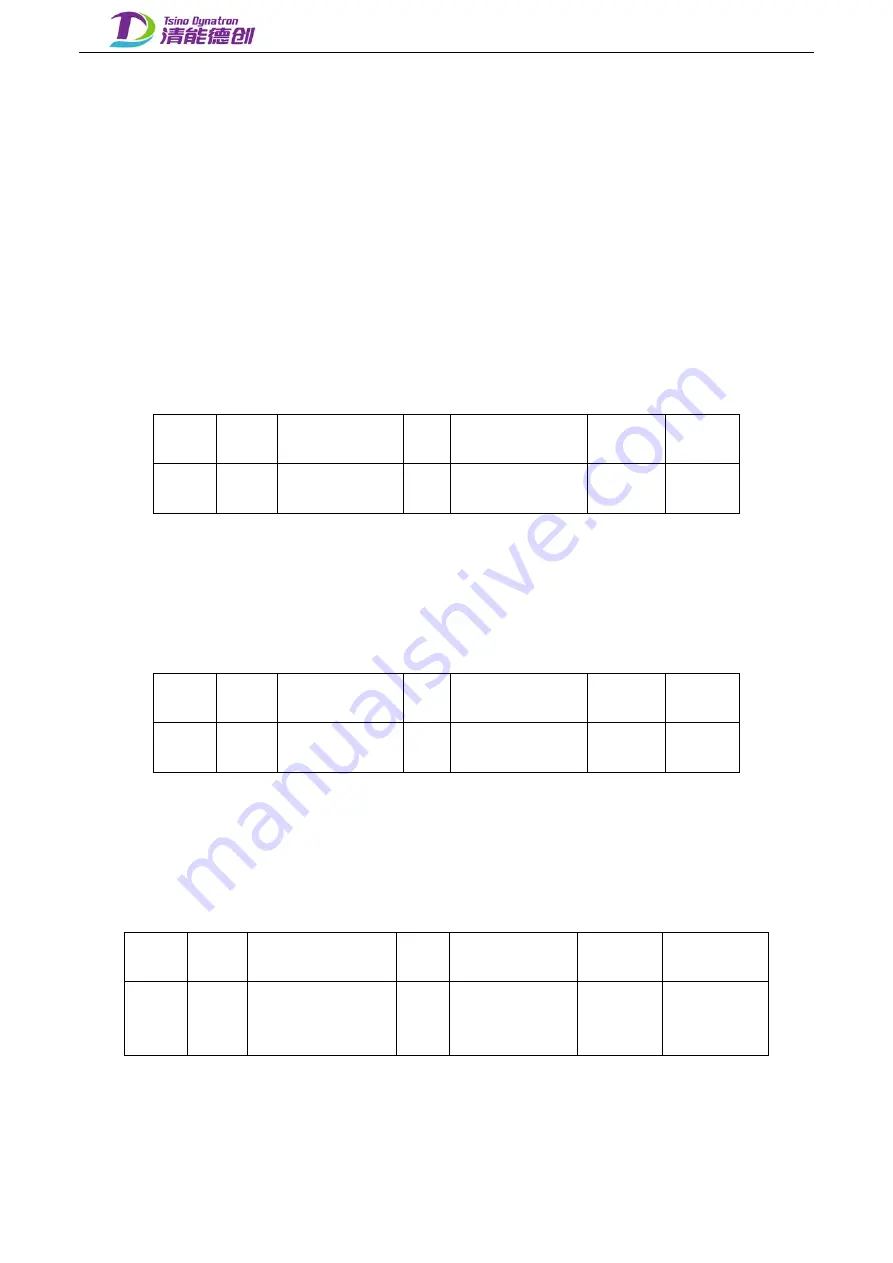
Tsino-Dynatron Electrical Technology (Beijing) Co., Ltd.
b. The position loop gain and velocity loop gain should not be increased any more once vibration is generated
in the mechanical system, and proper adjustment should be done to eliminate vibration.
c. The servo gain adjustment has close relations with the mechanical rigidity. Normally, as for high-rigidity
machines, the overall system responsiveness can be improved by improving the servo gain. However, as for
low-rigidity machines, an over-high gain may cause vibration, as a result, the overall system responsiveness fails to
be improved, and the expected performance requirements cannot be met. Therefore, in occasions requiring high
responsiveness, high-rigidity machines are needed to avoid mechanical resonance.
Velocity regulator
8.2.1
Generally, during gain adjustment, the responsiveness of the velocity loop should be higher than that of the
position loop, otherwise system vibration can be caused. Firstly, adjust the velocity loop parameters, and then
position loop parameters.
Number
Index
Name
Unit
Setting range
Default
value
Effective
time
47
0x2044
Velocity Control
Gain1
‰
1~ 2147483647
15000
Immediately
Parameter description:
The greater the set value of velocity control gain 1, the higher the gain, the better
following with the velocity command. However, due to the constraint of mechanical characteristics, an overlarge
value may cause mechanical vibration.
User permission:
User/Engineer.
Parameter permission:
Read and Write
Number
Index
Name
Unit
Setting range
Default
value
Effective
time
49
0x2046
Velocity Control
Gain2
‰
1~ 2147483647
5000
Immediately
Parameter description:
Valid when Byte3 of parameter 0x2065 is set to 0x10. The greater the set value of
the velocity control gain 2, the higher the gain, and the better following with the velocity commands. However, due
to the constraint of mechanical characteristics, a high set value may cause mechanical vibration.
User permission:
User/Engineer.
Parameter permission:
Read and Write
Number
Index
Name
Unit
Setting range
Default
value
Effective time
48
0x2045
Velocity Control
Integration time
constant1
us
125~ 2147483647
20000
Immediately
Parameter description:
Valid when Byte3 of parameter 0x2065 is set to 0x10; The smaller the set value of
velocity control integration time, the better responding to the velocity commands. However, due to the constraint of
mechanical characteristics, a small set value may cause vibration and noise. Increasing the velocity control
188
Summary of Contents for EtherCAT CoolDrive RC Series
Page 1: ...Updated on Update summary Updated version Version number D3 ...
Page 17: ...Tsino Dynatron Electrical Technology Beijing Co Ltd Dimension Drawing of RC3 2 3 2 7 ...
Page 18: ...Tsino Dynatron Electrical Technology Beijing Co Ltd Dimension Drawing of RC4 2 3 3 8 ...
Page 19: ...Tsino Dynatron Electrical Technology Beijing Co Ltd 9 ...
Page 20: ...Tsino Dynatron Electrical Technology Beijing Co Ltd Dimension Drawing of RC6 2 3 4 1 ...