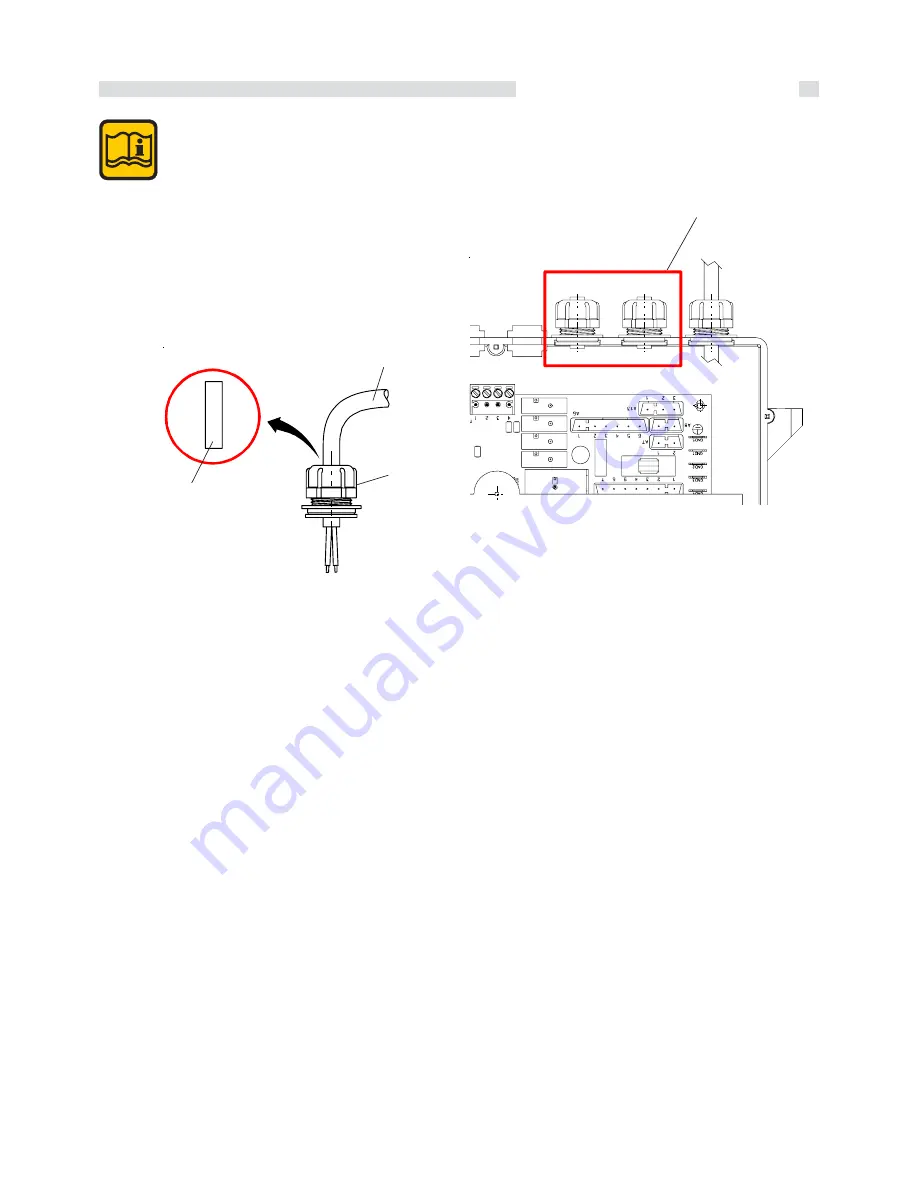
25
Instructions for the installer
If connecting a thermostat, use one of the
extractable grommets which are present on the
electrical panel, carrying out the following
operations:
- Remove the grommet 1
- Unscrew the ring nut 2
- Remove the plastic ‘tap’ 3
- Insert the cable 4
- Wire the electrical connections onto the terminal
strip
- Replace the grommet 1 in its housing
- Tightly close the ring nut 2 to block the cable
Remove
1
2
3
4
Summary of Contents for Alkon Cargo 35
Page 1: ...ALKON CARGO 35 INSTALLATION AND SERVICING MANUAL 00332603 2nd edition 04 2008 ...
Page 46: ...NOTE ...
Page 47: ...NOTE ...