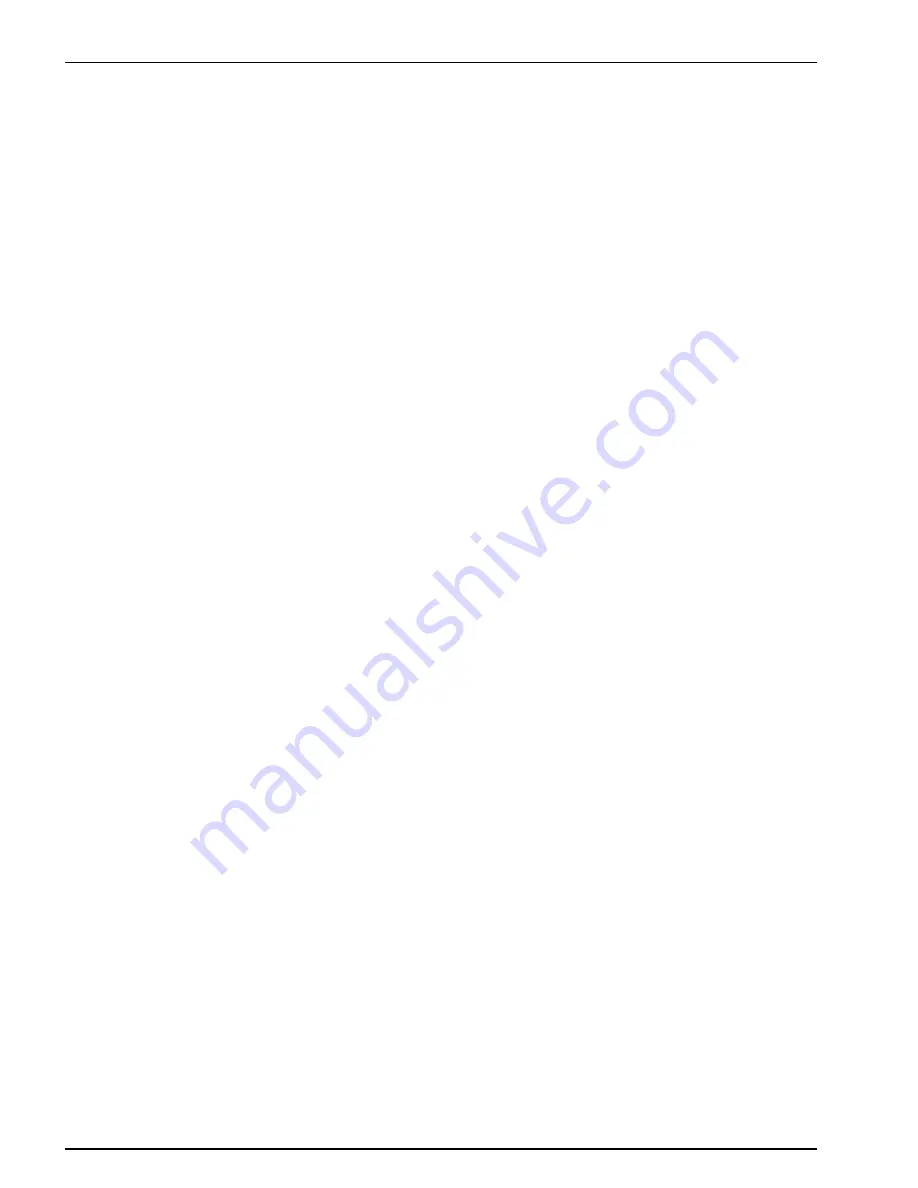
Electrical Maintenance (Rev. 04/03)
64
HIGH CAPACITY THERMAX
™
HEATING
SYSTEM
The High Capacity TherMax
™
Heating System
The high capacity heating system increases the capacity of
the heat mode by making more refrigerant available for use
in the heat mode. This is accomplished by adding an addi-
tional solenoid (TherMax™ solenoid) to the refrigeration
system which opens during the beginning of the heat mode
to move the liquid refrigerant from the condenser to the
accumulator where it can be used in the heat mode. The
sequence of operation for the improved heating system is
from the cool mode to the heat with refrigerant transfer
mode to the heat mode. The heat mode to cool mode opera-
tion is the same as in the past. The bypass check valve, and
the condenser check valve have been eliminated from the
TherMax™ heating system.
The components that have been added to the system are: the
TherMax™ solenoid, the TherMax™ solenoid line, and the
receiver outlet check valve. The TherMax™ solenoid con-
trols the flow of refrigerant through the TherMax™ sole-
noid line. The TherMax™ solenoid line goes from the
liquid line just past the receiver outlet check valve to the
accumulator inlet. The receiver outlet check valve is located
in the liquid line near the drier/receiver outlet. This check
valve prevents refrigerant from migrating back into the
receiver tank and condenser during the heat mode.
Cool Mode
The cool mode has not been changed in the TherMax™
heating system. The TherMax™ solenoid, which is nor-
mally closed, is de-energized during the cool mode. The
TherMax™ solenoid separates the high side from the low
side. When the TherMax™ solenoid is closed, it does not
allow liquid refrigerant to flow from the liquid line, through
the TherMax™ solenoid line, to the accumulator.
Heat/Condenser Evacuation Mode
When the µP-T controller initiates a heat or defrost cycle,
both the TherMax™ solenoid and the pilot solenoid ener-
gize simultaneously. The 26P wire from the interface circuit
board supplies a ground to the pilot solenoid and the 26T
wire supplies a ground to the TherMax™ solenoid. The
pressure difference between the high pressure liquid in the
condenser and the low pressure accumulator drives much of
the refrigerant out of the condenser and receiver, and back
into the accumulator. It is then available for improved heat-
ing capacity. The three-way valve and the receiver outlet
check valve prevent the migration of refrigerant back into
the receiver tank and condenser. The TherMax™ solenoid
will remain energized until there develops a +4 degree F
(0.2 C) temperature difference between the discharge air
and return air sensors (discharge air temperature - return air
temperature = +4 degrees F). After this, the heat cycle will
continue with just the pilot solenoid energized. The heat
with refrigerant transfer mode will perform this way in
every SR unit, regardless of ambient temperature or refrig-
erant type.
Additional Notes
In the event that either the discharge air temperature sensor
or return air temperature sensor fails, as determined by the
µP-T controller, the heat with refrigerant transfer mode will
be controlled by the coil sensor instead. The coil
temperature will be recorded at the start of the defrost or
heat cycle, and the TherMax™ solenoid will stay energized
until the coil sensor temperature increases by 4 degrees F
(0.2 C).
(Every time the SR unit starts up on diesel engine or electric
motor, the unit is placed in the heat mode for about 20
seconds. During this time, the TherMax™ solenoid is not
energized.)
Summary of Contents for KD-II SR
Page 4: ......
Page 8: ......
Page 13: ...Safety Precautions Rev 04 03 v AEA40...
Page 14: ...Safety Precautions Rev 04 03 vi AEA38...
Page 33: ...Unit Description Rev 04 03 19 1 Evaporator 2 Access Door Rear View Curbside KD II SR 1 2 AEA38...
Page 37: ...Unit Description Rev 04 03 23 Power Receptacle Box KD II SR 50 AEA42...
Page 58: ...Remote Control Panel Features Rev 04 03 44...
Page 112: ...Refrigeration Maintenance Rev 04 03 98...
Page 120: ...106...
Page 146: ...132...
Page 156: ...142...
Page 162: ...148...
Page 170: ...156...
Page 172: ...158...
Page 173: ...159 KD II 30 Schematic Diagram Page 1 of 2...
Page 174: ...160 KD II 30 Schematic Diagram Page 2 of 2...
Page 175: ...161 KD II 30 Wiring Diagram Page 1 of 2...
Page 176: ...162 KD II 30 Wiring Diagram Page 2 of 2...
Page 177: ...163 KD II 50 Schematic Diagram Page 1 of 2...
Page 178: ...164 KD II 50 Schematic Diagram Page 2 of 2...
Page 179: ...165 KD II 50 Wiring Diagram Page 1 of 2...
Page 180: ...166 KD II 50 Wiring Diagram Page 2 of 2...
Page 181: ...167 KD II 50 SR 230 1 60 Wiring Diagram Page 1 of 2...
Page 182: ...168 KD II 50 SR 230 1 60 Wiring Diagram Page 2 of 2...