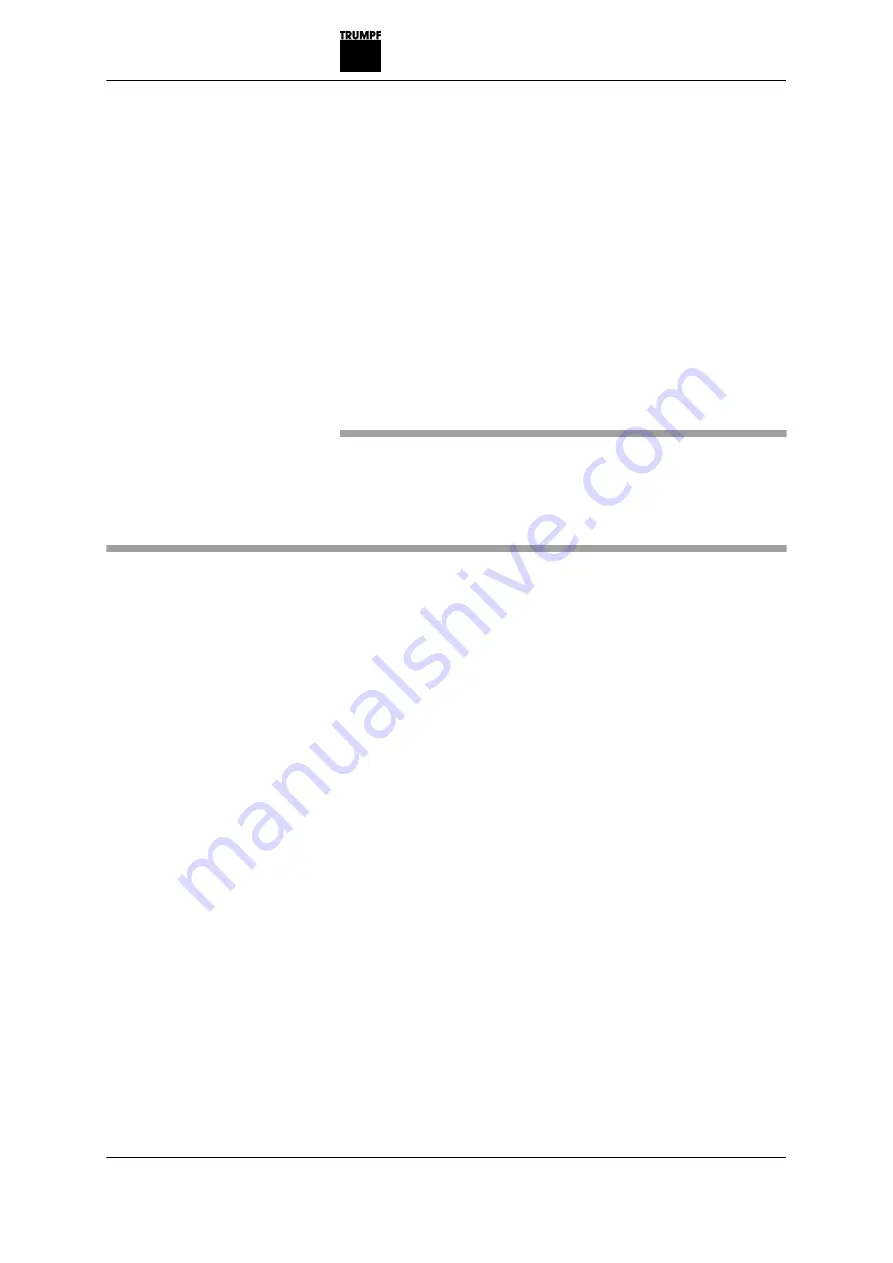
Chapter 1
Safety
1
For your safety
2
Operational safety
2.1
Intended use
2.2
Authorized personnel
3
Hazards
3.1
Dangers due to the open electrical cabinet
3.2
Hazards due to laser radiation
3.3
Dangers handling workpieces
Sharp-edged workpieces
Upper and lower tool
Flange of the workpiece
Positioning the workpiece
Falling workpieces
Improper handling of flat workpieces
Improper handling when bending boxes
B1161en
2019-07-09
Safety
1
‐
1