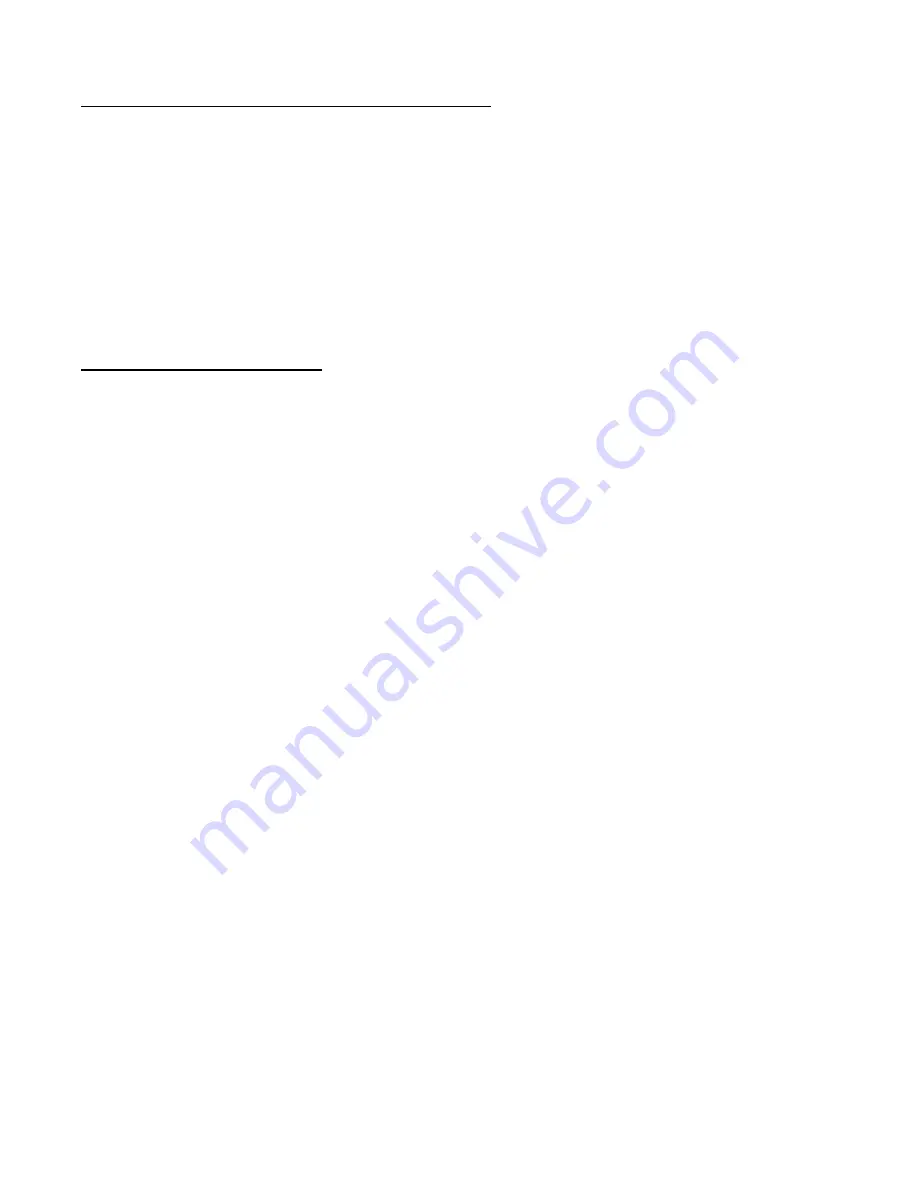
9-5
Compressor Motor Protection
—
Field Diagnosis
The protective devices SE-E1 or SE-E2 monitor motor and discharge gas temperatures, rotating direction, and
check for phase loss.
•
Temperature monitoring
. Locks out immediately if pre-set temperatures for the motor, discharge gas,
or the oil are exceeded. Acceptable temperature range is -22° to 140°F (-30 to 60°C).
•
Compressor Rotation
. Checks the rotation direction during the first 5 seconds of compressor operation.
If the compressor starts with the wrong rotation direction, the module locks out immediately.
•
Phase Loss
. Checks for phase loss in the first 5 seconds of compressor operation and opens relay contact
immediately if phase loss occurs. The contact closes after 6 minutes. If three-phase losses occur within
18 minutes, or 10 within 24 hours, the module locks out.
•
Reset.
To reset after a lock out, power must be removed from the module for 5 seconds.
Compressor Motor Burnout
Compressor motor burnout can have several causes, including:
•
Low Line Voltage
. A compressor motor is designed to operate within the range of ±10% of its nameplate
voltage. Low voltage requires the motor windings to carry more current at the same compressor load.
When this current becomes too high or is applied for an extended period, the motor windings overheat,
resulting in a failure.
•
Loss of Refrigerant
. The semi-hermetic compressor motor is maintained at proper operating
temperature by passing cool suction gas over the motor windings. A loss of refrigerant can cause the
winding to overheat, resulting in a failure or burnout.
•
High Head Pressure
. The system is designed to operate at 130 psig (9 bar). Excessive head pressure
increases the refrigeration load on the compressor. This increase can cause the windings to overheat,
resulting in a failure or burnout.
•
Moisture
. Moisture in contact with refrigerant oil and the presence of heat will form hydrochloric or
hydrofluoric acid. The acid will destroy the insulation on the motor windings, causing a short circuit,
which can increase motor temperatures in excess of 3,000°F (1,649°C). This extreme temperature will
also create a sludge or black residue in the system.
•
Mechanical Failure
. Mechanical failure has been determined to be a major cause of motor burnout.
Bearing wear or wipe-out may allow the rotor to drag, overheating the windings and causing a burnout.
Whenever a compressor fails because of a motor burnout, it is important to thoroughly clean the system before
replacing the damaged compressor, or a new compressor may also become damaged.
Summary of Contents for Tube-Ice HFO10
Page 2: ......
Page 6: ......
Page 10: ......
Page 12: ......
Page 16: ...2 4 Figure 3 Water Cooled Piping Schematic ...
Page 17: ...2 5 Figure 4 Air Cooled Piping Schematic ...
Page 36: ......
Page 40: ......
Page 43: ...6 3 Figure 16 Panel Layout 60 Hz Non CE Machines ...
Page 44: ...6 4 Figure 17 Electrical Schematic Control Circuit All Voltages 50 Hz ...
Page 45: ...6 5 Figure 18 Electrical Schematic Control Circuit All Voltages 60 Hz ...
Page 46: ...6 6 Figure 19 Electrical Schematic 3 Phase Power All Voltages 50 Hz ...
Page 47: ...6 7 Figure 20 Electrical Schematic 3 Phase Power All Voltages 60 Hz ...
Page 68: ......
Page 96: ......
Page 110: ...Notes ...
Page 111: ...Notes ...