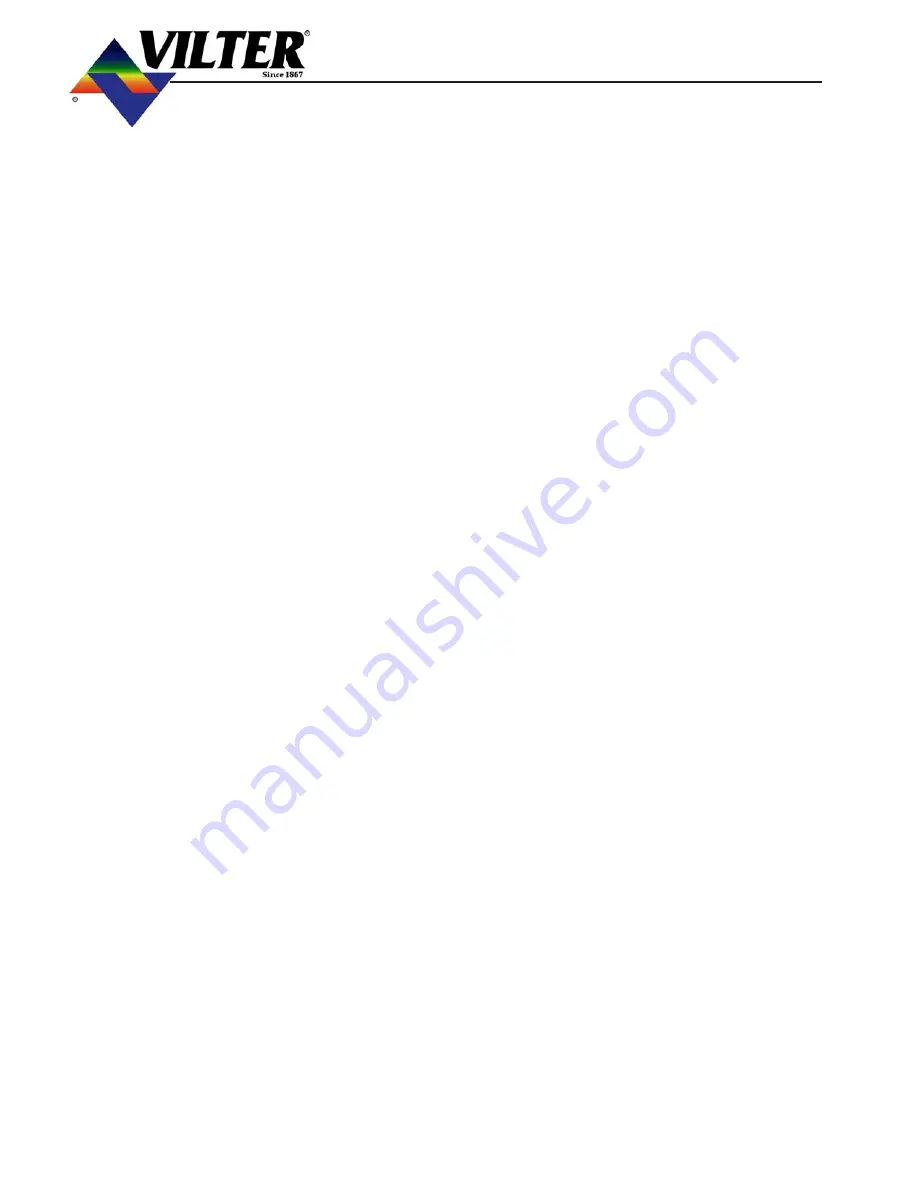
24
Installation
Charge a small amount of ammonia into the sys-
tem and pressurize the system to its respective
design pressure. Pass a lit sulfur stick around all
joints and connections. Any leaks will be indi-
cated by a heavy cloud of smoke. If any leaks are
observed during this test, they must be repaired
and rechecked before the system can be consid-
ered tight and ready for evacuation.
B.
Halocarbon Refrigerant Systems
“Oil pumped” dry nitrogen, or anhydrous CO2 in
this order of preference may be used to raise the
pressure to the proper level for testing.
When the proper pressure is attained, test for leaks
with the soap mixture previously described. Af-
ter all leaks are found and marked, relieve the
system pressure and repair the leaks. Never at-
tempt to repair soldered or welded joints while
the system is under pressure. Soldered joints
should be opened and re soldered.
Do not simply add more solder to the leaking joint.
After all the joints have been repaired and the
system is considered “tight” the system may be
tested with refrigerant.
Attach a drum of the refrigerant to be used in the
system and allow the gas to enter until a pressure
of 5 psig is reached.
Remove the refrigerant drum and bring the pres-
sure to the recommended test level with oil
pumped dry nitrogen or CO2. Then check the
entire system again for leaks, using a halide torch
or electronic leak detector. Be sure to check all
flanged, welded, screwed and soldered joints, all
gasketed joints, and all parting lines on castings.
If any leaks are found, they must be repaired and
rechecked before the system can be considered
tight again, remembering that no repair should
be made to welded or soldered joins while the sys-
tem is under pressure.
C.
Evacuating The System
A refrigeration system operates best when only
refrigerant is present. Steps must be taken to re-
move all air, water, vapor, and all other non-
condensables from the system before charging it
with refrigerant. A combination of moisture and
refrigerant, along with any oxygen in the sys-
tem, can form acids or other corrosive com-
pounds that corrode internal parts of the system.
To properly evacuate the system, and to remove
all non-condensables, air and water vapor, use a
high vacuum pump capable of attaining a
blanked off pressure of 50 microns or less. At-
tach this pump to the system and allow it to op-
erate until system pressure is reduced somewhere
below 1000 microns. Evacuation should not be
done unless the room temperature is 60F or
higher.
Attach vacuum gauge(s), reading in the 20 to
20,000 micron gauge range, to the refrigerant
system. These gauge(s) should be used in con-
junction with the high vacuum pump. The read-
ing from the gauge(s) indicates when the system
has reached the low absolute pressure required
for complete system evacuation.
Connect the high vacuum pump into the refrig-
eration system by using the manufacturer’s in-
structions. Connect the pump both to the high
side and low side of the system, to insure system
evacuation. Attach the vacuum gauge to the sys-
tem in accordance with the manufacturer’s in-
structions.
A single evacuation of the system does not satis-
factorily remove all of the non-condensable, air
and water vapor. To do a complete job, a triple
evacuation is recommended.
When the pump is first turned on, bring system
pressure to as low a vacuum level as possible,
and continue operation for 5 to 6 hours.
Stop the pump and isolate the system. Allow the
unit to stand at this vacuum for another 5 to 6
hours. After this time, break, the vacuum and
bring the system pressure up to 0 psig with dry
nitrogen.
To begin the second evacuation, allow the pump
to operate and reduce the pressure again to within
50 to 1000 microns. After this reading is reached,
Summary of Contents for VSM 71-701
Page 1: ...1 VPN 35391S February 2006 Rev 05 Price 60 00...
Page 2: ...2...
Page 20: ...20...
Page 52: ...53 Pre Start Up Check List...
Page 99: ...99 Recommended Spare Parts List...
Page 104: ...104 Gate Rotor...
Page 110: ...110 Main Rotor VSS...
Page 112: ...112 Main Rotor VSR...
Page 114: ...114 Slide Valve Cross Shafts and End Plate...
Page 118: ...118 Capacity Slide Volume Slide Carriage Assembly Slide Valve Carriage Assembly...
Page 134: ...134 Miscellaneous Frame Components VSS Screw Compressor VSR Mini Screw Compressor...
Page 138: ...138 C FlangeAdapter Components 630 620 610 640 601 641 630 601 620 610 640 641 642 650 651...
Page 140: ...140 Replacement Parts Tools...
Page 144: ...144 GaterotorAssembly...
Page 148: ...148 Main Rotor Slide Valve Cross Shafts and End Plate Models 71 401 Only Counter clockwise...
Page 152: ...152 Main Rotor Slide Valve Cross Shafts and End Plate Model 501 701 Only Clockwise...
Page 154: ...154 Volume Ratio Capacity Slide Carriage Assembly Slide Valve Carriage Assembly...
Page 158: ...158 Miscellaneous Frame Components Model VSM 501 701 Model VSM 71 401...
Page 160: ...160 Replacement Parts Accessories Housing Accessories C Flange Assembly...
Page 166: ...166 Haight Pumps...
Page 170: ...3 Refrigerating Specialties Division...
Page 236: ......
Page 237: ......
Page 238: ......
Page 243: ......
Page 244: ...168...