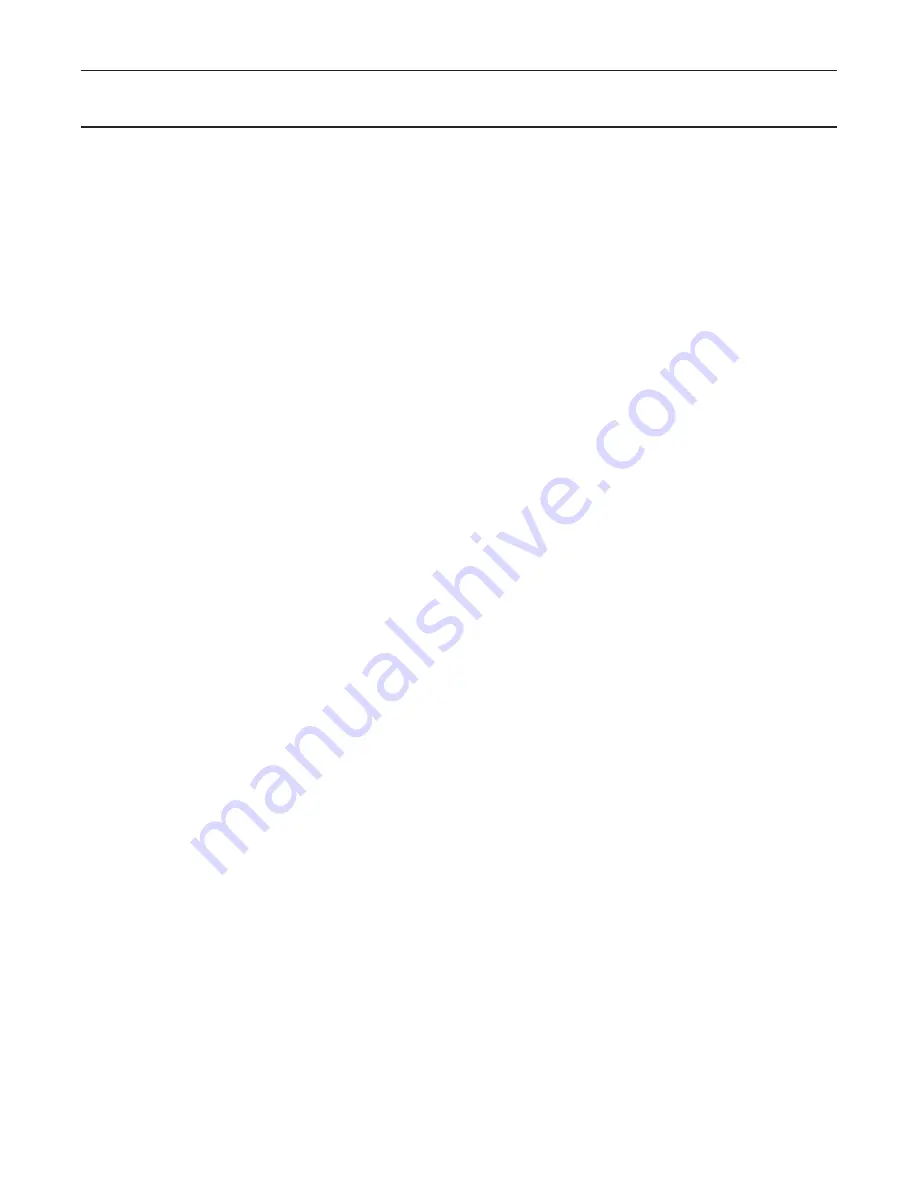
Issue/Rev. 0.1 (11/18) ║ MNKS025 • Page 99
MPU Series C I/O/M Manual
Fluid Correction Configuration
8 – Fluid Correction Configuration
This section addresses configuring the meter for fluid correction calculations; this
consists of selecting an algorithm and assigning inputs from various sources. The
correction results may be seen in the fluid correction run screen and accumulators
screen.
Input variables may typically be routed from sources listed below, but some inputs may
have limitations:
1. Fallback Value
a. A value programmed in the parameter database.
2. Analog Input, 4-20mA
a. Engineering units specified; engineering values for 4 and 20 mA (p1p2
configuration).
b. Units of measure may be converted. For example, pressure engineering units
may be set up for psi (gauge), and the units converted to that required by the
algorithm (bar absolute, for example).
c. Error selection – hold last or use fallback value. This behavior typically activates
when an analog input exceeds range.
3. Analog RTD Input
a. Error selection – hold last or use fallback value. This behavior typically activates
when an analog input exceeds range.
4. Modbus Input (also see the communications manual for modbus addresses and
number formats):
a. A floating point number written to the ultrasonic meter by an external host.
b. Error selection – hold last or use fallback value. This behavior typically activates
when the host does not write a value to the ultrasonic meter for a time. There
is a short timeout and a long one; the actual times may be different for different
input variables (see below, recommended update rates):
i. Short timeout
1. Hold last – an algorithm alarm is issued, but the calculations continue
using the last value written.
2. Fallback – an algorithm alarm is issued, but the calculations continue
using the programmed fallback value.
ii. Long timeout
1. An algorithm alarm is issued and calculations stop.
c. Units of measure may be converted, except for Mole Fractions, which are
percentage.
d. Recommended update rates from the host are below. Updating more frequently
risks overloading the meter CPU causing delayed responses in other Modbus
queries and user display, and updating less frequently risks the meter issuing
an alarm if more than one update in a row fails to write for some reason:
i. Temperature, Pressure, Live Density – recommended update rate is between
10 and 25 second intervals. The short timeout occurs at 60 seconds and
the long at 10 minutes.
ii. Reference Density, Gas composition – recommended update rate is
between 2 and 4 minute intervals. The short timeout occurs at 10 minutes,
and the long at 60 minutes. If new data is not available at 4 minute intervals,
the same values may be rewritten, thus preventing an alarm from being
issued.
Output variables vary widely depending on the algorithm selected. There may be
circumstances when the selected algorithm cannot compute outputs; if this should occur,
the algorithm outputs are set to “not a number” (typically displayed as “---”), as well as
any other variables that are derived from them, and an algorithm alarm is issued.
Summary of Contents for Smith Meter MPU 1600c
Page 10: ...Page 10 MNKS025 Issue Rev 0 1 11 18 Page intentionally left blank ...
Page 34: ...Page 34 MNKS025 Issue Rev 0 1 11 18 Page intentionally left blank ...
Page 38: ...Page 38 MNKS025 Issue Rev 0 1 11 18 Page intentionally left blank ...
Page 98: ...Page 98 MNKS025 Issue Rev 0 1 11 18 Page intentionally left blank ...
Page 106: ...Page 106 MNKS025 Issue Rev 0 1 11 18 Page intentionally left blank ...
Page 112: ...Page 112 MNKS025 Issue Rev 0 1 11 18 Page intentionally left blank ...
Page 119: ...Issue Rev 0 1 11 18 MNKS025 Page 119 Page intentionally left blank ...