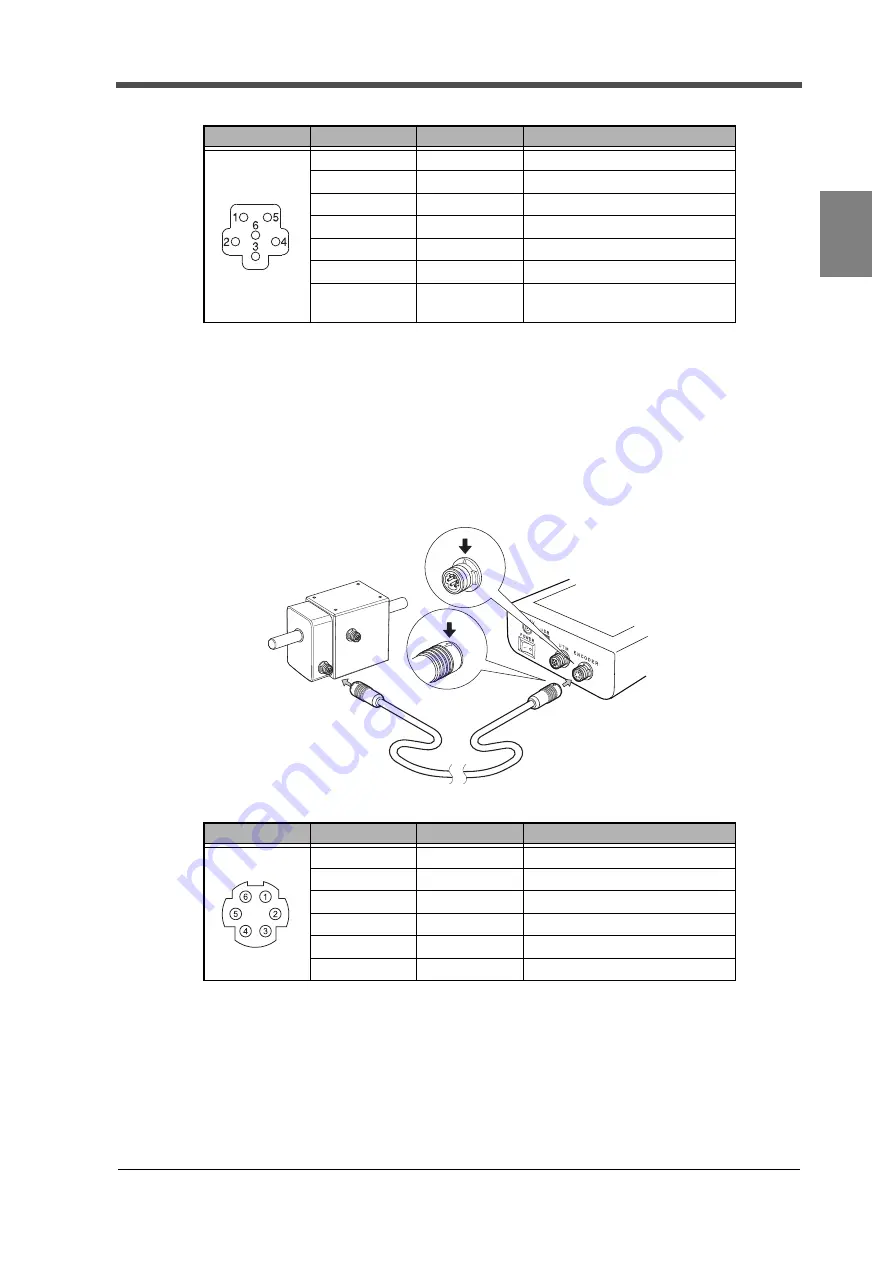
9
2
Connection
9
Connection
Chapter
2
●
Pin assignment
* The wire colors correspond with the color of cable included with UTM
Ⅱ
.
* Compatible connector: HR30-6P-6P manufactured by HIROSE ELECTRIC CO., LTD.
(Model without optional connector: CN90)
2-3.
Rotary encoder connection
The UTM
Ⅱ
rotary encoder can be connected easily with a dedicated cable. The cable has no
polarity. Connect UTM
Ⅱ
while paying attention to the direction of the connector.
●
Pin assignment
* The wire colors correspond with the color of cable included with UTM
Ⅱ
rotary encoder.
* Compatible connector: HR30-6P-6S manufactured by HIROSE ELECTRIC CO., LTD.
(Model without optional connector: CN91)
Pin-out
Pin number
Wire color
Signal name
1
Red
PWR+ (+24V)
2
Black
PWR- (0V)
3
Green
SIG IN (±5V DC)
4
White
SIG GND
5
Yellow
PULSE IN+
6
Brown
PULSE IN-
Shield
Braided wire
* The shield is not connected to the
UTM
Ⅱ
case.
Pin-out
Pin number
Wire color
Signal name
1
-
NC
2
Red
PWR+ (+5V)
3
Transparent
Z-phase output
4
Black
B-phase output
5
Blue
A-phase output
6
Shield (green)
PWR GND