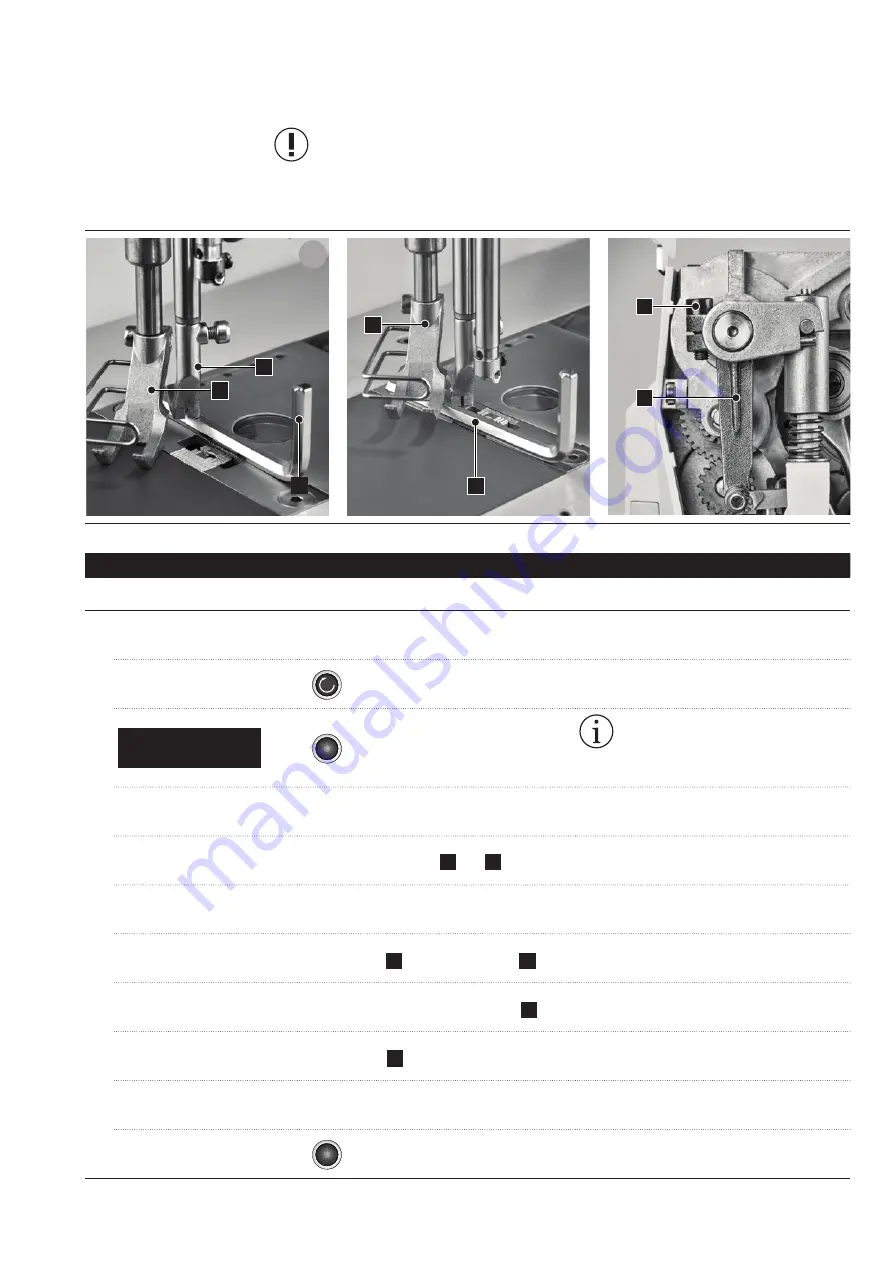
1
3
1
3
2
5
4
2
54
05/2019
VETRON 5000 - FLAT BED MACHINE - SERVICE MANUAL
55
05/2019
VETRON 5000 - FLAT BED MACHINE - SERVICE MANUAL
03. ADJUSTMENT
19.
TOP FEED STROKE
DISPLAY
STEP
DESCRIPTION
»
TOP FEET STROKE
01
Activate the
ADJUSTMENT WIZARD
(see 02.01. / Page 19).
02
» Until chapter
19
appears on the display.
03
9
e
t
T
t
e
p
u
o
f
if
d
e
p
l
1
s
» Confirm.
INFO:
The
stitch length
is set
to
0mm
and the top feet stroke
to
5mm
. Footlifting via pedal is possib-
le but the electrical
machine run is blocked.
04
Remove the needle.
05
Tighten the sewing feet
1
and
2
to the machine as in image 1.
06
By turning the mechanical hand wheel, the feet should lift equally
07
Loosen screw
5
and move the lever
4
until the lift of the feet is equal.
08
Check the equal lift with the allen key
3
.
09
Tighten screw
5
.
10
Remount the needle and feet correctly.
11
» Confirm to proceed to the next step.
NOTE:
The sewing feet should lift evenly at a top feed stroke of
5mm.
Summary of Contents for 5000
Page 1: ...5000 5100 SERVICE MANUAL 05 2019 ...
Page 2: ......
Page 3: ...5000 5100 SERVICE BOOK 05 2019 STANDARD 5000 5010 5020 5030 5040 LONGARM 5100 5110 5120 5130 ...
Page 8: ...06 05 2019 VETRON 5000 FLAT BED MACHINE SERVICE MANUAL INDEX ...
Page 20: ...18 05 2019 VETRON 5000 FLAT BED MACHINE SERVICE MANUAL 01 OPERATING ELEMENTS ...
Page 102: ...100 05 2019 VETRON 5000 FLAT BED MACHINE SERVICE MANUAL 04 SHORT THREAD CUTTER ...
Page 106: ...104 05 2019 VETRON 5000 FLAT BED MACHINE SERVICE MANUAL 05 MAINTENANCE ...
Page 110: ...108 05 2019 VETRON 5000 FLAT BED MACHINE SERVICE MANUAL 06 WEAR PARTS ...