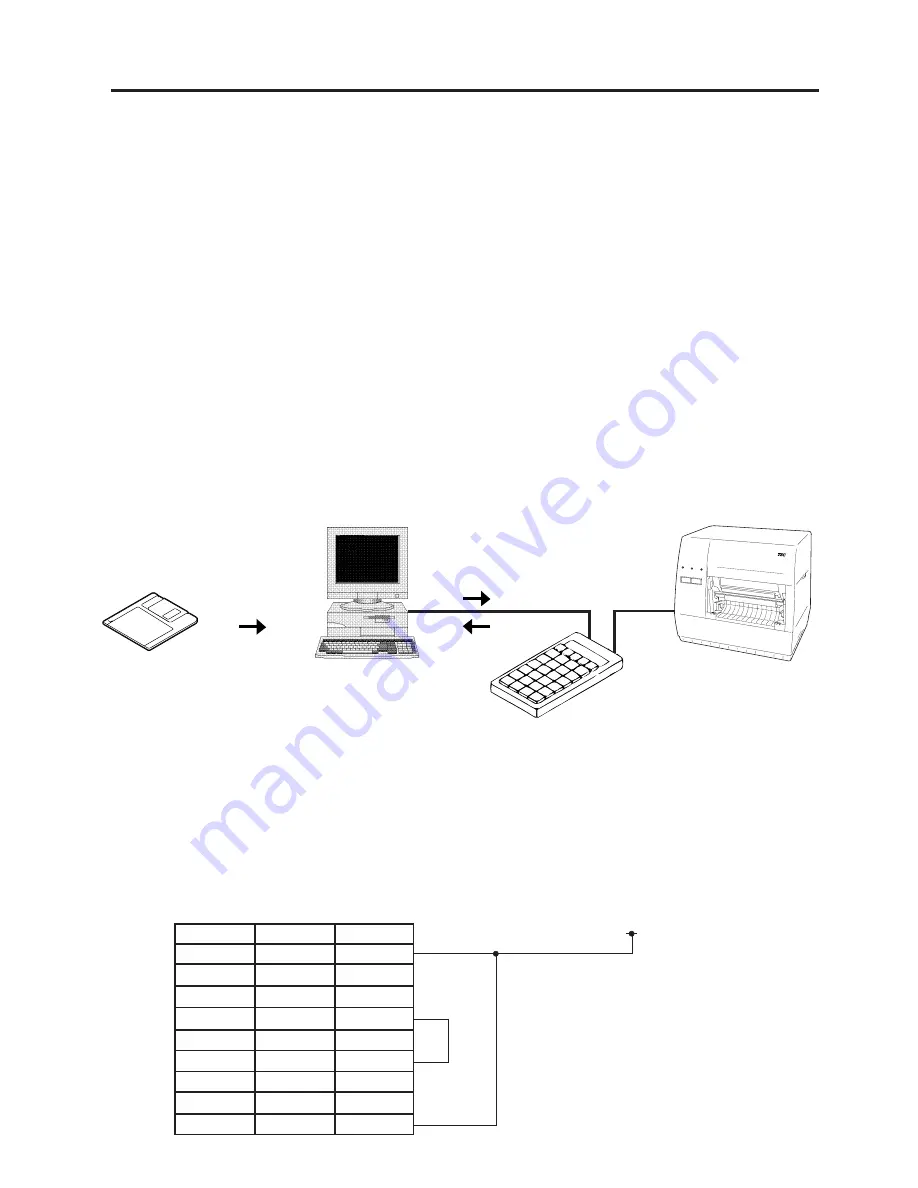
8-1
EO18-33003A
8. PROGRAM DOWN LOAD FOR KEYBOARD
8. PROGRAM DOWN LOAD FOR KEYBOARD
8.1 OUTLINE
The file loading loads (writes) BASIC program file or data file sent from the PC via an RS-232C cable to
the flash memory. This section describes how to use the file loading.
8.2 SETUP
1) The KB-80-QM enters the downloading mode in the maintenance mode.
2) The loading preparation command is sent from the PC via an RS-232C port (D-SUB).
3) The loading data is sent.
Communication conditions
Communication speed: 19200BPS
Data length:
8 bit
Parity:
EVEN
Stop bit:
1 bit
Flow control:
None
8.3 BLOCK DIAGRAM FOR FILE LOADING (CONNECTION)
8.1 OUTLINE
1) Turn off the printer and your PC.
2) Connect the DIN cable of the KB-80-QM to the DIN connector of the B-450 printer.
3) Connect KB-80-QM and your PC with the serial cable (D-SUB).
4) Turn on the printer and your PC.
NOTE: Pin configuration of KB-80-QM D-SUB connector:
To PC KB-80-QM D-SUB female (Locking screw: inch)
Fig. 8-1
Pin No.
1
2
3
4
5
6
7
8
9
Signal
---
TXD
RXD
---
GND
---
CTS
RTS
---
I/O
---
Output
Input
---
---
---
Input
Output
---
5V
Binary data
Command
Program
Binary data
Status