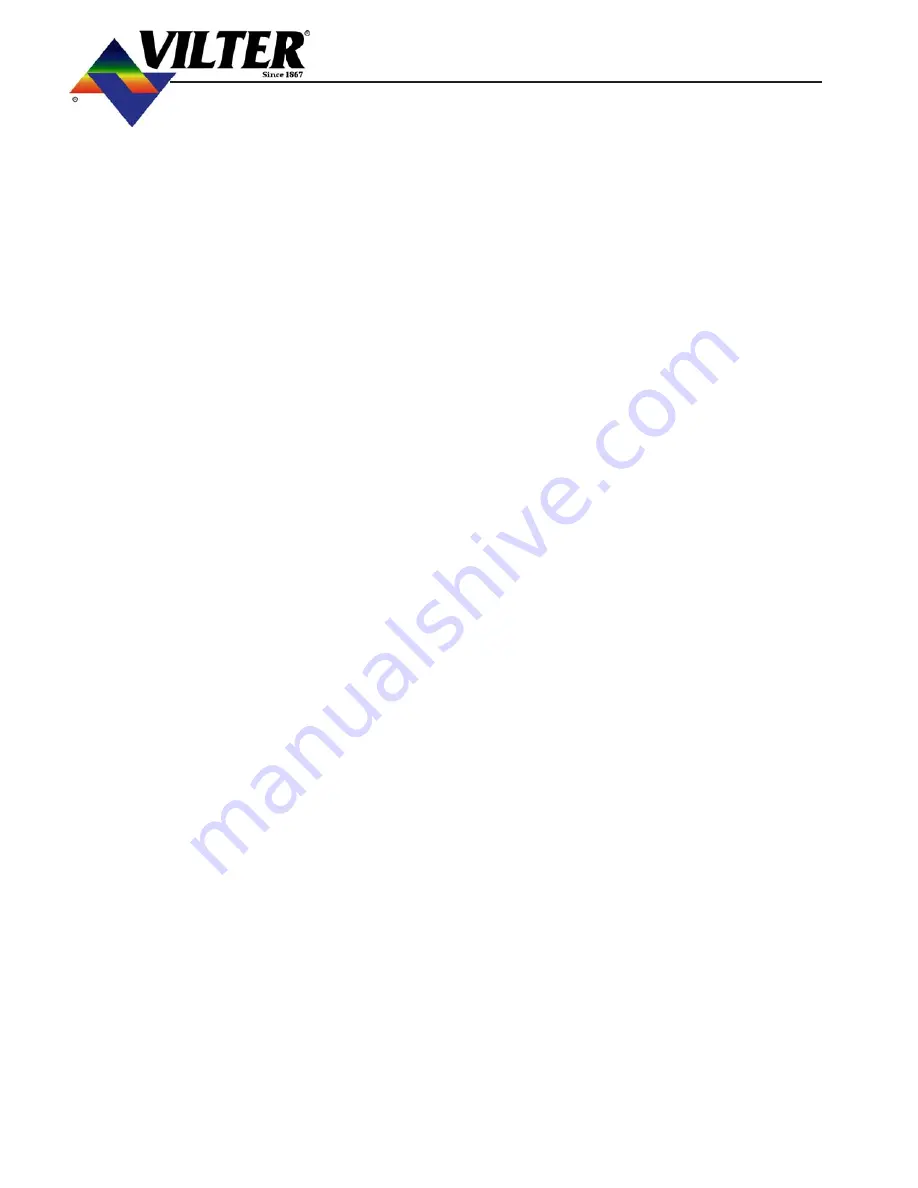
28
Installation
16.
Flush out sediment, etc. from water circuits.
17.
Clean all oil strainers.
18.
Clean suction strainer – compressors.
19.
Check motors and fans for shaft wear and
end play.
20.
Check operation and general condition of
microprocessor and other electrical controls.
21.
Clean all water strainers.
22.
Check drains to make sure water will flow
away from equipment.
23.
Drain and clean entire oil system at receiver
drain. Recharge with new clean moisture
free oil. For proper procedure for changing
micronic oil filter and charging oil into the
system, see Start-Up and Operation section.
24.
Check compressor coupling. For integrity
and alignment.
25.
Check oil pump for wear.
26.
Check the calibration of the microprocessor
pressure transducers and RTD’s for accuracy.
27.
Check mounting bolts for compressor and
motor.
F.
System Leaks
There are any number of reasons why leaks de-
velop in a refrigeration system (i.e. such as dry-
ing out of valve packing, yielding of gaskets, im-
proper replacement of valve caps and loosening
of joints due to vibration). For these reasons, the
need for periodic leak testing cannot be over-em-
phasized. Similarly, when any service operations
are performed on the system, care should be exer-
cised to insure all opened flanges are tightened,
all plugs that were removed are replaced with a
suitable thread filling compound, all packing
glands on valve stems are tightened, and all valve
caps are replaced. When operation is restored,
all joints opened or any valves moved during the
servicing should be checked for leaks.
G.
Year Round Operation
On a continual basis:
1.
Guard against liquid slugging of compres-
sor.
2.
Maintain unit in clean condition and paint
as necessary.
3.
Grease valve stems and threads for the valve
caps.
When refrigeration equipment is operated 24
hours a day year round, it is highly recommended
that a yearly check of all internal parts be made
(see Service Section). While the highest mate-
rial standards are maintained throughout all
Vilter compressors, continuous operation and any
presence of dirt may prove injurious to the ma-
chine. To forestall needless shutdowns or pre-
vent possible machine breakdowns, the side cov-
ers should be removed yearly, and a visual in-
spection be made of the internal parts. In this
way, a small amount of time spent checking
machine conditions once a year may prevent
extensive shutdowns later with subsequent prod-
uct loss and expensive repairs.
Summary of Contents for VSM 71-701
Page 1: ...1 VPN 35391S February 2006 Rev 05 Price 60 00...
Page 2: ...2...
Page 20: ...20...
Page 52: ...53 Pre Start Up Check List...
Page 99: ...99 Recommended Spare Parts List...
Page 104: ...104 Gate Rotor...
Page 110: ...110 Main Rotor VSS...
Page 112: ...112 Main Rotor VSR...
Page 114: ...114 Slide Valve Cross Shafts and End Plate...
Page 118: ...118 Capacity Slide Volume Slide Carriage Assembly Slide Valve Carriage Assembly...
Page 134: ...134 Miscellaneous Frame Components VSS Screw Compressor VSR Mini Screw Compressor...
Page 138: ...138 C FlangeAdapter Components 630 620 610 640 601 641 630 601 620 610 640 641 642 650 651...
Page 140: ...140 Replacement Parts Tools...
Page 144: ...144 GaterotorAssembly...
Page 148: ...148 Main Rotor Slide Valve Cross Shafts and End Plate Models 71 401 Only Counter clockwise...
Page 152: ...152 Main Rotor Slide Valve Cross Shafts and End Plate Model 501 701 Only Clockwise...
Page 154: ...154 Volume Ratio Capacity Slide Carriage Assembly Slide Valve Carriage Assembly...
Page 158: ...158 Miscellaneous Frame Components Model VSM 501 701 Model VSM 71 401...
Page 160: ...160 Replacement Parts Accessories Housing Accessories C Flange Assembly...
Page 166: ...166 Haight Pumps...
Page 170: ...3 Refrigerating Specialties Division...
Page 236: ......
Page 237: ......
Page 238: ......
Page 243: ......
Page 244: ...168...