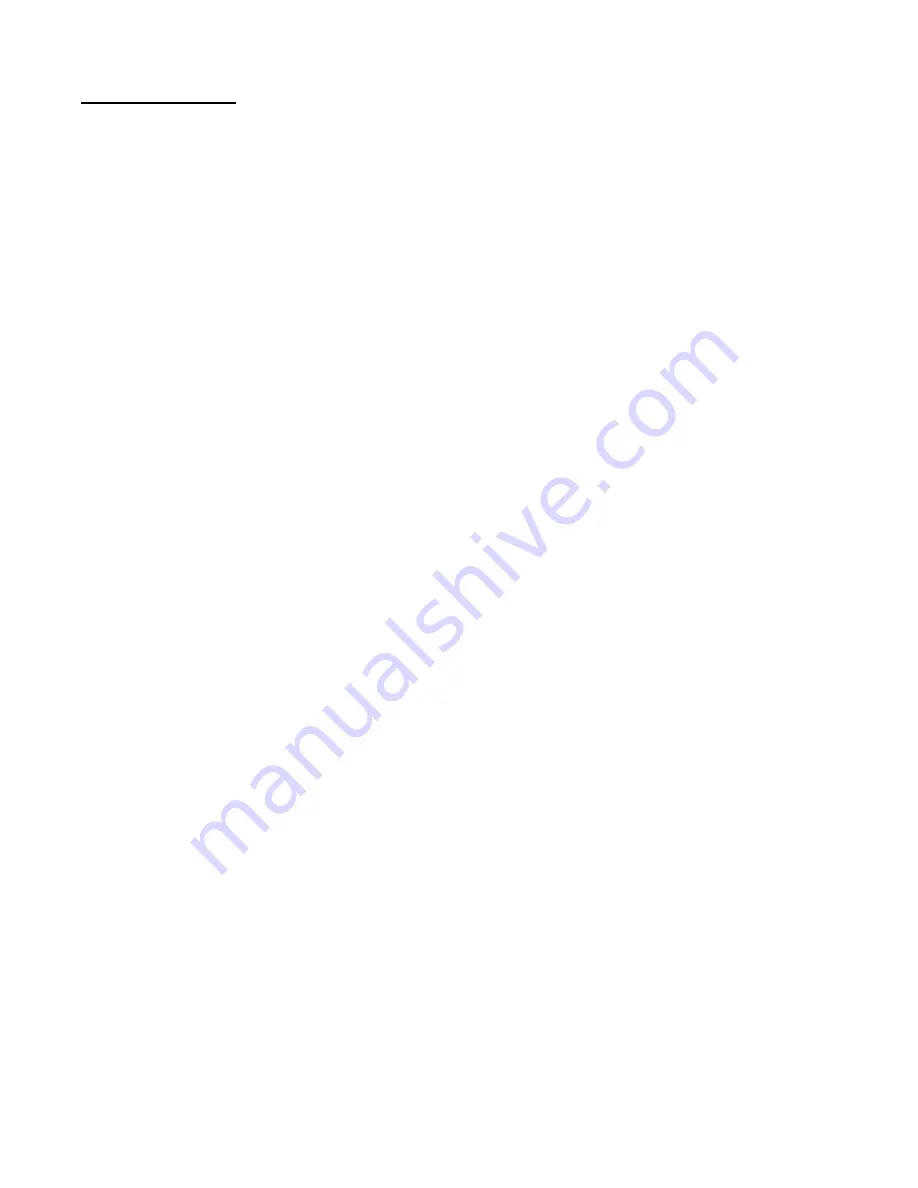
7-6
Mechanical Cleaning
The following steps should be followed during mechanical cleaning.
1.
Close the stop valve in the water supply line.
2.
Drain the water from the condenser.
3.
Remove the water regulating valve and associated piping from the condenser.
4.
Remove the nuts, water plates, and gaskets from both ends of the condenser.
−
If the gasket does not lift off with the end plate, do not attempt to pry it off. This can damage the
sealing surface, causing a water leak. To free a sticking gasket, replace the water plate and tap the
outside face of the plate with a rubber mallet or block of wood. After a few taps, the gasket will
spring free and slip off with the water end plate.
5.
Rinse gaskets with running water and use a rag or soft brush to remove foreign matter.
−
Rust, scale, and dirt will not stick to the gasket material.
6.
Use clean water and a rag or soft bristle brush to clean the inside of the water end plates and the outer
tube sheet surfaces.
Note:
Never use a wire brush or strong caustic on these surfaces.
−
These surfaces have been coated with a special material that will give years of protection against
corrosion unless damaged.
7.
Flush the condenser tubes clear with air, water, or a piece of rag on the end of a stick or wire. This will
sufficiently clean the tubes in many cases.
−
If the inside surfaces are smooth, further cleaning is not necessary, even though the surfaces may be
discolored. Do not attempt to achieve a bright copper finish on the tubes as they will quickly discolor
when in service. The condenser is designed to handle moderate fouling on these surfaces.
−
If a rough coating remains on the insides of the tubes after flushing and wiping, further cleaning is
required. The color will vary depending on water conditions. In these circumstances, use a nylon,
brass, or copper brush to clean the tubes. Do not use any tool that will score, mark, flake, or
otherwise cut into the tubes.
Summary of Contents for Tube-Ice HFO10
Page 2: ......
Page 6: ......
Page 10: ......
Page 12: ......
Page 16: ...2 4 Figure 3 Water Cooled Piping Schematic ...
Page 17: ...2 5 Figure 4 Air Cooled Piping Schematic ...
Page 36: ......
Page 40: ......
Page 43: ...6 3 Figure 16 Panel Layout 60 Hz Non CE Machines ...
Page 44: ...6 4 Figure 17 Electrical Schematic Control Circuit All Voltages 50 Hz ...
Page 45: ...6 5 Figure 18 Electrical Schematic Control Circuit All Voltages 60 Hz ...
Page 46: ...6 6 Figure 19 Electrical Schematic 3 Phase Power All Voltages 50 Hz ...
Page 47: ...6 7 Figure 20 Electrical Schematic 3 Phase Power All Voltages 60 Hz ...
Page 68: ......
Page 96: ......
Page 110: ...Notes ...
Page 111: ...Notes ...