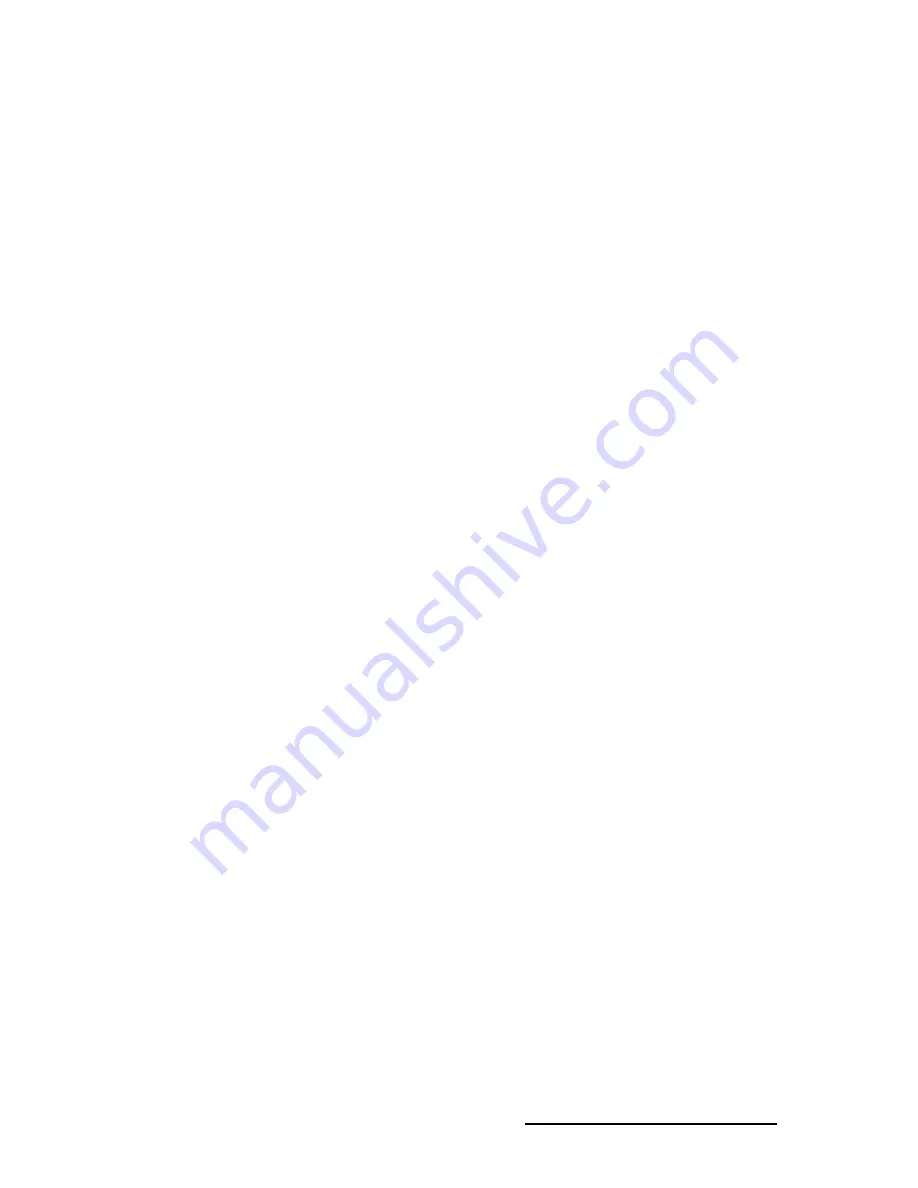
P118F Service Manual
MAINTENANCE
1/6/09
7-5
Part II.
The inside of the water end plates and the outer tube sheet surfaces should be cleaned only with clear
water and a rag or a soft bristle brush. A worn paint brush is excellent.
These surfaces have been coated with a special material which will give years of protection against
corrosion unless damaged. Never use a wire brush or a strong caustic on these surfaces.
Flush condenser tubes clear with air, water, or a piece of rag on a stick or wire. In many cases this is
all that is required. If the inside surfaces are smooth, even though discolored, further cleaning is not
necessary. It is useless to try and get a bright copper surface on the inside of the tubes. They will
discolor almost immediately in service and the condenser has been designed with an adequate
reserve for moderate fouling on these surfaces.
If, however, a rough coating remains inside the tubes after flushing and wiping, further cleaning is
desirable. The color of this coating varies with water conditions, but roughness indicates cleaning
tools should be used.
Any type tool to be considered should be tried first on a piece of copper tubing held in a vise or flare
block. Nylon, brass, or copper brushes are recommended. If any flakes of copper appear or if score
marks are made inside the tube, the tool should not be used. Never use anything with sharp or rigid
edges which could cut into the copper tubing.
Lubrication
Compressor.
When starting and charging the unit, the oil sight glass (33) in the crankcase of the
compressor should be watched carefully for the first hour to make certain the proper lubrication is
being maintained. The oil may become low in the crankcase on an initial start-up if electrical
current has been interrupted to the machine, thus de-energizing the compressor crankcase heater.
Before starting the machine again, the heater should be energized for a time period of at least two
hours to evaporate refrigerant that may have condensed in the crankcase during the shutdown period.
If the level is low after start-up, it should begin to return after a short period of operation.
The oil level should be checked frequently, particularly during the start-up operation, to see that a
sufficient amount of oil remains in the crankcase. While it is important to observe the oil splash
during operation, the true level can be obtained only when the compressor is stopped. With the
compressor idle, the oil level should be at a height of 1/4 to 1/2 of the sight glass but never out of
sight above it.
Although the machine was shipped with the oil charge, which was originally added for the test
operation, it may be necessary to add some oil when or if new refrigerant is added to the system.
An oil pump should be used to force any oil that may be required into the system. Oil may be added
to the compressor of all units through the low pressure test connection adjacent to the high/low
pressure switch or through the compressor suction service valve. The compressor suction service
valve should be “backseated” to shut off pressure to the gauge port when connecting the oil pump.
Air should be purged from the oil pump discharge line by forcing some oil through the line before
tightening the charging connection.
Use “Dual Inhibited Sunisco 3GS” (Viscosity 150) or equal.
Do not use a synthetic substitute.
Summary of Contents for TUBE-ICE P-118F
Page 1: ...P 118F TUBE ICE MACHINE Service Manual 5000 1 6 09 ...
Page 4: ......
Page 6: ......
Page 14: ...P118F Service Manual INTRODUCTION 1 6 09 1 4 FIGURE 1 1 Assembly Air Cooled Front View ...
Page 15: ...P118F Service Manual INTRODUCTION 1 6 09 1 5 FIGURE 1 2 Assembly Air Cooled Rear View ...
Page 16: ...P118F Service Manual INTRODUCTION 1 6 09 1 6 FIGURE 1 3 Assembly Air Cooled Right Side View ...
Page 17: ...P118F Service Manual INTRODUCTION 1 6 09 1 7 FIGURE 1 4 Assembly Water Cooled Front View ...
Page 18: ...P118F Service Manual INTRODUCTION 1 6 09 1 8 FIGURE 1 5 Assembly Water Cooled Rear View ...
Page 19: ...P118F Service Manual INTRODUCTION 1 6 09 1 9 FIGURE 1 6 Assembly Water Cooled Right Side View ...
Page 20: ...P118F Service Manual INTRODUCTION 1 6 09 1 10 ...
Page 23: ...P118F Service Manual RECEIPT OF YOUR TUBE ICE MACHINE 1 6 09 2 3 ...
Page 37: ......
Page 38: ...1 6 09 ...
Page 48: ......
Page 49: ...1 6 09 ...
Page 88: ...P118F Service Manual SERVICE OPERATIONS 1 6 09 9 18 FIGURE 9 8 Cutter Water Tank Assembly ...
Page 89: ...P118F Service Manual SERVICE OPERATIONS 1 6 09 9 19 FIGURE 9 9 Cutter Tank Parts cylinder ice ...
Page 90: ...P118F Service Manual SERVICE OPERATIONS 1 6 09 9 20 FIGURE 9 10 Cutter Drive Parts ...
Page 102: ...P118F Service Manual TABLES CHARTS 1 6 09 11 1 11 Tables Charts ...
Page 111: ...P118F Service Manual TABLES CHARTS 1 6 09 11 10 ...