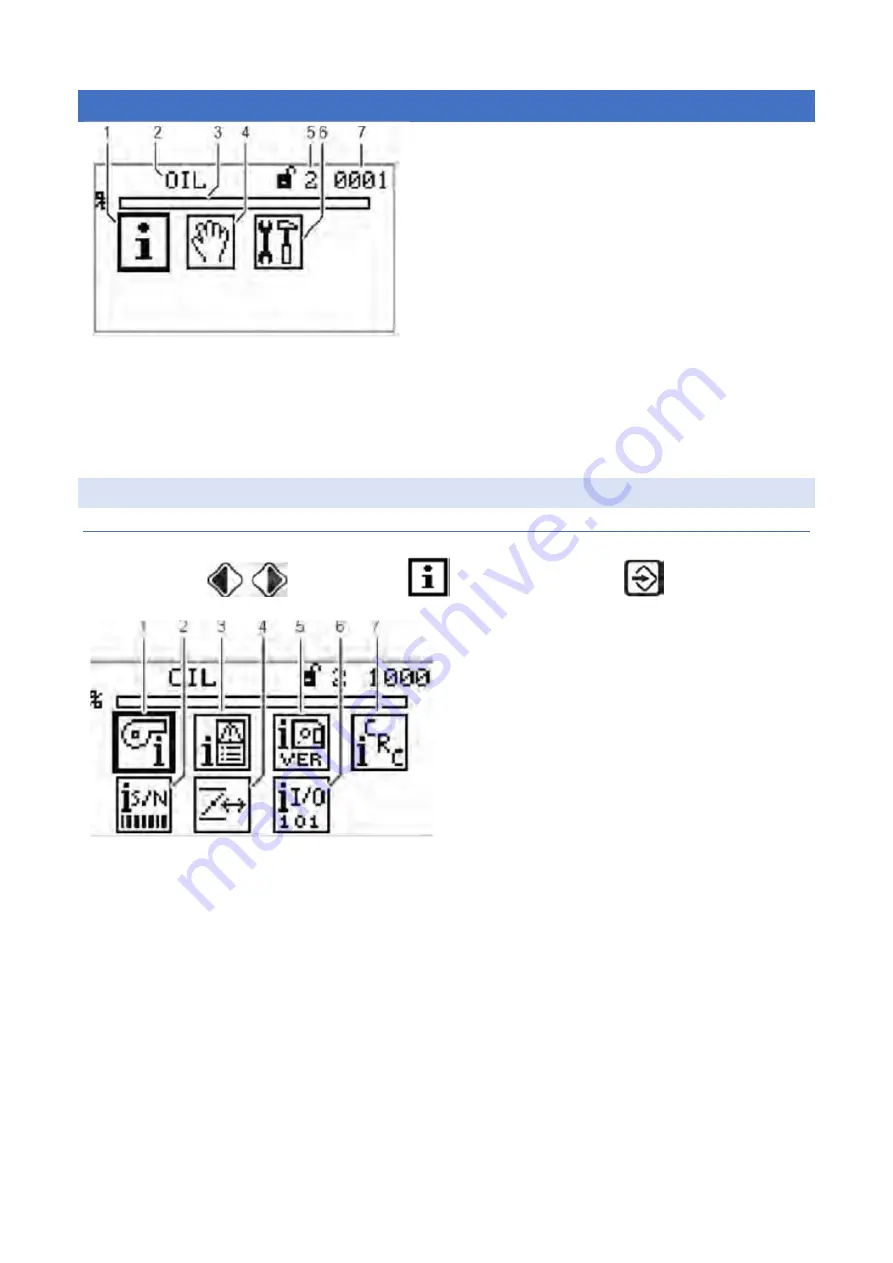
6
3
MAIN MENU
1
INFORMATION menu path [selected]
2
Display of fuel used
3
Bargraph of internal firing‐rate in % (0 ‐100)
4
MANUAL menu path
5
Access level 2
6
SETTINGS menu path
7
Window number
3.1
INFORMATION MENU PATH
3.1.1 INFORMATION PATH:
Use the cursor keys
to select the path
and confirm this with Enter
1
Selected burner information [selected]
2
Serial number
3
Fault history
4
Confguration of actual value of actuating outputs (display only)
5
Software version
6
Digital inputs/outputs
7
Check sum display
Summary of Contents for LAMTEC BT3 Series
Page 46: ...PART IV MAINTENANCE 46...
Page 47: ......
Page 98: ......
Page 99: ......
Page 100: ......
Page 114: ......
Page 123: ......
Page 124: ......
Page 125: ...WB1 QF A QF B...
Page 126: ......
Page 127: ......
Page 129: ......
Page 130: ......
Page 131: ...INTERFACE...
Page 132: ...R1 R2 POT...
Page 135: ......
Page 136: ......
Page 137: ......