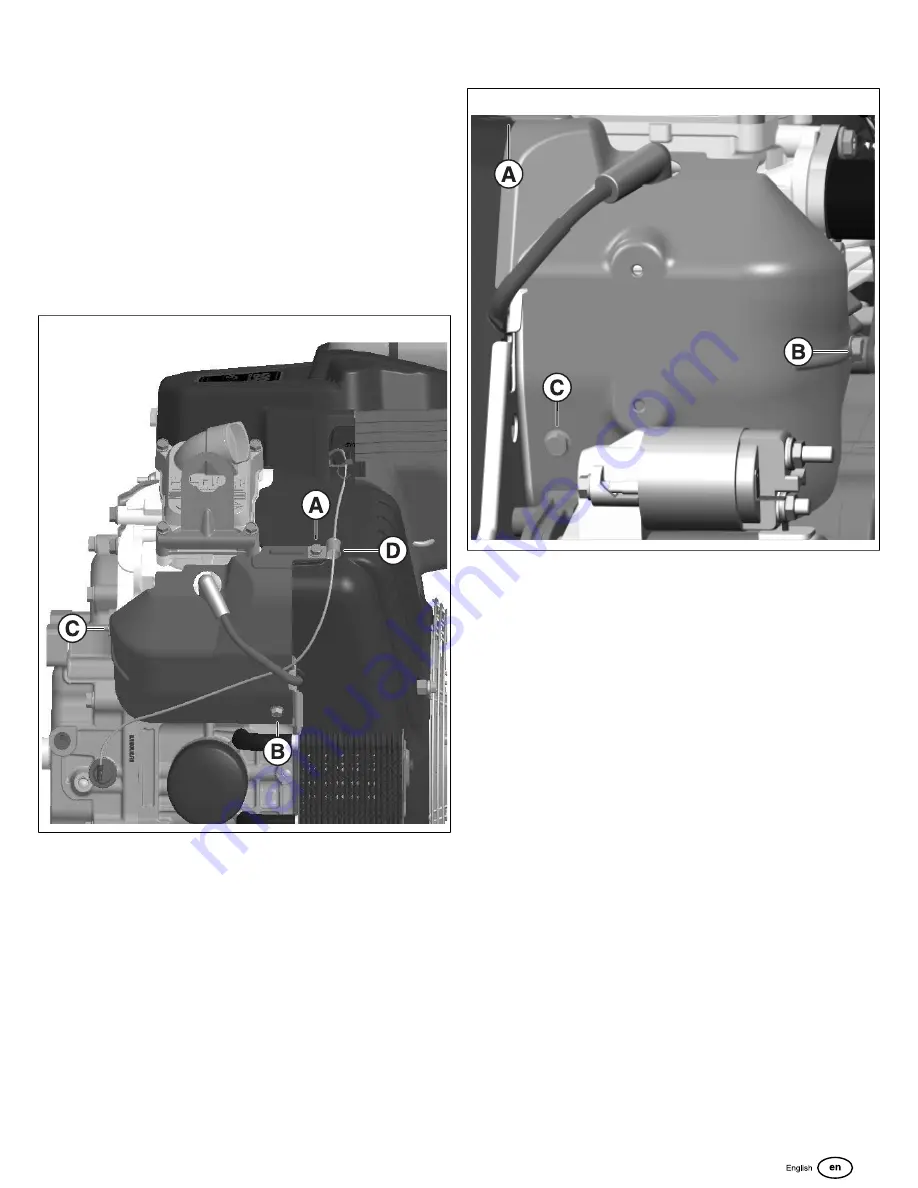
Cylinder Air Guides
1. On the oil filter side of the engine, install the cylinder air
guide to the cylinder head. Align the air guide mounting
holes to the threaded holes in the cylinder head.
NOTE:
A wire routing clamp is installed on the top air guide
mount. The oil pressure switch wire is secured by the wire
clamp and the clamp is secured by the air guide mounting
fastener. Install the wire clamp and make sure that the oil
pressure switch wire is routed correctly before torqueing the
fastener.
2. Start by hand the 3 fasteners (
A, B, C
Tighten to
90 lb-in
(10.2 Nm).
211
NOTE:
A wire routing clamp (
D
) is installed on the top air
guide mount. The oil pressure switch wire is secured by
the wire clamp and the clamp is secured by the air guide
mounting fastener. Install the wire clamp and make sure
that the oil pressure switch wire is routed correctly before
torqueing the fastener.
3. On the starter motor side of the engine, install the
cylinder air guide to the cylinder head. Align the air guide
mounting holes to the threaded holes in the cylinder
head.
4. Start by hand the 3 fasteners (
A, B, C
Tighten to
90 lb-in
(10.2 Nm).
212
Throttle Control
Depending on your engine's model and trim, a manual
detent throttle may be equipped. For engines equipped with
a Cyclonic Air Cleaner assembly, the throttle control may
be mounted above the key switch cover at the front of the
engine. For engines equipped with a Low-Profile Air Cleaner
assembly, the throttle control may be remotely mounted. For
engine mounted throttle controls, proceed as follows. For
remote mounted throttle control, see your equipment's repair
manual for installation instructions.
153
Summary of Contents for BIG BLOCK M540000
Page 46: ...Special Tools Image Chart 30 47...
Page 74: ...84 75...
Page 75: ...85 76 vanguardpower com...
Page 81: ...94 82 vanguardpower com...
Page 111: ...Vanguard Model 540000 145 112 vanguardpower com...
Page 113: ...Vanguard Model 610000 146 114 vanguardpower com...
Page 136: ...176 137...