove the refrigerant pressure from
the vessel or tubing before repairs are attempted.
Non-condensable Gases.
Satisfactory operation of the machine is not possible if non-condensable
gases (usually air) are present in the system. Excessive condensing pressure is an indication of such
gases. Excessive condensing pressure in water cooled condensers may also be due to the
accumulation of scale in the cooling coil or due to insufficient cooling water or excessive water
temperature. See “Water Cooled Condensers”, Section 7.
Compressor Motor Burnout
. There are several causes of compressor motor burnout. Some of
these are described below.
1. Low line voltage. A compressor motor is designed to operate within the range of plus or minus
10% of its nameplate voltage. Low voltage requires the motor windings to carry more current at
the same compressor load. When this current gets too high or is applied for an extended period,
the motor windings overheat, resulting in a failure or burnout.
2. Loss of refrigerant. The hermetic compressor motor is maintained at proper operating
temperature by passing cool suction gas over the motor windings. A loss of refrigerant can
cause the winding to overheat resulting in a failure or burnout.
3. High head pressure. The system is designed to operate at 200 psig. Excessive head pressure
adds refrigerating load on the compressor which can cause the windings to overheat and result in
a failure or burnout.
4. Moisture. Moisture in contact with refrigerant oil and the presence of heat will form
hydrochloric or hydrofluoric acid. The acid will destroy the insulation on the motor winding
causing a short circuit which can increase motor temperature in excess of 3000
°
F. This extreme
temperature will also create a sludge or black residue in the system.
5. Mechanical failure. Mechanical failure has been determined as a major cause of motor burnout.
Bearing wear or wipe-out may allow rotor to drag--overheating the windings and burnout.
Summary of Contents for TUBE-ICE P-118F
Page 1: ...P 118F TUBE ICE MACHINE Service Manual 5000 1 6 09 ...
Page 4: ......
Page 6: ......
Page 14: ...P118F Service Manual INTRODUCTION 1 6 09 1 4 FIGURE 1 1 Assembly Air Cooled Front View ...
Page 15: ...P118F Service Manual INTRODUCTION 1 6 09 1 5 FIGURE 1 2 Assembly Air Cooled Rear View ...
Page 16: ...P118F Service Manual INTRODUCTION 1 6 09 1 6 FIGURE 1 3 Assembly Air Cooled Right Side View ...
Page 17: ...P118F Service Manual INTRODUCTION 1 6 09 1 7 FIGURE 1 4 Assembly Water Cooled Front View ...
Page 18: ...P118F Service Manual INTRODUCTION 1 6 09 1 8 FIGURE 1 5 Assembly Water Cooled Rear View ...
Page 19: ...P118F Service Manual INTRODUCTION 1 6 09 1 9 FIGURE 1 6 Assembly Water Cooled Right Side View ...
Page 20: ...P118F Service Manual INTRODUCTION 1 6 09 1 10 ...
Page 23: ...P118F Service Manual RECEIPT OF YOUR TUBE ICE MACHINE 1 6 09 2 3 ...
Page 37: ......
Page 38: ...1 6 09 ...
Page 48: ......
Page 49: ...1 6 09 ...
Page 88: ...P118F Service Manual SERVICE OPERATIONS 1 6 09 9 18 FIGURE 9 8 Cutter Water Tank Assembly ...
Page 89: ...P118F Service Manual SERVICE OPERATIONS 1 6 09 9 19 FIGURE 9 9 Cutter Tank Parts cylinder ice ...
Page 90: ...P118F Service Manual SERVICE OPERATIONS 1 6 09 9 20 FIGURE 9 10 Cutter Drive Parts ...
Page 102: ...P118F Service Manual TABLES CHARTS 1 6 09 11 1 11 Tables Charts ...
Page 111: ...P118F Service Manual TABLES CHARTS 1 6 09 11 10 ...