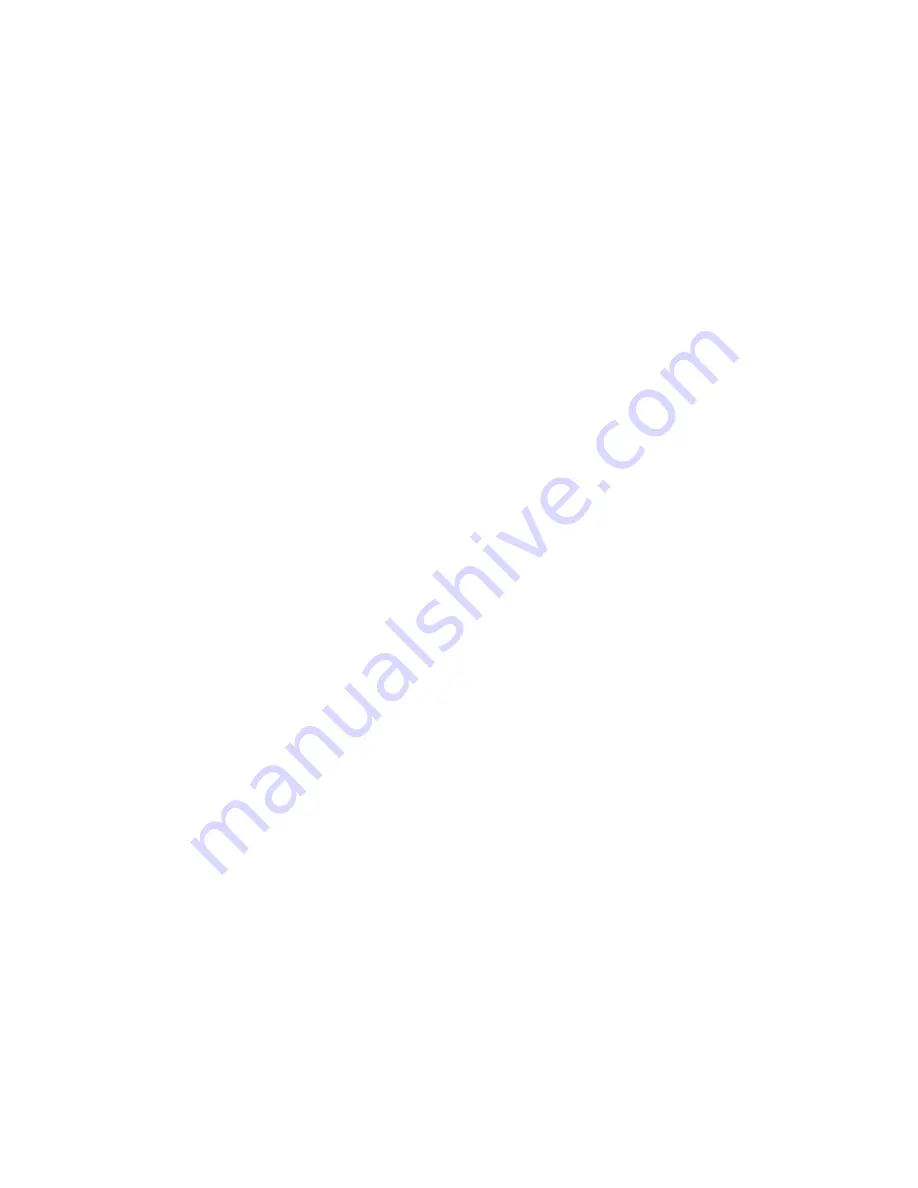
BULLETIN 10-11 /
Page 7
3. Wax
— Certain systems are contaminated with small amounts
of wax which will precipitate at low temperatures in systems
with Refrigerants 22 or 502. Since the TEV represents the first
cold point in the refrigeration cycle, wax is most likely to form
at the valve port.
It is sometimes difficult to observe the wax in a valve because it
may exist in solid form only at very low temperatures. By the
time the valve has been taken apart, the temperature has
increased enough to cause the wax to melt and thus become
difficult to detect. When wax is suspected, it can usually be
detected on the pin and seat by packing the valve in dry ice
while disassembling.
Remedy
— Clean the valve with solvent before reassembling
the valve. The Sporlan HH style Catch-All Filter-Driers have a
special activated charcoal desiccant that is designed to remove
wax in the liquid line before it causes trouble. Therefore, to
prevent wax problems, use these HH style driers (e.g., C-415-
S-HH) on all low temperature systems using Refrigerants 22 or
502.
4. Refrigerant shortage
— See•All or sight glass in the
liquid line will show bubbles when the system is short of refrig-
erant charge. Before adding more refrigerant however, be sure
the bubbles are not produced by other causes (See Paragraphs
A-2
and
A-5
).
A lack of refrigerant charge may also be detected by a hissing
sound at the TEV. Some systems not equipped with a liquid line
sight glass will have test cocks or other devices for checking the
refrigerant level in the receiver.
Remedy
— Add enough refrigerant to obtain desired result.
5. Gas in the liquid line
— As explained in Paragraphs
A-2
and
A-4
, liquid line vapor can be produced by a partially
plugged strainer or drier and by a shortage of refrigerant charge.
In addition, gas in the liquid line can be caused by air or other
non-condensable gases in the system or by excessive pressure
losses in the liquid line as a result of:
■
Long or undersized line.
■
Liquid line vertical lift.
Remedy
— Verify the correct liquid line size for the equiva-
lent length and system tonnage. Consult liquid line sizing data
published in many manufacturers’ catalogs and in textbooks. If
undersized, repipe with the correct size.
Determine amount of vertical lift, and obtain the resulting
pressure loss from Table 3, Bulletin 10-9. Using the subcooling
calculation example provided in the "subcooling" section of
Bulletin 10-9, find required subcooling necessary to prevent
gasification with the existing pressure losses. Provide the
necessary subcooling by using one of the methods described on
Page 1.
6. Misapplication of internally equalized valve or
incorrect location of external equalizer
— If the
pressure drop through the evaporator exceeds the predetermined
values shown in Table 1, Bulletin 10-9, an externally equalized
valve must be used. When an externally equalized valve is used,
the equalizer connection should be made at a point in the suction
line that will reflect the pressure existing in the line at the bulb
location.
Remedy
— Replace internally equalized valve with one
having an external equalizer.
If external equalizer is installed incorrectly, change to correct
location. See Page 3.
7. Insufficient pressure drop across valve
— One of the
factors that influence expansion valve capacity is the pressure
drop that exists between the inlet and outlet. Anything
contributing to a reduction in this pressure drop will reduce valve
capacity. Abnormally low condensing pressures, excessive liquid
line pressure losses (even with adequate subcooling), undersized
distributor nozzle or distributor tubes may also be responsible for
a very low net pressure drop across the valve port.
Remedy
— Remove source of pressure loss, or install valve
with adequate capacity at the reduced pressure drop. If inlet
pressure to valve is low due to low condensing pressure, raise
pressure.
If the refrigerant distributor nozzle is undersized replace with
correct size. See Bulletin 20-10.
8. Dead thermostatic element or wrong thermo-
static charge
— If the element has partially or completely
lost its thermostatic charge, the valve will be unable to feed
sufficient refrigerant or will remain closed. A wrong charge may
cause insufficient feed also.
Remedy
— Replace the element if it is dead. If charge is
incorrect, replace with proper selective charge. See Bulletin 10-9.
9. Charge migration (CP series, ZP series, and VGA
charges only)
— In order for valves with these charges to
maintain control at the bulb, the bulb must be kept at a lower
temperature than the element (diaphragm case). If the thermo-
static charge does migrate to the element because of a lower
element temperature, the valve will throttle.
Detection
— Warm the element with a cloth saturated with
hot water. If this produces more refrigerant feed and reduces the
superheat to normal, charge migration is responsible for the
starved evaporator.
Causes
—
■
Insufficient pressure drop between the valve outlet and bulb
location, possibly due to an oversized distributor nozzle or no
nozzle at all.
■
Excessive pushrod leakage, which allows the leaking refrig-
erant to cool the diaphragm case before passing into the
equalizer line. This is a rare occurrence and should be
carefully checked before arriving at this conclusion.
■
Cold location of TEV, or condensate drippage on the
diaphragm case.
Remedies
—
■
Install distributor nozzle correctly sized in accordance with
nozzle sizing procedure given in Sporlan Bulletin 20-10.
■
On valves with packed pushrod construction, remove element
and tighten the pushrod packing nuts.
■
Relocate the TEV away from cold outlet air, or condensate
drippage.
10. Undersized valve
Remedy
— Install valve sized in accordance with procedure
given in Bulletin 10-9, or Bulletin 10-10.
11. High Superheat adjustment
Remedy
— Turn the adjusting stem counter clockwise until
the correct superheat is indicated.
12. Feed-back from another valve
— Review instructions
for Bulb Location and Installation, Page 2.
Remedy
— Check the bulb temperature and calculate the
superheat. If superheat is normal but too little refrigerant is
Summary of Contents for VSM 71-701
Page 1: ...1 VPN 35391S February 2006 Rev 05 Price 60 00...
Page 2: ...2...
Page 20: ...20...
Page 52: ...53 Pre Start Up Check List...
Page 99: ...99 Recommended Spare Parts List...
Page 104: ...104 Gate Rotor...
Page 110: ...110 Main Rotor VSS...
Page 112: ...112 Main Rotor VSR...
Page 114: ...114 Slide Valve Cross Shafts and End Plate...
Page 118: ...118 Capacity Slide Volume Slide Carriage Assembly Slide Valve Carriage Assembly...
Page 134: ...134 Miscellaneous Frame Components VSS Screw Compressor VSR Mini Screw Compressor...
Page 138: ...138 C FlangeAdapter Components 630 620 610 640 601 641 630 601 620 610 640 641 642 650 651...
Page 140: ...140 Replacement Parts Tools...
Page 144: ...144 GaterotorAssembly...
Page 148: ...148 Main Rotor Slide Valve Cross Shafts and End Plate Models 71 401 Only Counter clockwise...
Page 152: ...152 Main Rotor Slide Valve Cross Shafts and End Plate Model 501 701 Only Clockwise...
Page 154: ...154 Volume Ratio Capacity Slide Carriage Assembly Slide Valve Carriage Assembly...
Page 158: ...158 Miscellaneous Frame Components Model VSM 501 701 Model VSM 71 401...
Page 160: ...160 Replacement Parts Accessories Housing Accessories C Flange Assembly...
Page 166: ...166 Haight Pumps...
Page 170: ...3 Refrigerating Specialties Division...
Page 236: ......
Page 237: ......
Page 238: ......
Page 243: ......
Page 244: ...168...