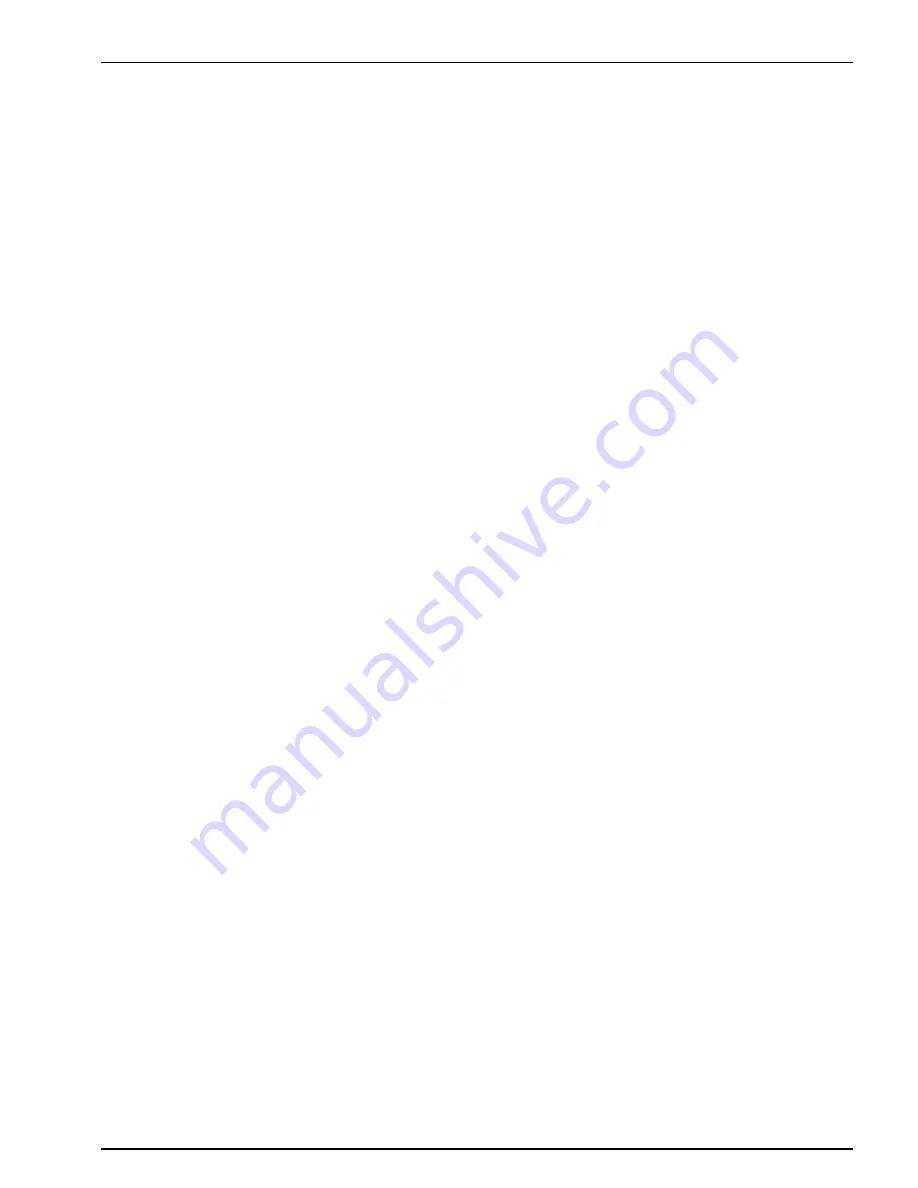
Engine Maintenance (Rev. 04/03)
71
The injection pump plungers are activated by an extension
on the engine camshaft. The governor sleeve and weight
assembly is mounted on the end of the crankshaft with
governor’s speed requirements being relayed to the
injection pump through a linkage arrangement located in the
front timing cover. The injection pump raises the pressure of
the fuel and meters the correct amount of fuel to the nozzle
at the correct time. The increased fuel pressure will lift the
spring loaded nozzle to admit fuel into the combustion
chamber.
The fuel system is relatively trouble free, and if properly
maintained will usually not require major service repairs
between engine overhauls.
The most common cause of fuel system problems is con-
tamination. It cannot be stressed enough that the fuel must
be clean, fuel tanks must be free from contaminants, and the
fuel filter must be changed regularly. Any time that the fuel
system is opened up, all possible precautions must be taken
to keep dirt from entering the system. This means all fuel
lines should be capped when open. The work should be
done in a relatively clean area, if possible, and the work
should be completed in the shortest time possible.
Thermo King recommends that any major injection pump or
nozzle repairs be done by a quality diesel injection service
specialty shop. The investment in equipment and facilities
to service these components is quite high. Therefore, this
equipment is not found in most repair shops.
The following procedures can be done under field condi-
tions:
1.
Bleeding air from the fuel system.
2.
Maintenance involving the fuel tank and filter system.
3.
Speed and governor adjustments.
4.
Electric transfer pump replacement or repair (10 psig
[69 kPa] pump with diesel filter).
5.
Injection line replacement.
6.
Pump timing.
7.
Nozzle spray pattern testing and adjustment.
8.
Minor rebuilding of nozzles.
Bleeding the Fuel System
The fuel system will have to have the air bled out if the
engine runs out of fuel, if repairs are made to the fuel sys-
tem, or air gets into the system for any other reason.
NOTE: MAKE SURE to keep the fuel tank vent open. If
the vent becomes clogged, a partial vacuum develops in
the tank, and this increases the tendency for air to enter
the system.
Proceed as follows:
1.
Loosen the bleeder screw on the inlet fuel fitting of the
injection pump.
2.
Turn on the electric fuel pump. The electric fuel pump
is energized when the ON button is pushed. Tighten the
bleeder screw on the injection pump when clear flow of
fuel appears. Use the relay board test—see TK 41087.
NOTE: At initial start-up, open the bleeder screw at
the injection pump and bleed fuel until a clear flow is
noted.
3.
Loosen the injector lines on the injection nozzles.
4.
Crank the engine until fuel appears at the nozzles.
Tighten the injector lines, and start the engine.
NOTE: Fuel will not appear at the nozzles by merely
running the electric pump. The engine must be
cranked.
Summary of Contents for KD-II SR
Page 4: ......
Page 8: ......
Page 13: ...Safety Precautions Rev 04 03 v AEA40...
Page 14: ...Safety Precautions Rev 04 03 vi AEA38...
Page 33: ...Unit Description Rev 04 03 19 1 Evaporator 2 Access Door Rear View Curbside KD II SR 1 2 AEA38...
Page 37: ...Unit Description Rev 04 03 23 Power Receptacle Box KD II SR 50 AEA42...
Page 58: ...Remote Control Panel Features Rev 04 03 44...
Page 112: ...Refrigeration Maintenance Rev 04 03 98...
Page 120: ...106...
Page 146: ...132...
Page 156: ...142...
Page 162: ...148...
Page 170: ...156...
Page 172: ...158...
Page 173: ...159 KD II 30 Schematic Diagram Page 1 of 2...
Page 174: ...160 KD II 30 Schematic Diagram Page 2 of 2...
Page 175: ...161 KD II 30 Wiring Diagram Page 1 of 2...
Page 176: ...162 KD II 30 Wiring Diagram Page 2 of 2...
Page 177: ...163 KD II 50 Schematic Diagram Page 1 of 2...
Page 178: ...164 KD II 50 Schematic Diagram Page 2 of 2...
Page 179: ...165 KD II 50 Wiring Diagram Page 1 of 2...
Page 180: ...166 KD II 50 Wiring Diagram Page 2 of 2...
Page 181: ...167 KD II 50 SR 230 1 60 Wiring Diagram Page 1 of 2...
Page 182: ...168 KD II 50 SR 230 1 60 Wiring Diagram Page 2 of 2...