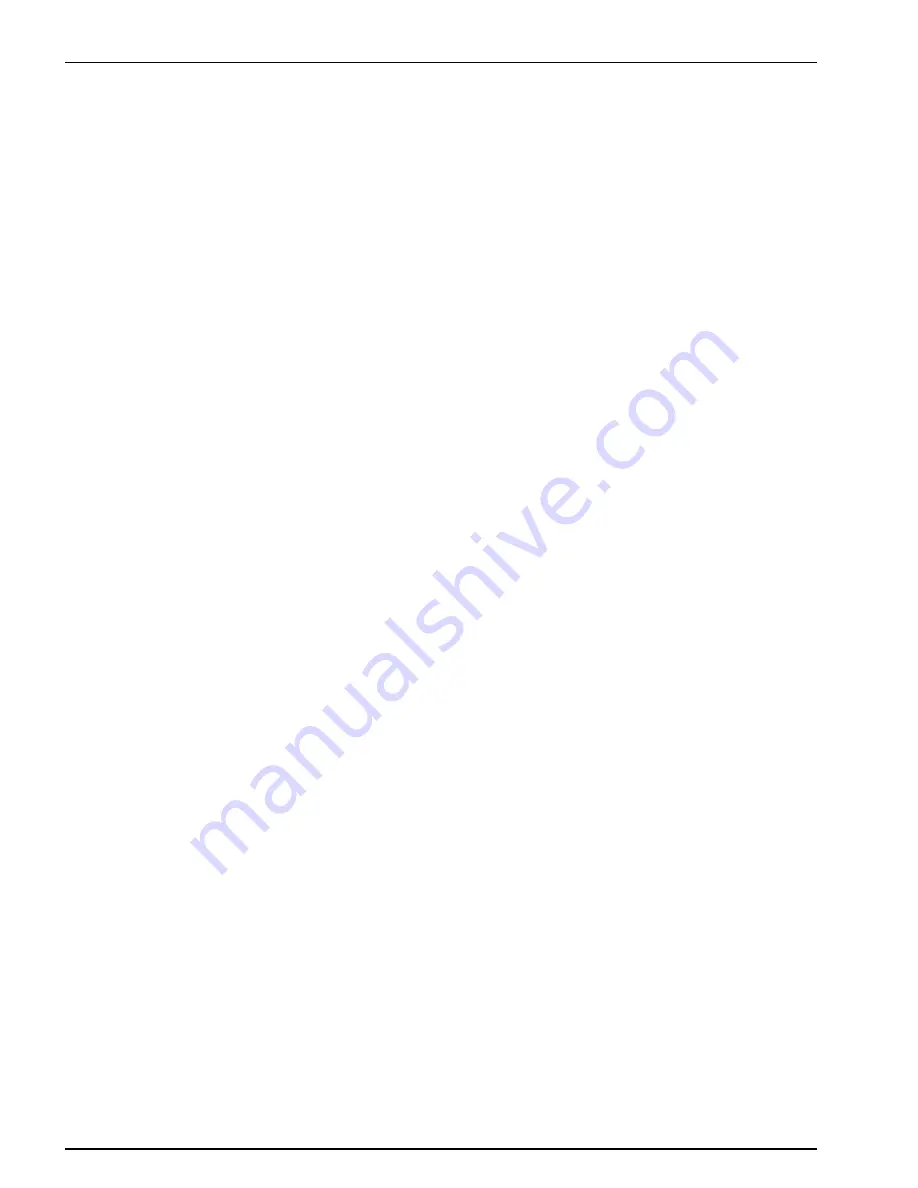
Refrigeration Maintenance (Rev. 04/03)
104
3.
Prepare to perform service on the low side by equaliz-
ing the high side and low side pressures through the
gauge manifold. Equalize low side pressure to 1 to
2 psig (7 to 14 kPa).
NOTE: Repeat the pump down procedure if the pres-
sures equalize above 20 psig (138 kPa). If acceptably
low pressures cannot be achieved after the third pump
down, the refrigerant must be recovered to perform
service in the low side.
4.
If the reading on the gauge manifold’s high pressure
gauge increases after the high and low side pressures
have been equalized, the condenser inlet check valve
(or hot gas solenoid) is leaking.
THREE-WAY VALVE CONDENSER
PRESSURE BYPASS CHECK VALVE
The condenser pressure bypass check valve is built into the
three-way valve. This check valve controls the bypass flow
of refrigerant gas between the condenser inlet line and com-
pressor discharge line.
The check valve is closed when the unit is running on cool,
or whenever the discharge pressure is higher than the con-
denser pressure.
When the unit is running on defrost or heat, if the condenser
pressure is higher than the discharge pressure, the check
valve opens and the condenser pressure is bled off until it
drops to the level of the discharge pressure. The purpose of
the valve is to improve heating/defrosting ability and three-
way valve response.
To check the operation of the valve:
1.
Remove the condenser pressure bypass check valve cap
from the three-way valve.
2.
Using a screwdriver, gently turn the check valve stem
in until the valve is front seated.
3.
Install a service gauge manifold set on compressor.
4.
Close (front seat) the receiver tank outlet valve.
5.
Operate the unit on cooling, and pump down the low
side to 20 in. (-68 kPa) of vacuum.
6.
Stop the unit. The condenser and suction pressures
should remain stable, indicating no leaks.
7.
Shift the three-way valve to heat position. Low side
gauge will raise slightly. High side gauge will drop to
approximately zero. Gauges will equalize.
8.
Gauges will remain in this position (approximately
zero) if the three-way valve seals properly toward the
condenser and the condenser pressure bypass check
valve seals properly.
9.
Back seat condenser pressure bypass check valve stem
against snap ring. Both gauges should rise indicating
the condenser pressure bypass check valve is properly
releasing condenser pressure into the discharge tube
and evaporator.
10. Replace the cap on the condenser pressure bypass
check valve.
NOTE: Valve stem MUST be back seated during nor-
mal unit operation.
11. Open the receiver tank return outlet valve, remove the
gauges and return the unit to normal operation.
Summary of Contents for KD-II SR
Page 4: ......
Page 8: ......
Page 13: ...Safety Precautions Rev 04 03 v AEA40...
Page 14: ...Safety Precautions Rev 04 03 vi AEA38...
Page 33: ...Unit Description Rev 04 03 19 1 Evaporator 2 Access Door Rear View Curbside KD II SR 1 2 AEA38...
Page 37: ...Unit Description Rev 04 03 23 Power Receptacle Box KD II SR 50 AEA42...
Page 58: ...Remote Control Panel Features Rev 04 03 44...
Page 112: ...Refrigeration Maintenance Rev 04 03 98...
Page 120: ...106...
Page 146: ...132...
Page 156: ...142...
Page 162: ...148...
Page 170: ...156...
Page 172: ...158...
Page 173: ...159 KD II 30 Schematic Diagram Page 1 of 2...
Page 174: ...160 KD II 30 Schematic Diagram Page 2 of 2...
Page 175: ...161 KD II 30 Wiring Diagram Page 1 of 2...
Page 176: ...162 KD II 30 Wiring Diagram Page 2 of 2...
Page 177: ...163 KD II 50 Schematic Diagram Page 1 of 2...
Page 178: ...164 KD II 50 Schematic Diagram Page 2 of 2...
Page 179: ...165 KD II 50 Wiring Diagram Page 1 of 2...
Page 180: ...166 KD II 50 Wiring Diagram Page 2 of 2...
Page 181: ...167 KD II 50 SR 230 1 60 Wiring Diagram Page 1 of 2...
Page 182: ...168 KD II 50 SR 230 1 60 Wiring Diagram Page 2 of 2...