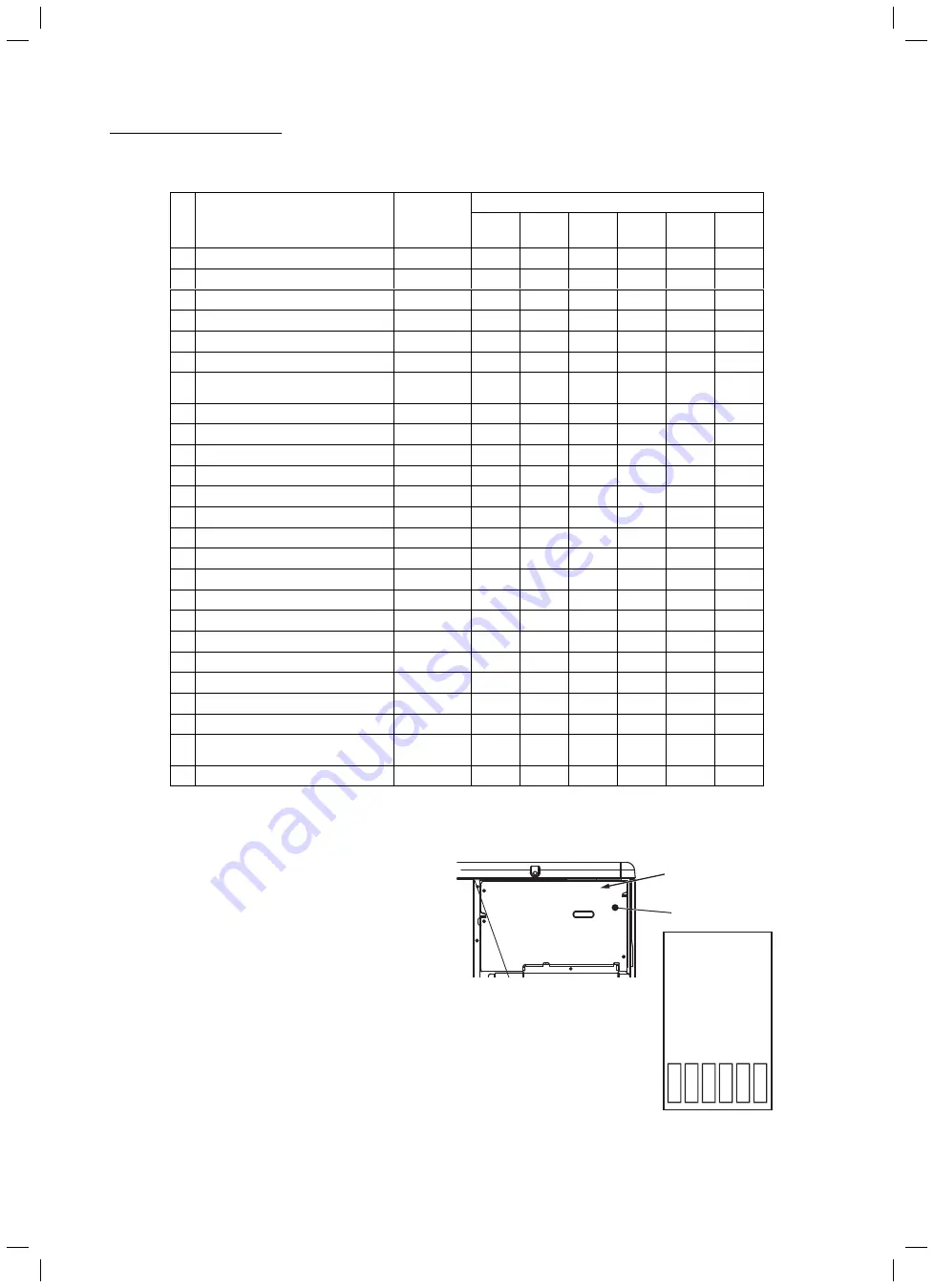
Contents Error Display
*
When fixations of the errors were overlapped, the latest error is displayed.
NO
ltem
Check code
[Wired remote
controller]
LED display
D800
(Yellow)
D801
(Yellow)
D802
(Yellow)
D803
(Yellow)
D804
(Yellow)
D805
(Green)
1
Discharge temp. sensor (TD) error
F04
۔
ە
ە
ە
ە
ۑ
2
Heat exchanger temp. sensor (TE) error
F06
ە
۔
ە
ە
ە
ۑ
4
Outside air temp. sensor (TO) error
F08
ە
ە
۔
ە
ە
ۑ
5
Suction temp. sensor (TS) error
F12
۔
ە
۔
ە
ە
ۑ
6
Heat sink temp. sensor (TH) error
F13
ە
۔
۔
ە
ە
ۑ
7
Miss-mounting of outdoor temp. sensor
(TE, TS)
F15
۔
۔
۔
ە
ە
ۑ
8
EEPROM error
F31
ە
۔
ە
۔
ە
ۑ
9
Compressor break down
H01
۔
۔
ە
۔
ە
ۑ
1
0
Compressor lock
H02
ە
ە
۔
۔
ە
ۑ
1
1
Current detection circuit error
H03
۔
ە
۔
۔
ە
ۑ
1
2
Case thermostat operation
H04
ە
۔
۔
۔
ە
ۑ
1
3
Unset model type of P.C.board
L10
ە
ە
ە
ە
۔
ۑ
1
4
Communication error between MCUs
L29
۔
ە
ە
ە
۔
ۑ
1
5
Discharge temp. error
P03
ە
۔
ە
ە
۔
ۑ
1
6
High pressure SW system error
P04
۔
۔
ە
ە
۔
ۑ
1
7
Power supply voltage error
P05
ە
۔
ە
۔
ۑ
1
8
Heat sink overheat error
P07
ە
۔
۔
ە
۔
ۑ
19
Gas leak detection
P15
۔
۔
۔
ە
۔
ۑ
20
High pressure protective operation
P20
۔
ە
ە
۔
۔
ۑ
21
Fan system error
P22
ە
۔
ە
۔
۔
ۑ
22
Short-circuit of compressor drive element
P25
۔
۔
ە
۔
۔
ۑ
23
Position detection circuit error
P29
ە
ە
۔
۔
۔
ۑ
2
4
Compressor IPDU or other (not specially
identified)
–
۔
ە
۔
۔
۔
ۑ
2
5
Power supply error
–
ە
ە
ە
ە
ە
ە
ۑ
: ON
ە
: OFF
۔
: Rapid flash (5 times /sec.)
D800
D801
D802
D803
D804
D805
(Yellow)
(Yellow)
(Yellow)
(Yellow)
(Yellow)
(Gr
een)
Inspection window
through which to check
the LED displays
Electric parts cover
*
The LEDs are located at the top right of the P.C.
board of the outdoor unit as shown in the figure
on the right.
ە
3
Heat exchanger temp. sensor (TL) error
F0
7
۔
۔
ە
ە
ە
ۑ
- 48 -
FILE NO. SVM-17005