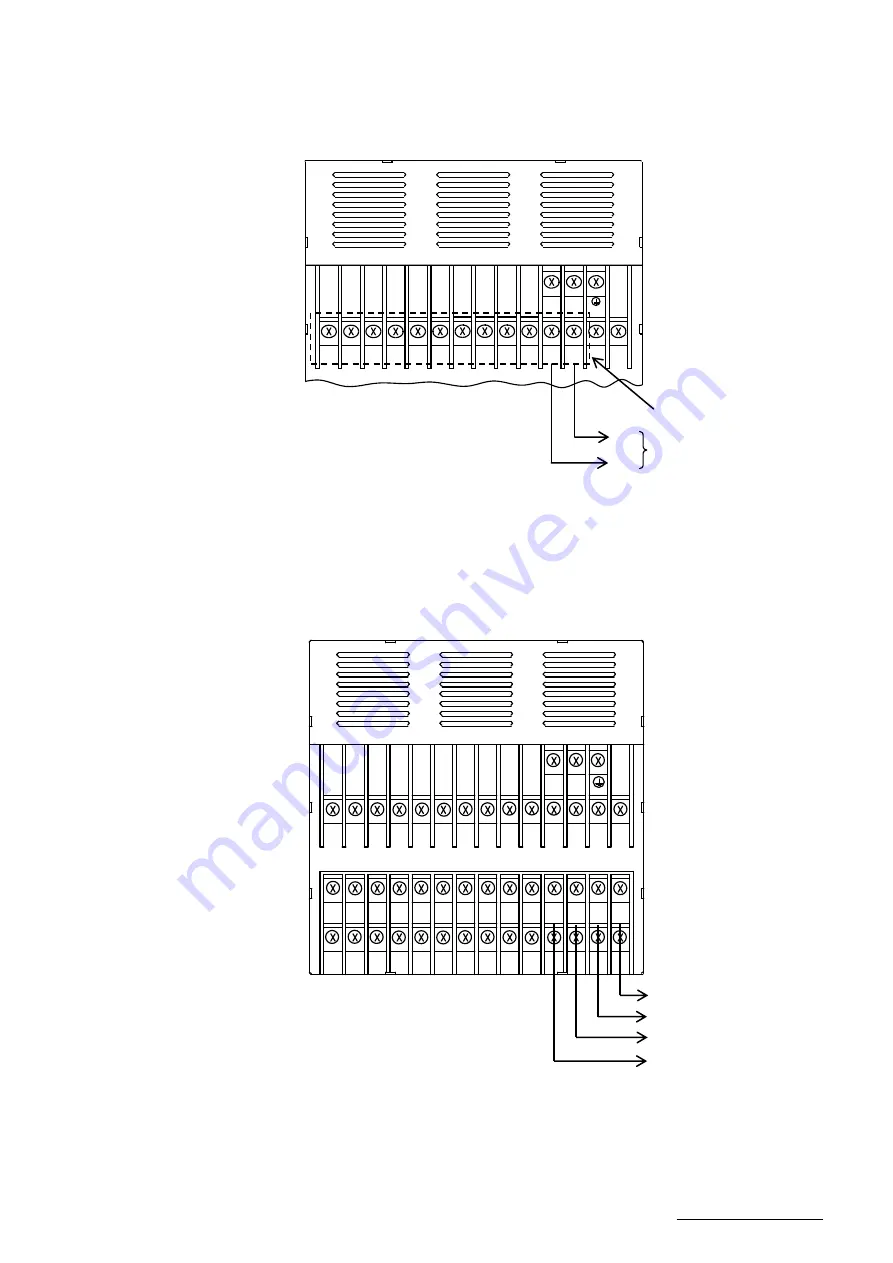
―
23
―
HXPRM10mnCT002E
4.3.2 Alarm Output Wiring Procedure
Wire the Alarm output refer to Fig.4.8.
Fig. 4.8
Alarm Output Wiring
4.3.3 DI Wiring Procedure
Wire the DI refer to Fig.4.9.
Fig. 4.9
DI Wiring
L
N
1A
1C
2A
2C
3A
3C
+
-
3-Relay output
3C
3A
Relay No.3
(Normally open)
L
N
1C
1A
2A
3C
3A
2C
1+
B
1-
B
1
A
2+
B
2-
B
2
A
SG
RD
TD
DI
COM
DI
3
DI
2
DI
1
+
-
DI1
DI2
DI3
DI.COM
(COMMON for DI1 to DI3)