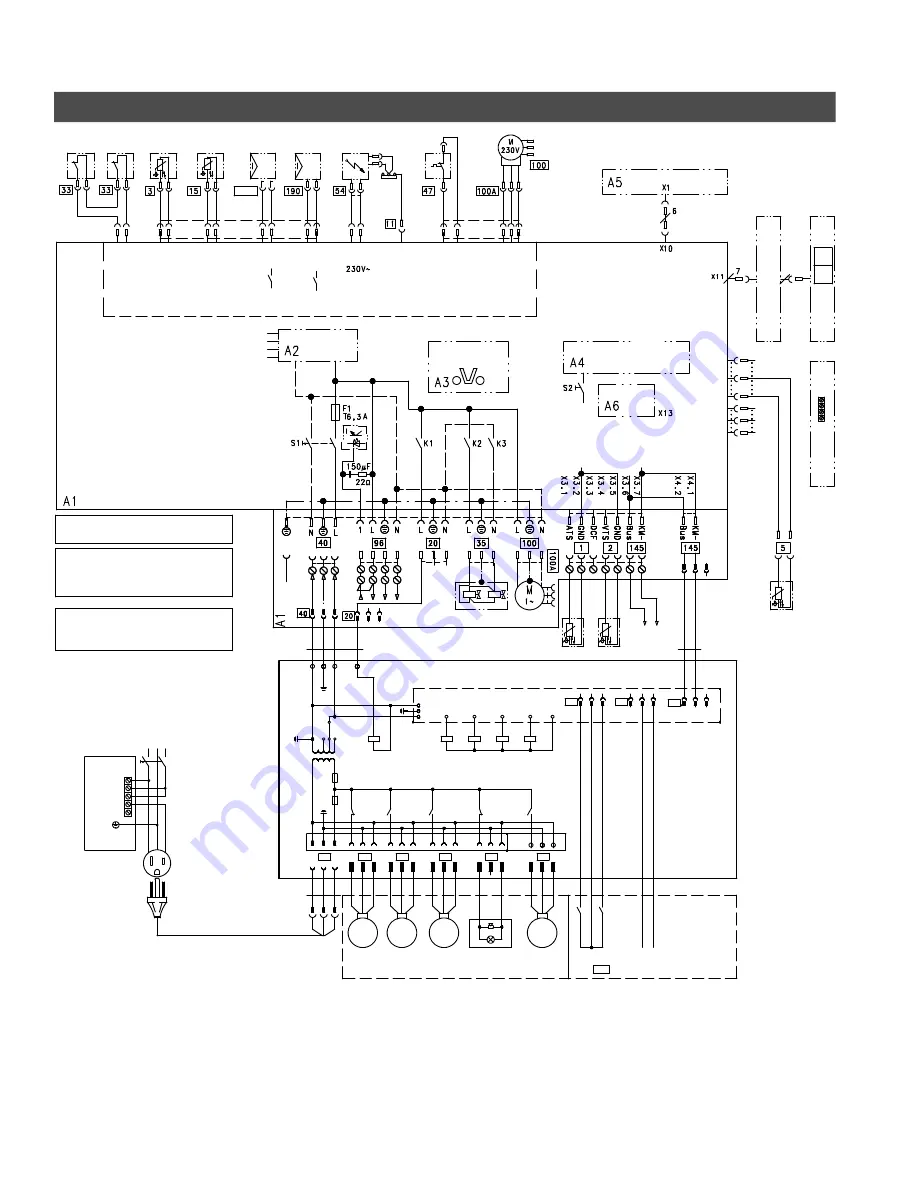
Additional Information
68
Wiring Diagram
See legend for this wiring diagram on next page.
5
4
4
3
2
0
7
v
1
.5
N
G
L
L
G
N
L
G
N
L
G
N
L
G
N
N
G
L
T
L
G
N
1
2
3
1
2
3
1
2
3
N
N
G
L
L
G
1
2
3
BL
BN
N
G
L
120VAC
M
120VAC
M
120VAC
M
DISCONNECT
SWITCH
A
P1
P2
L2
L1
MAIN
MAIN POWER SUPPLY
120V, 60HZ, 12A
N G L
L
O
W
W
A
T
E
R
C
U
T
--
O
F
F
S
A
F
E
T
Y
D
E
V
IC
E
--
T
Y
P
IC
A
L
120VAC
WALL
RECEPTACLE
PUMP
DHW
SYSTEM
PUMP
BOILER
PUMP
ONLY ONE FUNCTION/ACCESSORY MAY BE
ASSIGNED TO EACH CONNECTION.
WARNING! DISCONNECT POWER
CAUTION! LABEL ALL WIRES PRIOR TO
DISCONNECTION WHEN SERVICING CONTROLS.
WIRING ERRORS CAN CAUSE IMPROPER AND
DANGEROUS OPERATION. VERIFY PROPER
IF ANY OF THE ORIGINAL WIRE AS SUPPLIED
WITH THE APPLIANCE MUST BE REPLACED
IT MUST BE REPLACED WITH ITS
EQUIVALENT.
BEFORE SERVICING BOILER.
OPERATION AFTER SERVICING.
INTERNAL CONNECTIONS
GC131 BURNER IGNITION MODULE
POWER PUMP MODULE
120VAC
M
DHW
RE--CIRC.
--
+
--
+
FAULT ALARM
OUTPUT
EXTERNAL
DEMAND
SEE
143
EXTERNAL
0--10V
SIGNAL
PUMP
99 C
210 F
40
20A
21
20
50
28
145
144
143
X
9
.4
X
9
.5
X
9
.6
X
9
.7
X
9
.1
2
X
9
.1
3
X
9
.9
X
9
.8
K4
X
8
.2
X
8
.1
X
6
.1
X
2
.2
X
2
.1
X
8
.6
P
W
M
X
8
.4
H
A
L
L
X
8
.3
G
N
D
X8.1
X8.10
X8.11
X9.1
X9.3
X9.4
OR
L
O
N
X
1
L
O
N
X
2
A7
A8
A8
X
1
K
M
K
1K
M
K
2
120VAC
1 2 3 4 5 6 7
Conduit
KM--BUS
Accessories
X1 X2
X2
--X1
K3
K1
K2
K4
K5
120--230V
300VA
--5%
+5%
K5
240VAC
K1
K2
K3
K4
24VDC
24VDC
24VDC
24VDC
JUMPER
H1
PCB
3xAWG16
1
F
A
2
1
T
2
F
FIELD CONNECTIONS
o
o
L
A
T
O
T
.
x
a
m
A
8
C
A
V
0
2
1
:
S
T
U
P
T
U
O
X
9
.1
0
X
9
.1
1
190A
K5
C
A
V
0
3
2
6
1
G
W
A
x
4
WH
GN
BK
RD
s
u
b
--
M
K
X3
N
L2
L1
G
T3.5A