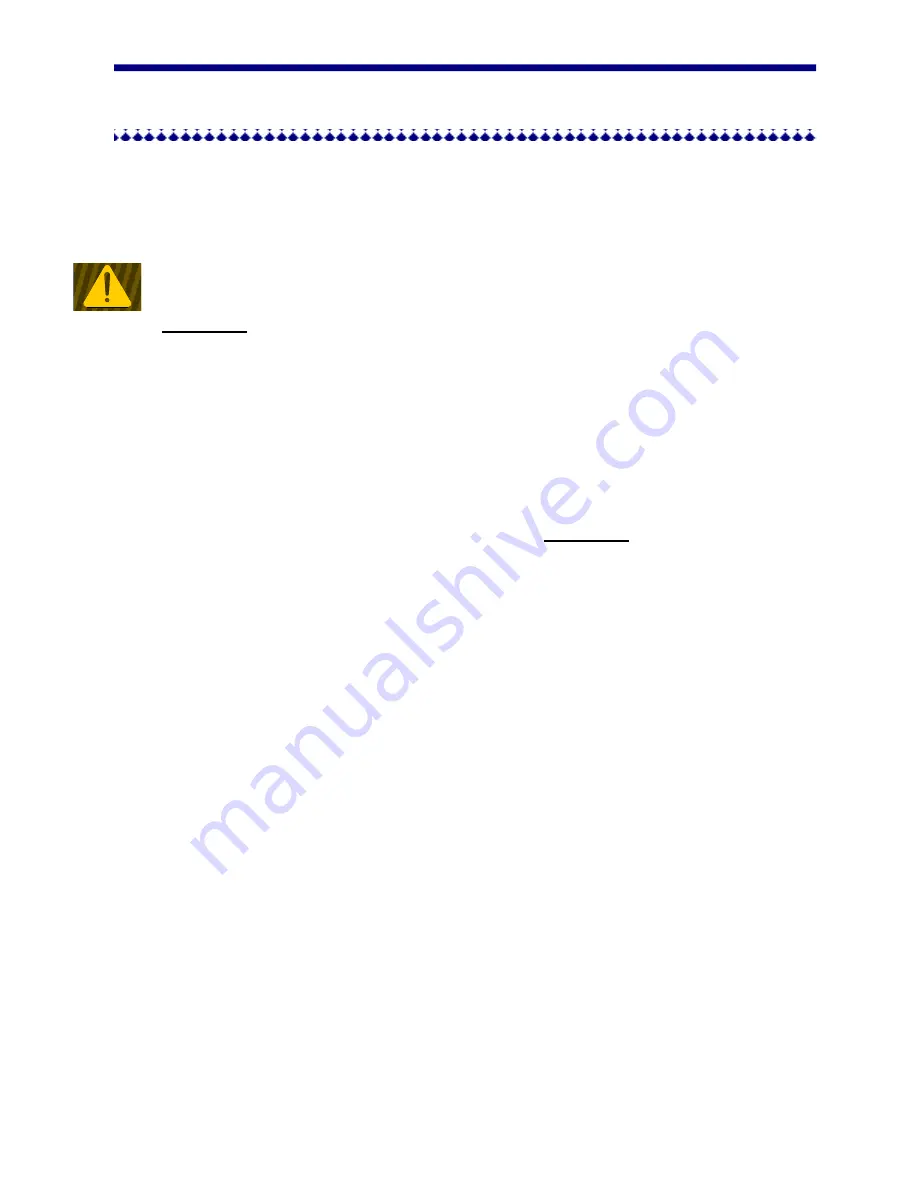
22
6.5 Maintenance Schedule
6.5.1 Constant Operational Checks
1.
AIR NOZZLES- At each shut down cycle, examine air nozzles and remove any buildup.
2.
AIR NOZZLE ADJUSTMENT- The side air jet nozzles may need adjustment
periodically. Remove the nozzle from the head and place into a vise. By hand bend the
nozzle tube to required fit. To get an even spray pattern the right and left tube should be
close
to
the
same
fit.
See
Section
6.2
for
alignment
requirements.
CAUTION:
do not bend the tube while it is in the head, the plastic head may break.
3.
SPRAY TEXTURE- If the spray becomes course or rough, check contact tip and air
nozzle alignment.
4.
SPRAY PATTERN- If the spray pattern changes, check tip and air nozzle alignment.
5.
ERRATIC WIRE FEED- Remove and clean contact tips and contact tubes. Lubricate
liners from feeder to head. With the wire removed, spray WD-40 into liner at feeder end,
then use an air hose to blow the lubricant through the liner to the head. Lubricate wire
delivery tube from dispenser unit. Placing a wiper that can be soaked with lubricant at the
dispenser will lubricate the wire and reduce friction in the delivery tube.
6.
SHIELD- Clean shield as needed during operations.
CAUTION
: MAY BE HOT!
7.
HEAD- Clean head as needed during operations. Metal dust can cause shorting between
the contact tubes.
6.5.2 Daily Maintenance (8 hours)
1.
SPRAY HEAD- Wipe off all dust particularly at the front between the contact tubes.
2.
CONTACT TIPS- Remove and clean dust and lint from behind the tip, this can bind the
wire and cause erratic feed.
3.
CONTACT TUBES- When the tips are removed, inspect the internal bore and remove
any debris.
4.
LINERS- Lubricate with WD-40, or use a non-petroleum based material. Spray WD-40
into liners at feeder end, and then use an air hose to blow the lubricant through the liners.
5.
FEED UNIT- Clean the inside of the wire feed unit. Blowing it down with air is usually
all that is required. Wire brush & remove any embedded material.
6.
FEED ROLL BEARINGS- Check each feed roll bearing (8 each) to make sure they are
loose and roll free. They are prelubricated bearings, however they can get gummed up
and stick. If required, remove the gear from the feeder and clean the shaft and inside of
bearing with a degreasing cleaner, then reinstall.
Summary of Contents for BRIDGEMASTER
Page 20: ...7 3 System Assembly drawing shows optional straighteners...
Page 30: ...17 6 2 1 Angle Spray Nozzle 3 16 4 8 mm Wire Head...
Page 31: ...18 6 3 Air Nozzle Alignment 1 8 3 2 mm Wire Head...
Page 32: ...19 6 3 2 Angle Spray Nozzle 1 8 3 2 mm Wire Head...
Page 57: ...44 9 4 1 System Wiring...