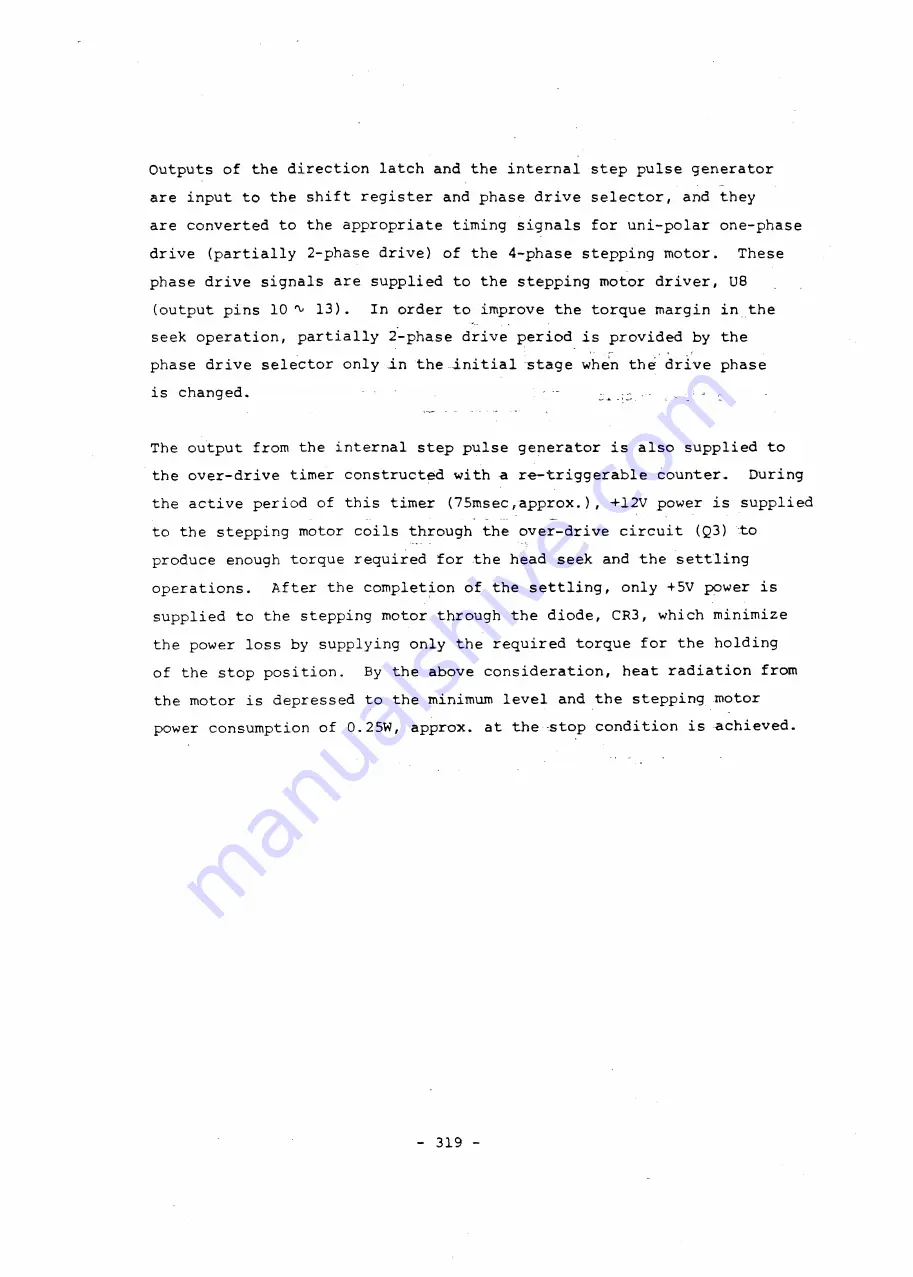
Outputs of the direction latch and the internal step pulse generator
are input to the shift register and phase drive selector, and they
are converted to the appropriate timing signals for uni-polar one-phase
drive (partially 2-phase drive) of the 4-phase stepping motor. These
phase drive signals are supplied to the stepping motor driver, U 8
(output pins 10 ^ 13).
In order to improve the torque margin in the
seek operation, partially 2-phase drive period is provided by the
phase drive selector only ±n the initial stage when the drive phase
is changed.
;
-
v
- c
The output from the internal step pulse generator is also supplied to
the over-drive timer constructed with a re-triggerable counter^
During
the active period of this timer (75msec,approx.), +12V power is supplied
to the stepping motor coils through the over-drive circuit (Q3) to
produce enough torque required for the head seek and the settling
operations.
After the completion of the settling, only +5V power is
supplied to the stepping motor through the diode, C R3, which minimize
the power loss by supplying only the required torque for the holding
of the stop position.
By the above consideration, heat radiation from
the motor is depressed to the minimum level and the stepping motor
power consumption of 0.25W, approx, at the stop condition is achieved.
319
Summary of Contents for FD-55 Series
Page 7: ...SECTION 3 THEORY OF OPERATION 300...
Page 8: ...3 1 CONSTRUCTION AND FUNCTION 3 1 1 General Block Diagram Fig 301 General block diagram 301...
Page 23: ...Fig 308 Control circuit block diagram 316...
Page 40: ...SECTION 4 MAINTENANCE 4000...
Page 56: ...J4 J12 Option J9 J5 Top view of the FDD Fig 401 Types of connectors 4016...
Page 95: ...Note Refer to item 4 2 1 as to handling of the set screw 4057...
Page 102: ...k Key in Cl SET TMAX L Confirm as in item j 4064...
Page 104: ...Notch B position TP6 voltage 0 5V Max LED indicator Fig 422 Check of file protect sensor 4066...
Page 125: ...k Eject the level disk and release the Invert and ADD modes of the oscilloscope 4087...
Page 136: ...Fig 431 Adjustment track alignment 4098...
Page 153: ...Fig 436 Adjustment of index sensor 4115...
Page 172: ...Fig 440 Replacement of head pad 4134...
Page 176: ...Plate Fig 441 CSS Ass y and shift lever position 4138...
Page 177: ...SECTION 5 DRAWINGS PARTS LIST 500...
Page 179: ...r Fig 501 External view No l 502...
Page 181: ...PCBA DD motor servo Fig 503 External view No 3...
Page 182: ...Fig 504 External view No 4 505...
Page 183: ...Partis nrnnber of the FDD Fig 505 Extemal view No 5 506...
Page 188: ...Fig 506 Mechanical section break down 511...
Page 199: ...PCBA DD MOTOR SERVO PARTS LOCATION Type S i 522A...
Page 200: ...PCBA DD TOR SERVO PARTS LOCATION Type TO 522B...
Page 201: ...PCBA DD MOTOR SERVO PARTS LOCATION Type G 522C...
Page 202: ...PCBA DD MOTOR SERVO PARTS LOCATION Type T 522D...
Page 204: ...523B PCBA DO MOTOR SERVO SCHEMATIC Type K...
Page 205: ...o 523C i 1 PACB DD HOTOR SERVO SCHEMATIC Type G...
Page 206: ...CV 5 3 3 H 2SV 523D PC DD M o t o r SERVO SCHEMATIC Type T...
Page 207: ...PCBA MFD CONTROL B PARTS LOCATION PCB ISSUE A G 524A...
Page 208: ......
Page 209: ...PCBA FRONT OPT PARTS LOCATION 525 PO I...
Page 210: ......
Page 211: ......
Page 212: ......
Page 213: ......
Page 214: ......
Page 215: ......
Page 216: ......