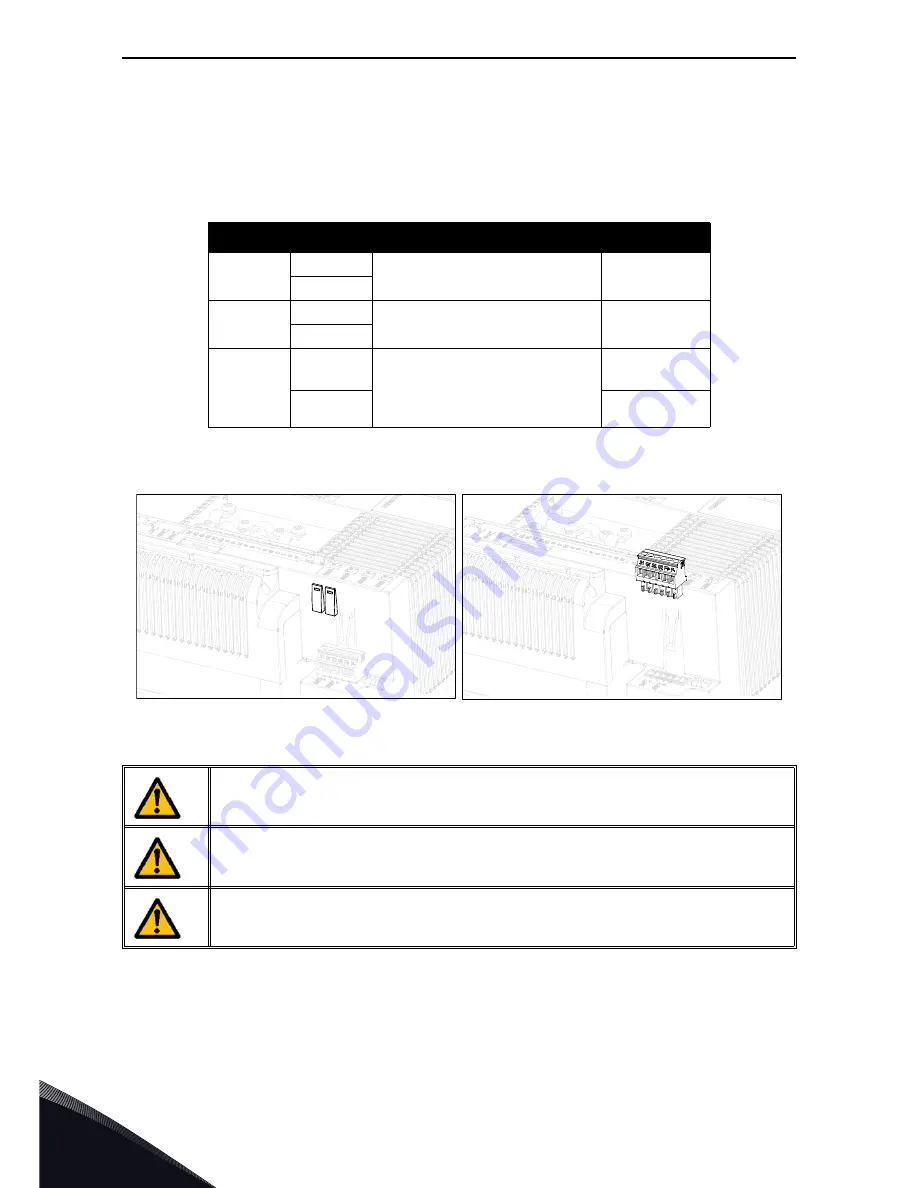
9
vacon • 106
Safe Torque Off
Local contacts: http://drives.danfoss.com/danfoss-drives/local-contacts/
9.5
Connections
To make the STO function available and ready to be used, both STO jumpers have to be removed.
They have been located in front of the STO terminal to mechanically prevent the insertion of the STO
inputs. For the correct configuration, see the following table and the Figure 71.
Figure 71. Removing the STO jumpers from the control unit.
The following examples show the basic principles for wiring the STO inputs and the STO output
feedback. Local standards and regulations should be always followed in the final design.
Table 47. STO connector and data signals.
Signal
Terminal
Technical information
Data
STO1
S1
Insulated digital input 1
(interchangeable polarity)
24V
±
20%
10...15 mA
G1
STO 2
S2
Insulated digital input 2
(interchangeable polarity)
24V
±
20%
10...15 mA
G2
STO
feedback
F+
Insulated digital output for STO
feedback
(CAUTION! Polarity must be
respected)
24V
±
20%
15 mA max.
F-
GND
Make sure that the AC drive is switched off before cabling.
When the STO function is used,
the IP-class of the drive may not be reduced below
IP54
. The IP-class of drive is IP66. It can be reduced by the wrong use of the cable
entry plates or the cable glands.
Disconnect both STO jumpers to allow the cabling of the terminals.