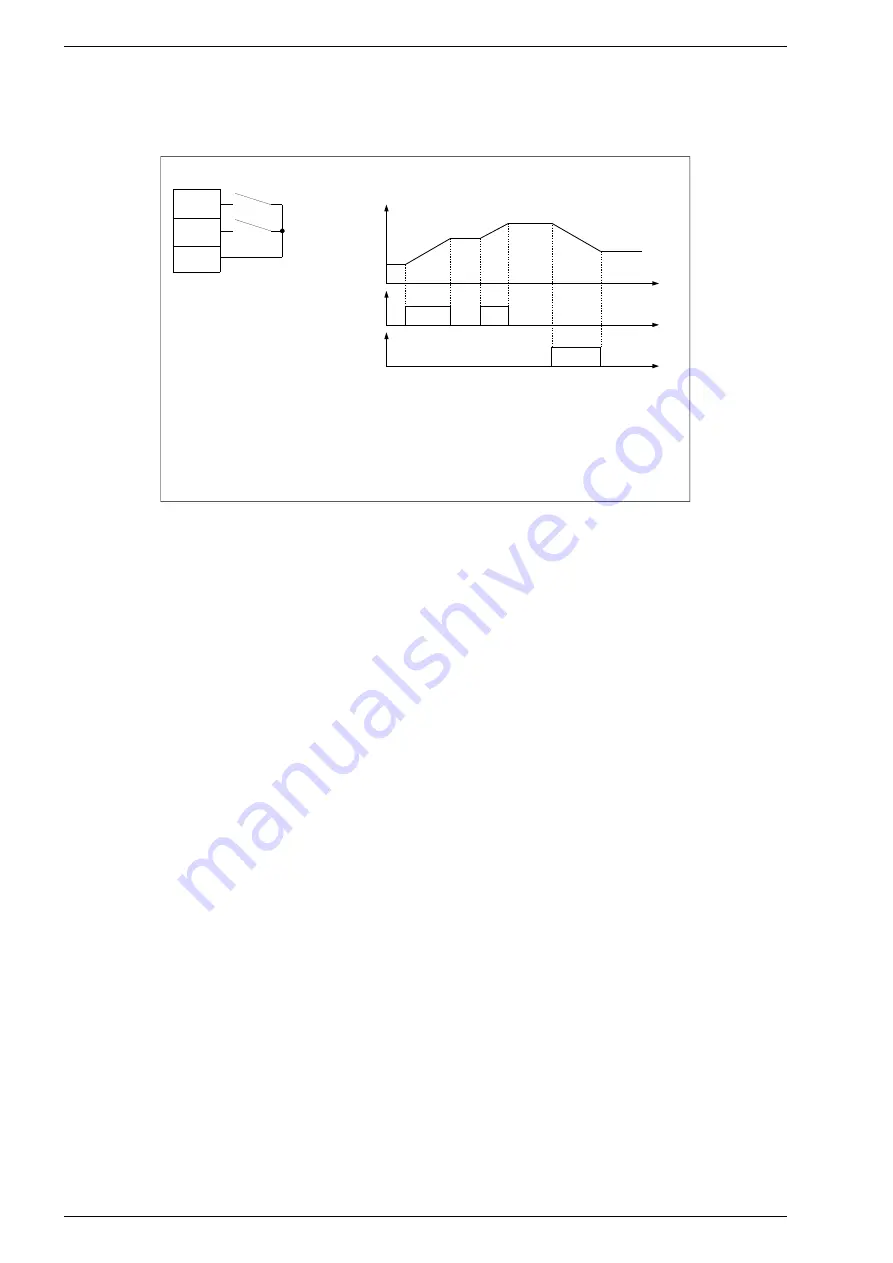
Section 4. Configuration of the frequency converter
4.2.5. Motopotentiometer
Motopotentiometer is designed to “increase/decrease” drive speed by two buttons. An exemplary way of connecting the
"Increase" and "Decrease" keys to the drive is shown in fig. 4.6a. In this example, the digital inputs DI3 and DI4 are
used. Fig. 4.6b. shows action of the device.
DI3
Increase
Reduce
a)
Increase
Reduce
f sel.
b)
time
Increase and reduce of drive speed depends on:
- constanta of motor-potentiometer (par. 2.23)
- dynamic of electric drive (par. 1.30 ... 1.36)
DI4
24V
Fig. 4.6 - Connection and illustration of a motopotentiometer device operation.
Information "mP" on the display in CONTROL STATE
mode confirms enabling of the motorpotentiometer’s ref.-unit
To set the output frequency of the drive using a motopotentiometer, set the output frequency of the drive
in the selected parameter responsible for the source of the reference signal 2.2 (for “control place” A) or 2.3
(for “control place” B) to “
138 MotPot
”. Fig. 4.6a corresponds to a situation when par. 2.20 = “
003 In.C3
”
and par. 2.21 = “
004 In.C4
”.
Note:
Digital input DI3 is default using as a source of external fail 1 (par. 3.10 = “
003 In.C3
”), so before using DI3 please
move a source of external fail 1 to another digital input DI or just turn it off. Similar situation occurs with digital input DI4.
Digital input DI4 is default using as a source of external reset, so before using DI4 please move a source of external
reset to another digital input DI or just turn it off (par. 3.70).
There are four available modes of motopotentiometer operation:
0
,
1
,
2
and
3
.
Modes 0, 1 and 2 should be used only when current referencing-unit (par. 2.2/par. 2.3) is set on “
004 MotPot
”.
Mode 3 can be used regardless of setting of current referencing-unit.
•
Stopping the converter In mode
0
will cause reset of motopotentiometer settings.
•
In mode
1
settings of motopotentiometer will be stored and there is no possibility of changing it while the drive
is stopped.
•
In mode
2
settings of current referencing-unit are traced by motopotentiometer so switching from current
referencing-unit to motopotentiometer's referencing is made very easily.
•
In mode
3
configuration of motopotentiometer is stored and there is possibility of changing it while the drive is
stopped.
4.2.6. Other possibilities of the frequency converter control
Other possibilities arise from the analysis of the block diagram of control (see section 4.2.1). From the major
options it is possible to allocate
Change of control place A / B e.g. using a digital input - par. 2.1
Mixed control – e.g. referencing frequency from the control panel and a START / STOP signal from digital inputs,
Control through RS232/RS485 connection (see section 13),
Referencing frequency from an output of the PID controller (see section 8),
Advanced functionalities related to the use of built-in PLC or a control system of group of pumps (see section 10
and the following sections).
32
Frequency converter MFC710 type. TWERD Power Electronics