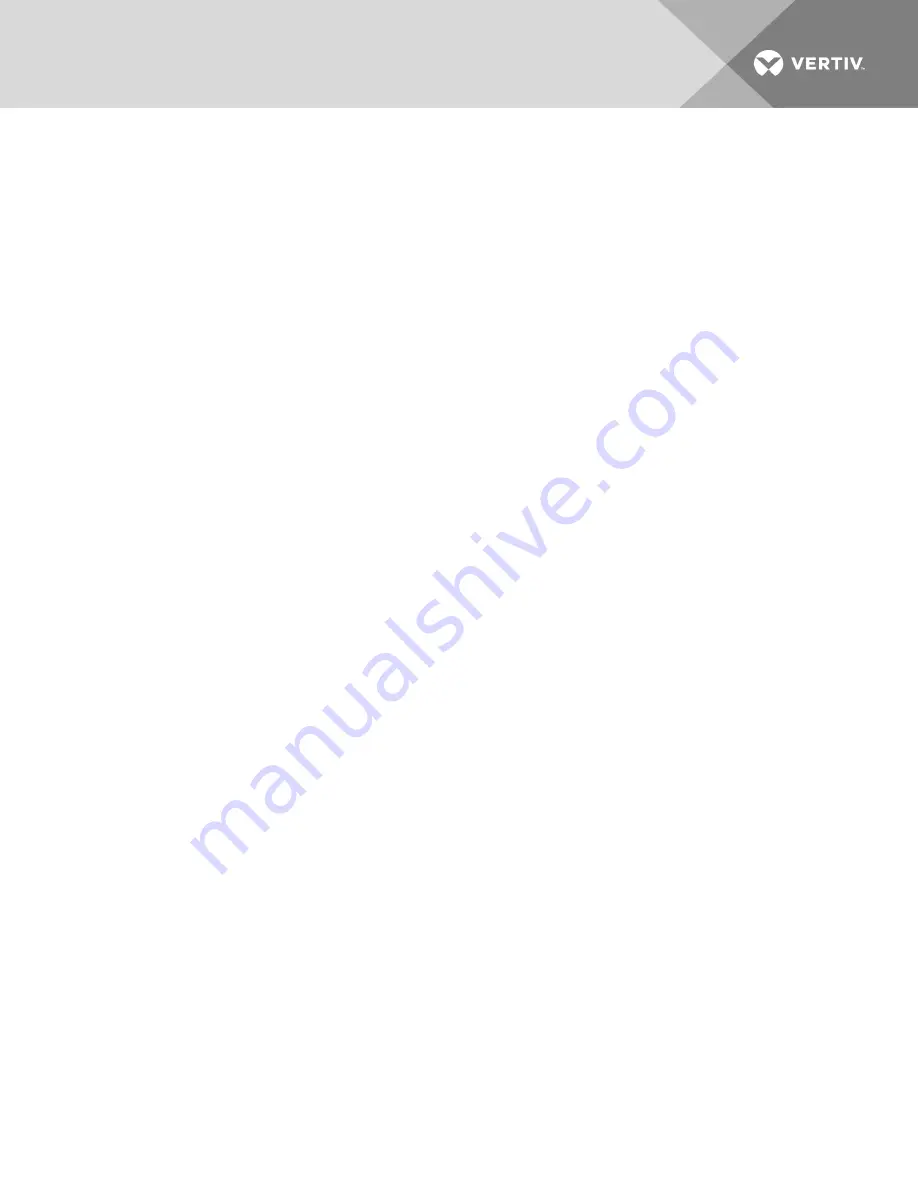
Multiple pump packages require a check valve at the discharge of each pump to prevent back-flow
through the standby pump(s). To extend the service life of the drycooler and the system's pumps, install
filters/strainers in the supply line to the pumps. These filters should have a 16-20 mesh screen and be a
type that can be easily replaced or cleaned.
Installing hose bibs at the lowest point of the system will facilitate filling.
Keep piping runs as straight as possible; avoid unnecessary bends and minimize additional fittings.
Allow for pipe expansion from warm fluids. Piping should be isolated from the building with vibration-
isolating supports. Use soft, flexible material to seal between pipes and wall openings to prevent pipe
damage.
Consideration of the minimum glycol temperature to be supplied from the drycooler and the pipe routing
will determine if the glycol supply and return lines should be insulated. Insulation will prevent
condensation on the glycol lines in low ambient conditions.
Completed piping system should provide maximum leak-prevention. Welded or high-temperature
soldered joints should be used where possible. Threaded pipe joints, if needed, can be made with tightly
drawn Teflon™ tape.
Clean and prepare all pipe connections before joining. Be careful not to allow solder/joining debris to get
inside the lines during the connection process.
6.11.2 Expansion Tanks, Fluid Relief Valves, Air Management and Other Devices
An expansion tank must be provided for expansion and contraction of the fluid due to temperature
change in this closed system. Vents are required at system high points to vent trapped air when filling the
system. A fluid pressure relief valve is also a necessary piping component.
All systems must have an air management system to ensure proper component operation and system
performance. There are several methods that can be used to manage the air within a closed loop hydronic
system. Depending on the method chosen, the system may include one or more of the following ancillary
components: tank-steel (expansion, compression, diaphragm or bladder), air separator and air vent.
Consult your local engineer to determine which method will be used and where these components must
be installed.
Depending on the complexity of the system, various other devices may be specified—refer to site-specific
drawings. Some of the devices that may be required are: pressure gauges, flow switches, automatic air
separator, tempering valves, standby pumps and sensors for electrical controls.
NOTICE
Risk of frozen coolant fluid. Can cause piping rupture, coolant fluid leaks and building damage.
Immediately following the use of water for leak testing or system cleaning, charge the tested system with
the proper percentage of glycol and water for your coldest design ambient. Complete system drain-down
cannot be ensured and damage to the system could result from freezing of residual water.
6.12 Electrical Supply
Line voltage electrical service is required for all models. Refer to equipment nameplate regarding wire size
and circuit protection requirements. Electrical service must conform to national and local electrical codes.
Refer to electrical schematic when making connections.
Each unit is shipped from the factory with all internal unit wiring completed.
Vertiv
| Liebert® Xtreme Density™ System Design Manual |
141
Summary of Contents for Liebert XD Series
Page 1: ...Liebert Xtreme Density System Design Manual...
Page 18: ...Vertiv Liebert Xtreme Density System Design Manual 18 This page intentionally left blank...
Page 20: ...Vertiv Liebert Xtreme Density System Design Manual 20 This page intentionally left blank...
Page 66: ...Figure 4 2 Overall dimensions Vertiv Liebert Xtreme Density System Design Manual 66...
Page 88: ...Figure 4 21 Liebert XDV dimensions Vertiv Liebert Xtreme Density System Design Manual 88...
Page 152: ...Vertiv Liebert Xtreme Density System Design Manual 152 This page intentionally left blank...
Page 166: ...Figure 7 7 Modules on a single chain Vertiv Liebert Xtreme Density System Design Manual 166...
Page 167: ...Figure 7 8 Modules on two chains Vertiv Liebert Xtreme Density System Design Manual 167...
Page 182: ...Vertiv Liebert Xtreme Density System Design Manual 182 This page intentionally left blank...
Page 199: ......