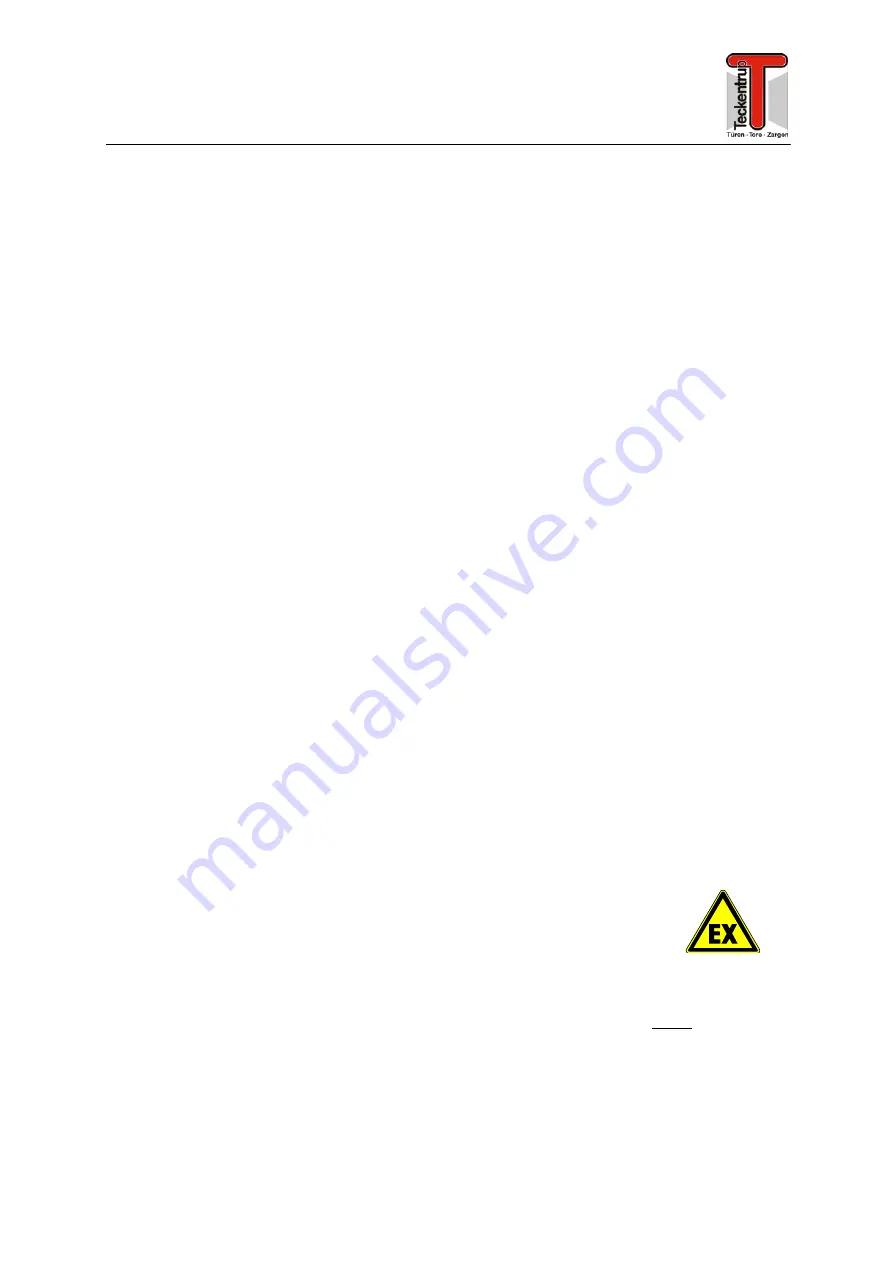
Planning, Installation, Maintenance and Operating Instructions
dw
62-2 ME Sliding Doors
- 3 -
1. General
Information
-
These installation instructions provide an overview of the current state of development.
-
The utmost care has been taken to ensure that these instructions are error free. However, we shall not be
liable for any possible printing errors or missing data.
-
We reserve the right to make technical changes.
-
In order to guarantee correct functioning and safe operation of the door only use original parts as
accessories, e.g. fittings, door latches, locks, locking mechanisms. Always observe the respective assembly
instructions. Spare parts and accessories can be purchased from an authorised distributor and Tekla-
Technik, Tor + Tür GmbH & Co. KG.
Important:
-
In the interest of safety, only use the anchors, plugs and bolts supplied with the door for installation. The
following plugs and anchors are used: For masonry Fischer FUR and for concrete Fischer FAZ or FH-S.
Fixings not specified in the installation instructions require prior release by Tekla-Technik, Tor + Tür GmbH &
Co. KG.
-
These instructions have been created for authorised technicians in accordance with EN 12635
requirements. Door assembly should only be carried out by technicians who fulfil these
requirements.
-
Welding at the suspension should only be carried out by qualified welders (DIN EN 287-1 (Qualification test
of welders - Fusion welding)).
1.1 Types of Walls
The static stability of the frame and runner rail installation has to be designed for the actual weight of
the door! Static inspection/documentation has to be provided by the customer!
The sliding door can be mounted to the following walls:
-
Masonry
in accordance with DIN 1053-1, min. masonry strength class 12, min. masonry mortar group IIa,
wall thickness
≥
240 mm
or
-
Concrete
in accordance with DIN 1045, min. strength class B15,
wall thickness
≥
140 mm
.
-
Autoclaved aerated concrete blocks and high precision units
– in accordance with DIN 4165, min.
masonry strength class 4
-
Steel constructions
with static documentation
2. Assembly
2.1 Preparation
-
Ensure that the wall is plumb and level prior to assembly.
-
Carry out plastering and painting work after assembling the door.
-
Precisely even out any unevenness, etc. on the wall using pressure-resistant bases.
-
Fix the sliding door to the adjacent constructional elements tightly enough to ensure that the static loads of
the closed and open door as well as the dynamic load of the opening and closing door are permanently
borne. These forces should not affect the stability of the adjacent wall.
-
Ensure that the door is covered before plastering or painting work is carried out, since spots of mortar,
cement, plaster or paint can damage the surface.
-
Make sure that the door does not come into contact with corrosive and caustic agents such as saltpetre
reactions from bricks or mortar, acids, alkalis, road salt, chlorine, corrosive paints or sealing compounds.
-
Always observe and adhere to local regulations if the door is installed in
explosive areas. The owner has to inform the company commissioned to install
the door of these regulations.
Earthing measures should only be carried out by qualified electricians
2.2 Maintenance/Inspections/Repairs
The owner or a person authorised by the owner has to visually inspect the functionality of the door system
regularly and to check for any external damages in accordance with chapter 1 of the maintenance information
(see 1, Check List Power Operated Doors - Systems). Repair work should only be carried out by qualified
technicians or Tekla-Technik, Tor + Tür GmbH & Co. KG. Immediately ensure that an unsafe door cannot be
operated until it has been repaired correctly by a qualified technician or the door manufacturer. Always
observe the corresponding regulations for the maintenance and inspection of power operated doors and
create an inspection book. Record all carried out inspections. (see Appendix for Inspection Book)
Only replace defective parts with original ones. Please contact Tekla-Technik, Tor + Tür GmbH & Co. KG for
more information.
2.3 Operation/Utilisation
-
The ready to use door has to comply
with
EN 12604 and EN 12453 requirements.
-
Never place objects within the movement range of the door.