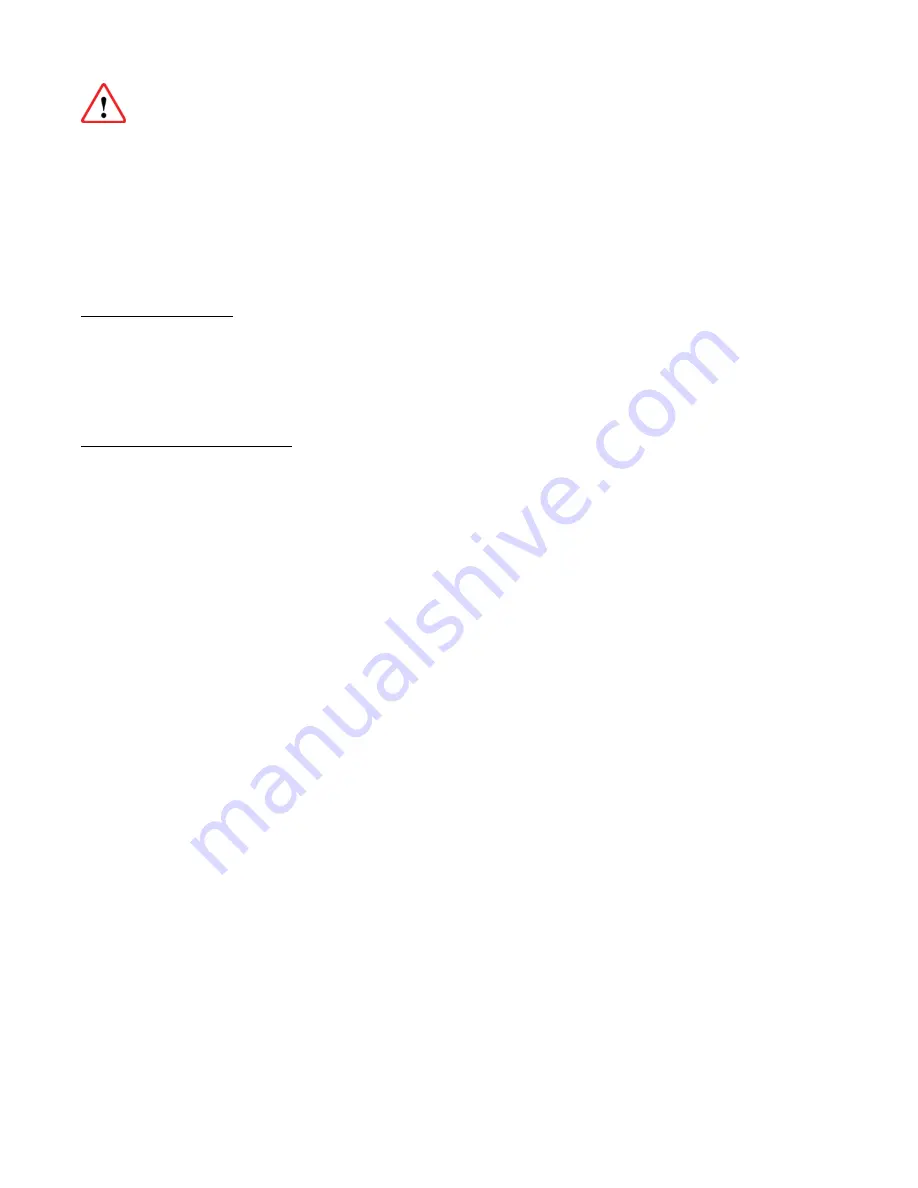
9-9
Warning:
Approved refrigerant recovery equipment, hoses, gauges, and refrigerant containers must be
used in compliance with all local and federal regulations. Only qualified personnel should perform refrigerant
servicing and recovery processes. Follow these instructions carefully. Severe personal injury can result from
improper discharge of refrigerant. It is not recommended to transfer refrigerant from a refrigeration system
directly into a cylinder unless this cylinder is an approved, clean cylinder (free of any contaminants or foreign
materials). The cylinder must be weighed continuously to assure contents do not exceed the net weight
specified by the cylinder manufacturer or any applicable code requirements.
Note:
Observe all local codes when handling and discharging refrigerant.
Refrigerant Leaks
It is recommended to complete a leak test after the unit has been in operation for approximately one week. Any
noticeable change in operating conditions, other than shown on the Certificate of Test, may indicate a loss of
refrigerant due to a leak. Always completely evacuate and recover the refrigerant from the vessel or tubing
before repairs are attempted.
Non-Condensable Gases
Air and other non-condensable gases in a refrigeration system are not desirable and can cause unsatisfactory
machine performance. Non-condensable gas effects are:
•
Higher condensing pressure than what should match the condensed liquid temperature according to a
pressure-temperature chart
•
Greater electrical power consumption
•
Reduced refrigeration capacity
•
Longer than normal compressor running time
•
Slow ice release
•
Long thaw cycle
Air collects mostly in high-pressure condensers, receivers, and other high-pressure components. It is most
commonly found in the coolest, lowest-velocity area of these components.
Evaporative condensers usually have purge points at the top of the outlet header of each circuit. Receivers
usually have a purge point at the top, away from the inlet, where it is coolest, and the gas velocity is the lowest.
Excessive condensing pressure in water-cooled condensers may also be due to:
•
Accumulation of scale in the cooling coil
•
Insufficient cooling water
•
Excessive water temperature
Summary of Contents for Tube-Ice HFO10
Page 2: ......
Page 6: ......
Page 10: ......
Page 12: ......
Page 16: ...2 4 Figure 3 Water Cooled Piping Schematic ...
Page 17: ...2 5 Figure 4 Air Cooled Piping Schematic ...
Page 36: ......
Page 40: ......
Page 43: ...6 3 Figure 16 Panel Layout 60 Hz Non CE Machines ...
Page 44: ...6 4 Figure 17 Electrical Schematic Control Circuit All Voltages 50 Hz ...
Page 45: ...6 5 Figure 18 Electrical Schematic Control Circuit All Voltages 60 Hz ...
Page 46: ...6 6 Figure 19 Electrical Schematic 3 Phase Power All Voltages 50 Hz ...
Page 47: ...6 7 Figure 20 Electrical Schematic 3 Phase Power All Voltages 60 Hz ...
Page 68: ......
Page 96: ......
Page 110: ...Notes ...
Page 111: ...Notes ...