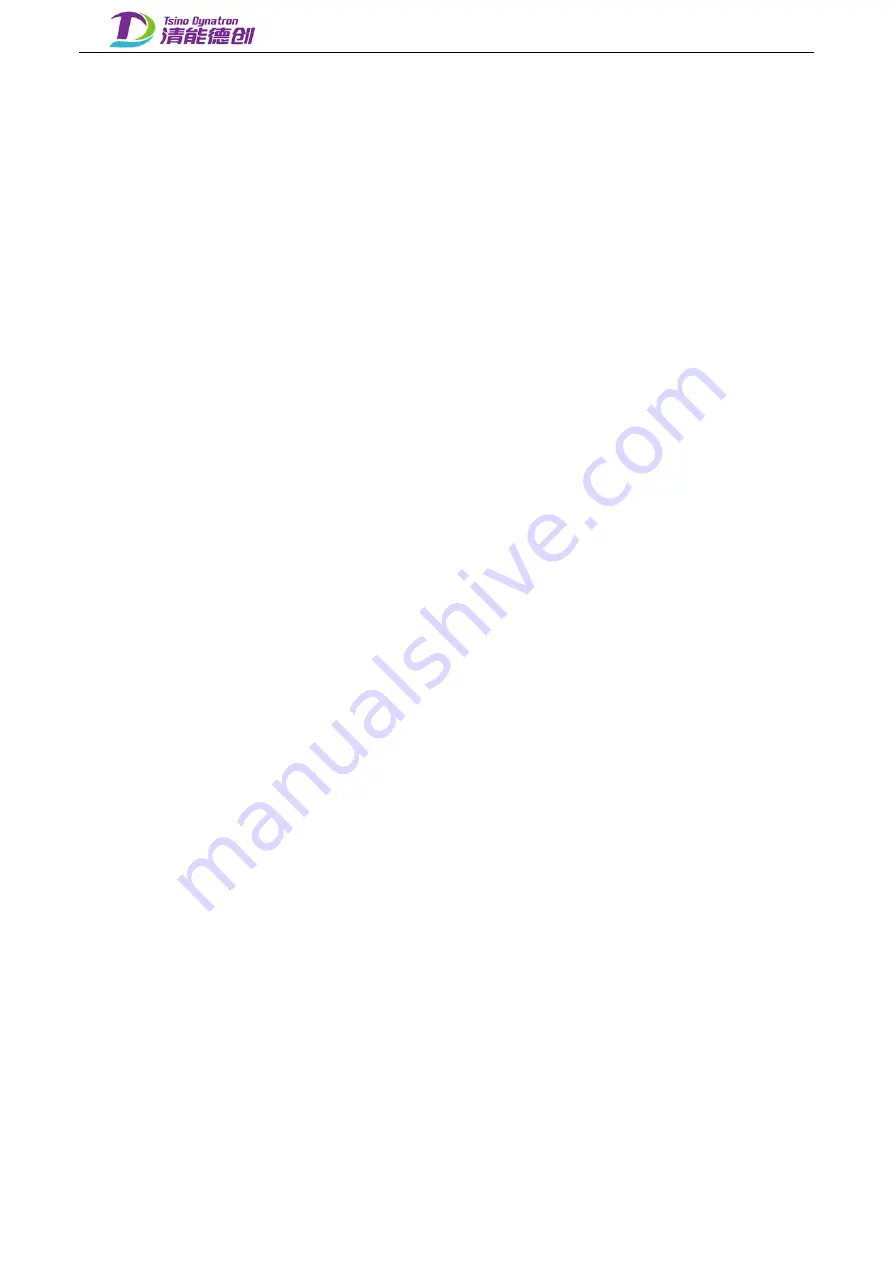
Tsino-Dynatron Electrical Technology (Beijing) Co., Ltd.
0x6075 (motor rated current);
0x6076 (motor rated torque);
0x6080 (max motor speed);
0x20C8 (motor torque constant);
5.1.2.3
Set Encoder Parameters
Set encoder parameters properly, which must be set according to the encoder specifications adaptive to the
motor in real application.
For Hiperface encoder, only need to set Byte1 (absolute encoder model) of 0x2009 (encoder type set) to
0x00 - Hiperface.
For other types of encoder, still need to set 0x2076 (absolute encoder single-turn bits) and 0x2077 (absolute
encoder multi-turn bits) after 0x2009 (encoder type set) is set according to the actual encoder type. For example: If
the encoder of the motor in use is Tamagawa absolute encoder, single-turn 17bit, multi-turn 16bit, set 0x2076 to 17,
and set 0x2077 to 16.
5.1.2.4
Set Regulator Parameters
Set the current control gain and velocity loop gain.
0x2048 (current control gain 1), 0x2049 (current control integration time constant), 0x2044 (velocity control
gain 1), 0x2045 (velocity control integration time constant 1) and 0x2040 (position control gain 1) can be
calculated by the "Parameter identification and tuning function" of the debugging software. Experienced servo
application engineers can also set parameters based on their own experience.
5.1.2.5
Set Motor Rotor Compensation Angle
0x2003 (rotor position compensation angle) must be set for each motor shaft before trial operation. Enter the
value directly if it is already known, or detect it through the following method if it is unknown.
If the motor is not mounted to the mechanical equipment (e.g. not mounted to the robot body), you can detect
it with conventional detection method.
If the motor is already mounted to the mechanical equipment (e.g. mounted to the robot body), please detect it
with static detection method. Set 0x20D1 (rotor compensation angle detection setting) before detection. You can
start with the default value, and make appropriate adjustment if the test fails.
After testing with the method above, you can click "Save detection value" on the test interface or set the
detection value to 0x2003 (rotor position compensation angle) manually. After the rotor position compensation
angle is set, soft reset or power off and restart the drive to perform motor trial operation.
Note: If enter the known rotor compensation angle without detection, please make sure the motor phase
sequence is properly wired.
Trial Operation Through DriveStarter
5.2
Precautions
5.2.1
Make sure the output side of the motor shaft is not connected to any load.
Make sure the DriveStarter commissioning software and RS485 serial drive have been properly installed on
the PC.
Make sure the commissioning cable has been properly connected to X10 commissioning port.
The servo control is DriveStarter.
Do not touch the rotating part of the motor during operation.
For the operations of trial operation through DriveStarter software, please refer to DriveStarter user manual.
32
Summary of Contents for EtherCAT CoolDrive RC Series
Page 1: ...Updated on Update summary Updated version Version number D3 ...
Page 17: ...Tsino Dynatron Electrical Technology Beijing Co Ltd Dimension Drawing of RC3 2 3 2 7 ...
Page 18: ...Tsino Dynatron Electrical Technology Beijing Co Ltd Dimension Drawing of RC4 2 3 3 8 ...
Page 19: ...Tsino Dynatron Electrical Technology Beijing Co Ltd 9 ...
Page 20: ...Tsino Dynatron Electrical Technology Beijing Co Ltd Dimension Drawing of RC6 2 3 4 1 ...