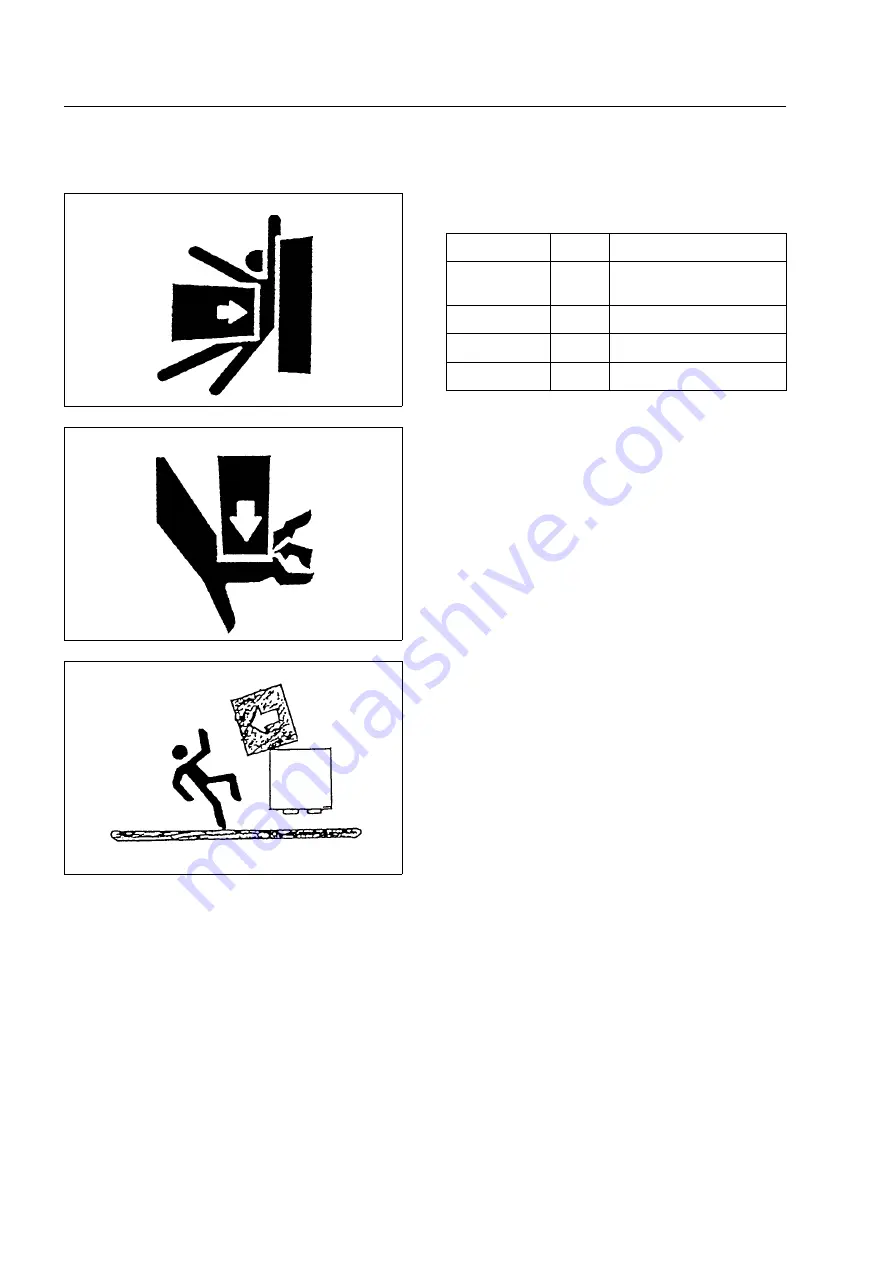
S. SAFETY
10
[ 2.2 ]
Transport
(1) Before bringing in machinery, always prepare
well-maintained carriers.
(2) Never lift the machine or load any higher than
200 mm above the floor during transport.
(3) Never stand in small spaces between the
machine/load and the wall during transporta-
tion.
(4) Always assign a guide and transport according
to his or her instructions.
The guide should pay sufficient attention to
any protruding parts on the transport route.
(5) Whenever inserting wooden blocks under the
machine/load, never let fingers get between
the machine/load and floor.
(6) Always push hand carts when carrying loads.
Never pull them.
(7) Fix the load with a rope or other means if nec-
essary, to prevent the load from falling down
during transport.
(8) When putting a lift beneath the machine, make
sure that its hook catches the place between
the back and front cross rails and balances it
right and left securely.
Carriers
Q'ty
Specifications
Forklift
(or wrecker)
1
3.5 t
(Reed space:150-190 cm)
Hand lift
2
3.0 t or more
Small jack
2
1.5 t or more
Wooden block
4
Approx. 90
×
150
×
60 mm