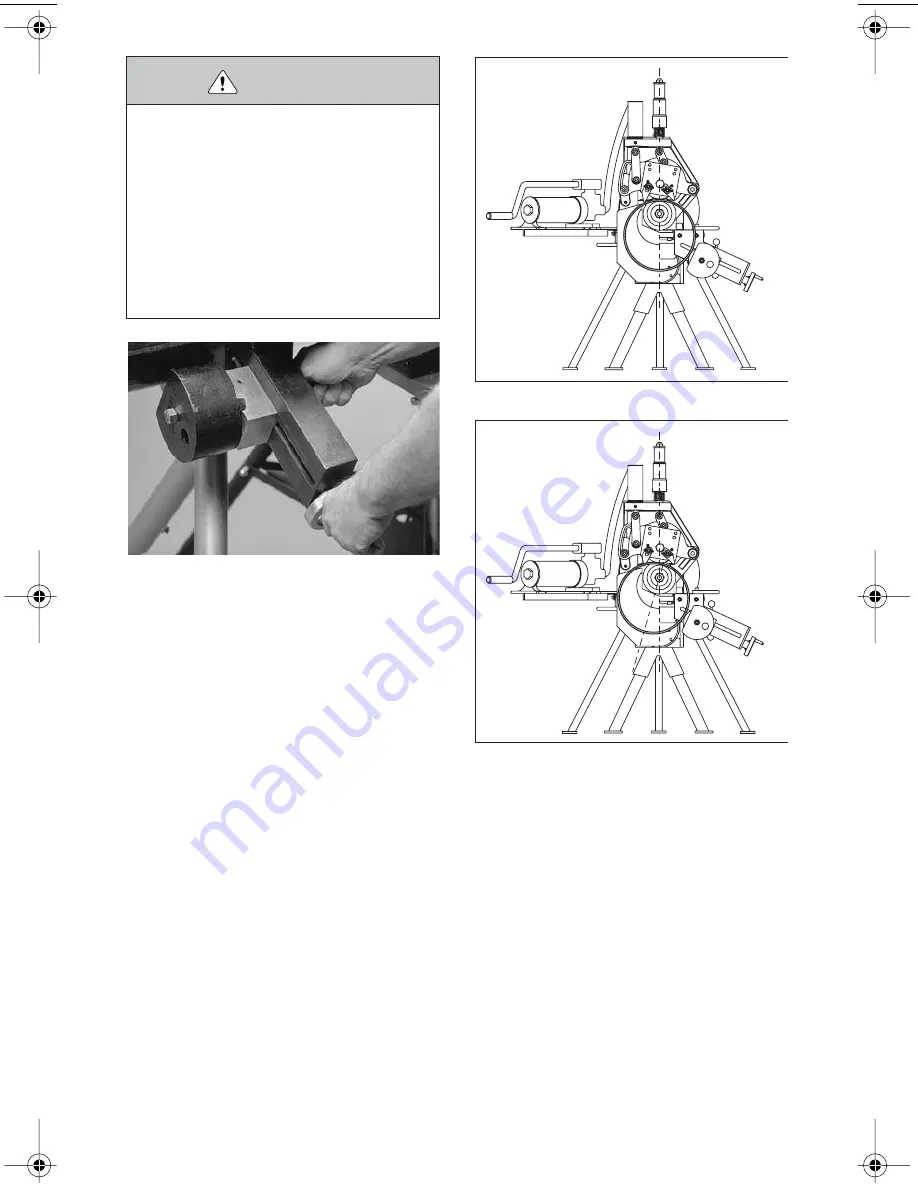
VE272SFS Roll Grooving Tool
17
7.
Using the hand wheel, advance the sta-
bilizer roller inward until the roller lightly con-
tacts the pipe. Tighten the stablizer locking
handle. Refer to Figures 3 and 4 on this page
for proper positioning.
8.
Complete all adjustments and groove
the pipe. Refer to the "Grooving Operation"
section, starting on page 20. Observe the
stabilizer roller while grooving. It should
remain in contact with the pipe, and the pipe
should rotate smoothly without swaying from
side to side. If the pipe is not rotating smoothly
or is swaying from side to side, adjust the sta-
bilizer roller further inward. Continue the
grooving operation and make further adjust-
ments, as necessary. DO NOT adjust the sta-
bilizer too far inward, since it will skew the
pipe to the left and off center, resulting in ex-
cessive pipe-end flare.
Figure 3 - “CORRECT”
Figure 4 - “INCORRECT”
CAUTION
• DO NOT adjust the stabilizer to push the pipe to the
left and off center from the rolls. Increased pipe-end
flare and shortened roll life will result if the pipe is
pushed to the left and off center.
• Assembly of couplings on pipe that exceeds the
maximum allowable flare dimension may prevent
proper pad-to-pad assembly of coupling housings
and may cause gasket distortion/damage.
Failure to prepare pipe in accordance with all instruc-
tions may cause joint failure, resulting in personal
injury and/or property damage.
TM-VE272SFS 3776 Rev_B.fm Page 17 Friday, December 3, 2004 12:10 PM
Summary of Contents for VE272SFS
Page 2: ......