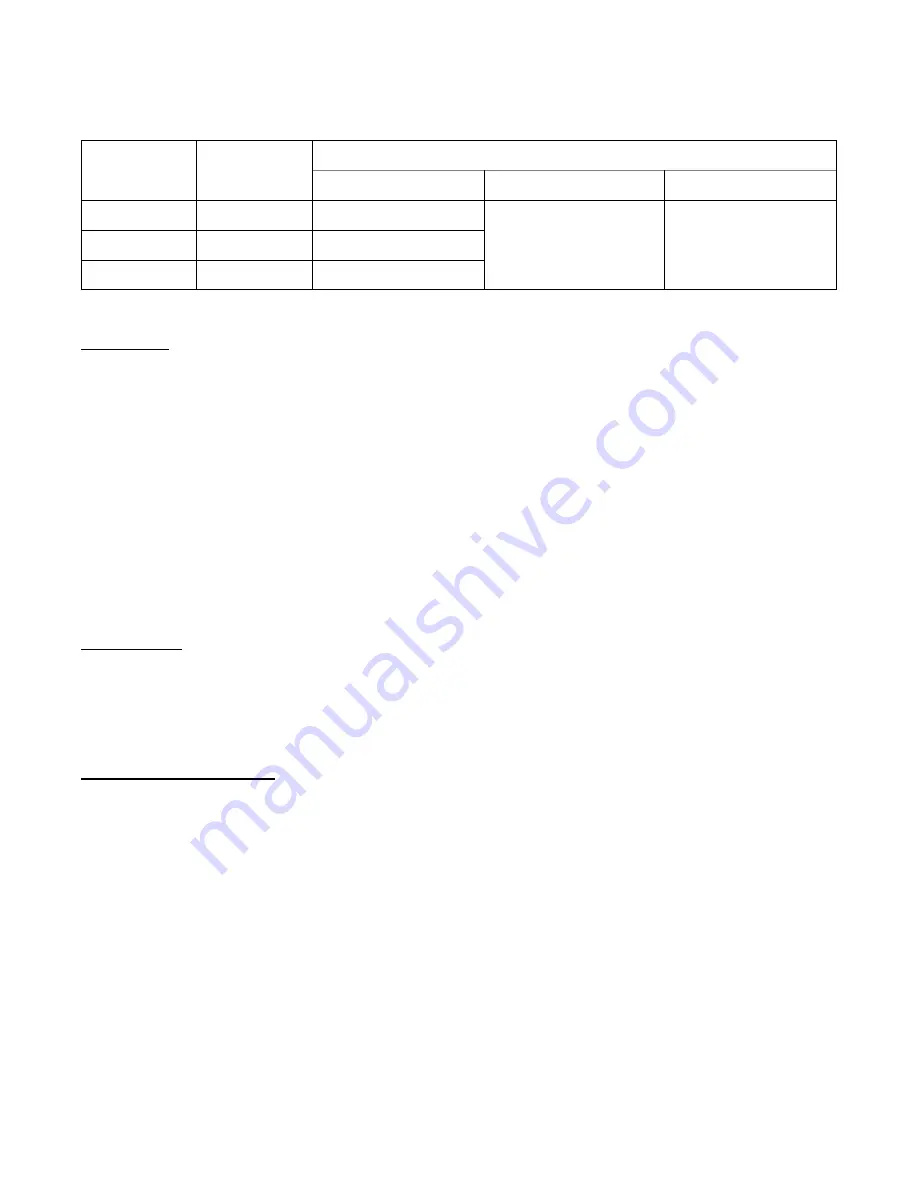
7-4
Table 8 shows the part numbers and tube quantities for water distributors on the HFO10.
Table 8: Water Distributor Information
Tube Size
in. (mm)
Number of
Tubes
Vogt Part Numbers
Water Distributor
Freezer Cover
Freezer Cover Gasket
1 (25)
156
12B2185N11
12B2145C03
12A2600G15
1-1/4 (32)
102
12B2185N21
1-1/2 (38)
72
12B2185N31
Water Tank
The production of opaque ice indicates the water in the water tank contains a concentrated number of solids or
salts. To remedy this problem, follow the steps below:
1.
Shut down the machine.
2.
Remove the cover plate on the water tank and open the drain valve.
3.
Clean the tank thoroughly by flushing it out with a hose and scrubbing it with a stiff brush. It may be
necessary to completely remove the water tank in order to clean all internal surfaces.
4.
After cleaning, reinstall the tank if necessary, close the drain valve, and fill the tank with fresh water.
5.
Set the
Clean/Off/Ice
selector switch to the
Clean
position and press
Start
to check if the pump is
working properly. Air may have collected in the impeller housing, and the pump may have to be stopped
and started several times to expel this air.
6.
After the pump is checked for proper flow, set the
Clean/Off/Ice
selector switch to the
Ice
position and
press
Start
to resume ice production.
Freezer Cover
A clear polycarbonate freezer cover is provided for visual inspection of the water box and water distributors
located at the top of the freezer. The cover should be removed and cleaned if it becomes coated with deposits.
Generally, if this cover is coated with solids, this is a major indicator that other water contact areas (i.e., water
tank and distributors) also require cleaning.
Water-Cooled Condensers
The interval in which condensers require cleaning varies. Some installations seldom need cleaning, while others
may require cleaning at least once a year or even several times a year.
Proper operation of cooling towers increases the interval between cleaning considerably. Check the tower
overflow rate frequently. If a tower operates with insufficient overflow (nominal 1.5 to 3 gph [5.7
–
11.4 Lph],
depending on water quality), the resulting mineral concentration in the water can cause rapid and heavy fouling
inside the condenser tubes, requiring excessively frequent cleaning. Also, these conditions often lead to severe
corrosion.
Chemical additives, including those used to stop algae and related growths, should be obtained only from a
reputable, established supplier. Always follow
manufacturer’s
directions. Excessive treatment of the water can
cause more harm than good, and the condensers, pumps, piping, and towers themselves may be damaged.
Double check the system to make sure that fouling is actually causing the trouble. High head pressure alone
does not mean a fouled condenser.
Before cleaning, always check for the following conditions:
Summary of Contents for Tube-Ice HFO10
Page 2: ......
Page 6: ......
Page 10: ......
Page 12: ......
Page 16: ...2 4 Figure 3 Water Cooled Piping Schematic ...
Page 17: ...2 5 Figure 4 Air Cooled Piping Schematic ...
Page 36: ......
Page 40: ......
Page 43: ...6 3 Figure 16 Panel Layout 60 Hz Non CE Machines ...
Page 44: ...6 4 Figure 17 Electrical Schematic Control Circuit All Voltages 50 Hz ...
Page 45: ...6 5 Figure 18 Electrical Schematic Control Circuit All Voltages 60 Hz ...
Page 46: ...6 6 Figure 19 Electrical Schematic 3 Phase Power All Voltages 50 Hz ...
Page 47: ...6 7 Figure 20 Electrical Schematic 3 Phase Power All Voltages 60 Hz ...
Page 68: ......
Page 96: ......
Page 110: ...Notes ...
Page 111: ...Notes ...