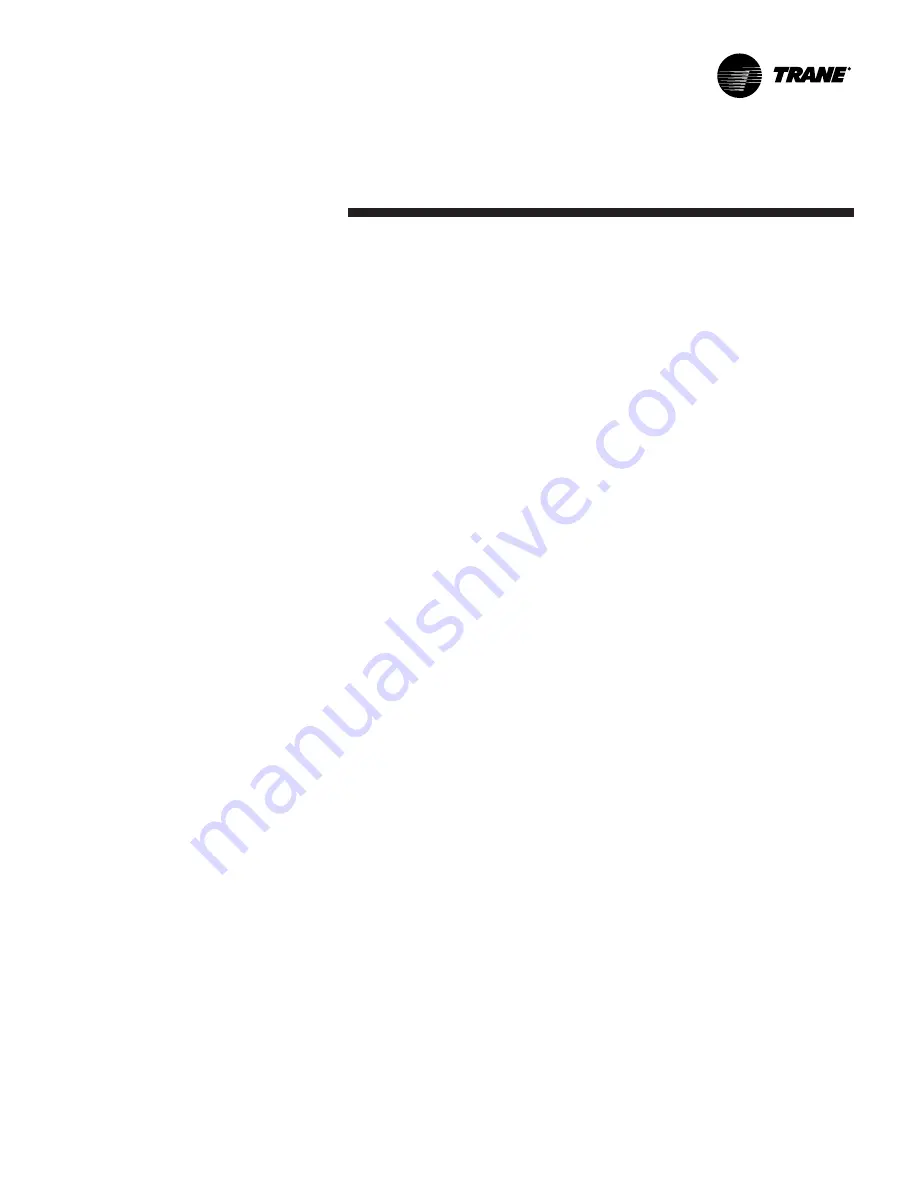
67
CDHF-SVU01C-EN
Electrical Sequence
This section will acquaint the
operator with the control logic
governing CDHF/CDHG chillers
equipped with Tracer CH530 UCP
based control systems. When
reviewing the step-by-step electrical
sequences of operation, refer to the
typical wiring schematics for Unit
mounted Wye Delta starter shown in
the installation manual shipped with
the chiller.
Note:
The typical wiring diagrams
are representative of standard units
and are provided only for general
reference. They may not reflect the
actual wiring of your unit. For
specific electrical schematic and
connection information, always refer
to the wiring diagrams that shipped
with the chiller.
With the supply power disconnect
switch or circuit breaker (2Q1 or 2K3)
closed, 115-volt control power
transformer 2T5 and a 40-amp starter
panel fuse (2F4 ) to terminal (2X1-1)
starter panel to terminal 1X1-1 in the
control panel. From this point,
control voltage flows to:
1. Circuit Breaker 1Q1 which
provides power to the starter
module (2A1) relay outputs and the
High Pressure Cutout switch (3S1).
2. Circuit Breaker 1Q2 which
provides power to the Purge
circuitry.
3. Circuit Breaker 1Q3 which
provides power to Transformer
(1T1) which steps down the 115
Vac to 24 Vac. This 24 Vac then
powers the 24 Vdc power supply
1A1, and 1A2 if present. The 24 vdc
is then connected to all modules
via the Interprocessor
communications Bus providing
module power.
1Q3 also provides power to the
external chiller water proof of flow
device connected between terminal
block 1X1-5 to 1A6-J3-2, and
condenser water proof of flow
device connected at 1X1-6 to 1A6-
J2-2.
4. Circuit Breaker 1Q4 which
provides power to the Oil Heater
4HR1 circuit and to circuit breaker
1Q5 oil and refrigerant pump
circuits.
5. The DynaView
™
display module
1A22, receives 24 vdc power from
the IPC bus.
UCP and Wye-Delta Starter
Control Circuits
Logic Circuits within the various
modules will determine the starting,
running, and stopping operation of
the chiller. When operation of the
chiller is required the chiller mode is
set at ‘‘Auto’’. Using customer
supplied power, the chilled water
pump relay (5K1) is energized by the
1A5 Module output at 1A5-J2-4, and
chilled water flow must be verified
within 4 minutes 15 seconds by the
1A6 Module. The main processors
logic decides to start the chiller
based on the differential to start
setpoint. With the differential to start
criteria met module 1A5 then
energizes condenser water pump
relay (5K2) via customer supplied
power at 1A5 J2-1.
Based on the restart inhibit function
and the differential to start setpoint,
oil and refrigerant pump (4M3) will
be energized by 1A7 Module (1A7-J1).
The oil pressure must be at least 9
Psid for 30 continuous seconds and
condenser water flow verified within
4 minutes 15 seconds minutes for the
compressor start sequence to be
initiated.
Control Sequence
of Operation
Summary of Contents for CenTraVac Duplex CDHE
Page 23: ...23 CDHF SVU01C EN General Information Figure 16 Oil refrigerant pump circuit 1 or 2 ...
Page 52: ...CDHF SVU01C EN 52 Control System Components Figure 24 Control panel components layout ...
Page 53: ...53 CDHF SVU01C EN Control System Components ...
Page 65: ...65 CDHF SVU01C EN Control System Components ...
Page 66: ...CDHF SVU01C EN 66 Control System Components ...
Page 104: ...CDHF SVU01C EN 104 ...
Page 105: ...105 CDHF SVU01C EN ...
Page 106: ...CDHF SVU01C EN 106 ...
Page 107: ...107 CDHF SVU01C EN ...
Page 108: ...CDHF SVU01C EN 108 ...
Page 109: ...109 CDHF SVU01C EN ...
Page 110: ...CDHF SVU01C EN 110 ...
Page 111: ...111 CDHF SVU01C EN ...
Page 112: ...CDHF SVU01C EN 112 ...
Page 113: ...113 CDHF SVU01C EN ...
Page 114: ...CDHF SVU01C EN 114 ...
Page 115: ...115 CDHF SVU01C EN ...