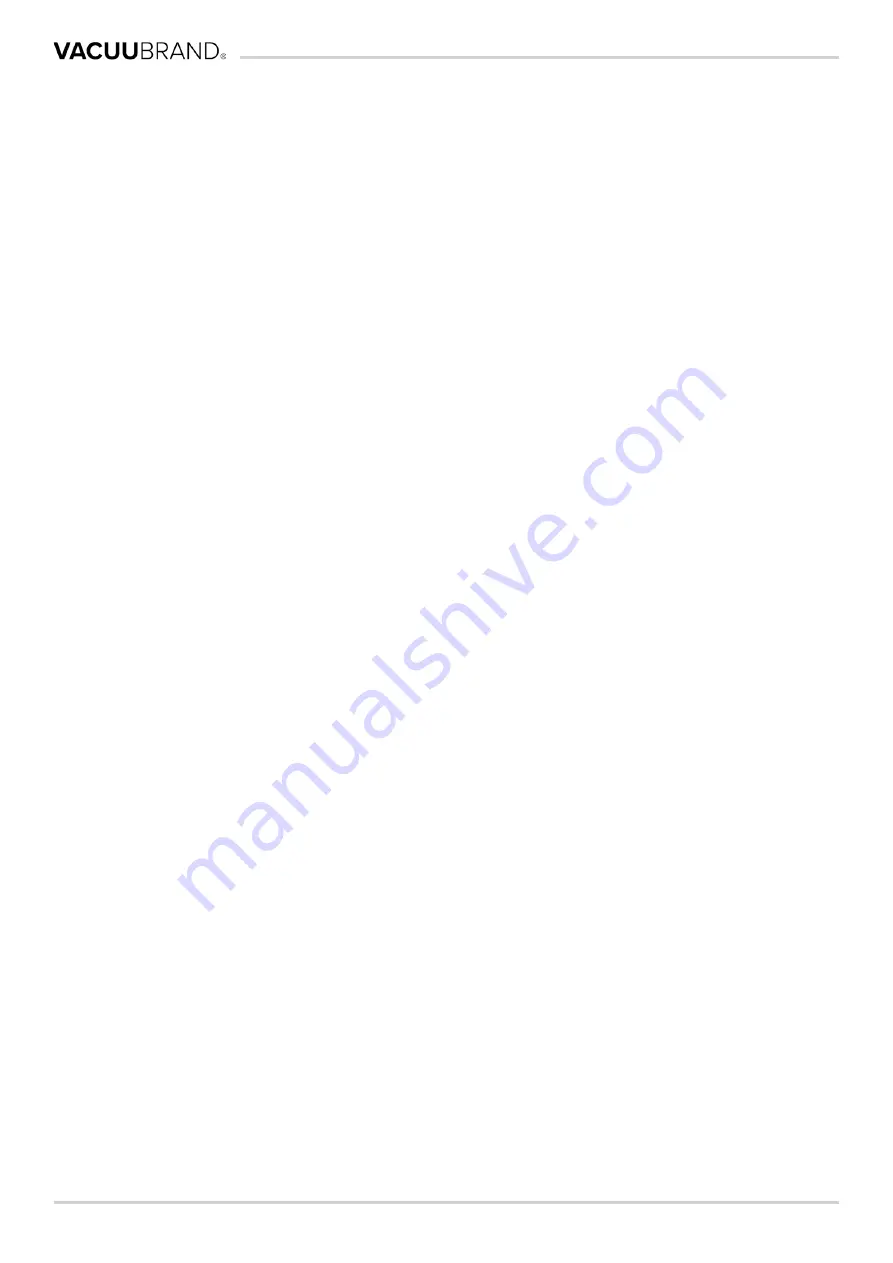
25
20901559_EN_RE_RZ_V7_230523
Product description
3
3 Product description
Product description
The
Rotary vane pumps Rx y
Rotary vane pumps Rx y
are oil‑sealed vacuum pumps for
the vacuum range from atmospheric pressure to the fine vacuum
range in the laboratory.
With the gas ballast valve closed, the rotary vane pump shuts
off vacuum tight. This, in turn, prolongs the intervals between oil
changes and improves corrosion resistance. The oil system incor
‑
porates an oil pump; this forced‑lubrication system ensures an
adequate supply of oil to the pump unit even at high inlet pres
‑
sures. A mechanical retaining valve in the oil system prevents oil
suck‑back into the vacuum system.
Product description
Summary of Contents for RE 2.5
Page 24: ...24 20901559_EN_RE_RZ_V7_230523 Introduction ...
Page 40: ...40 20901559_EN_RE_RZ_V7_230523 Installation and connection ...
Page 48: ...48 20901559_EN_RE_RZ_V7_230523 Installation and connection ...
Page 73: ...73 20901559_EN_RE_RZ_V7_230523 Appendix 8 8 8 8 CU Certificate CU Certificate CU Certificate ...
Page 76: ...76 20901559_EN_RE_RZ_V7_230523 ...
Page 77: ...77 20901559_EN_RE_RZ_V7_230523 ...
Page 78: ...78 20901559_EN_RE_RZ_V7_230523 ...