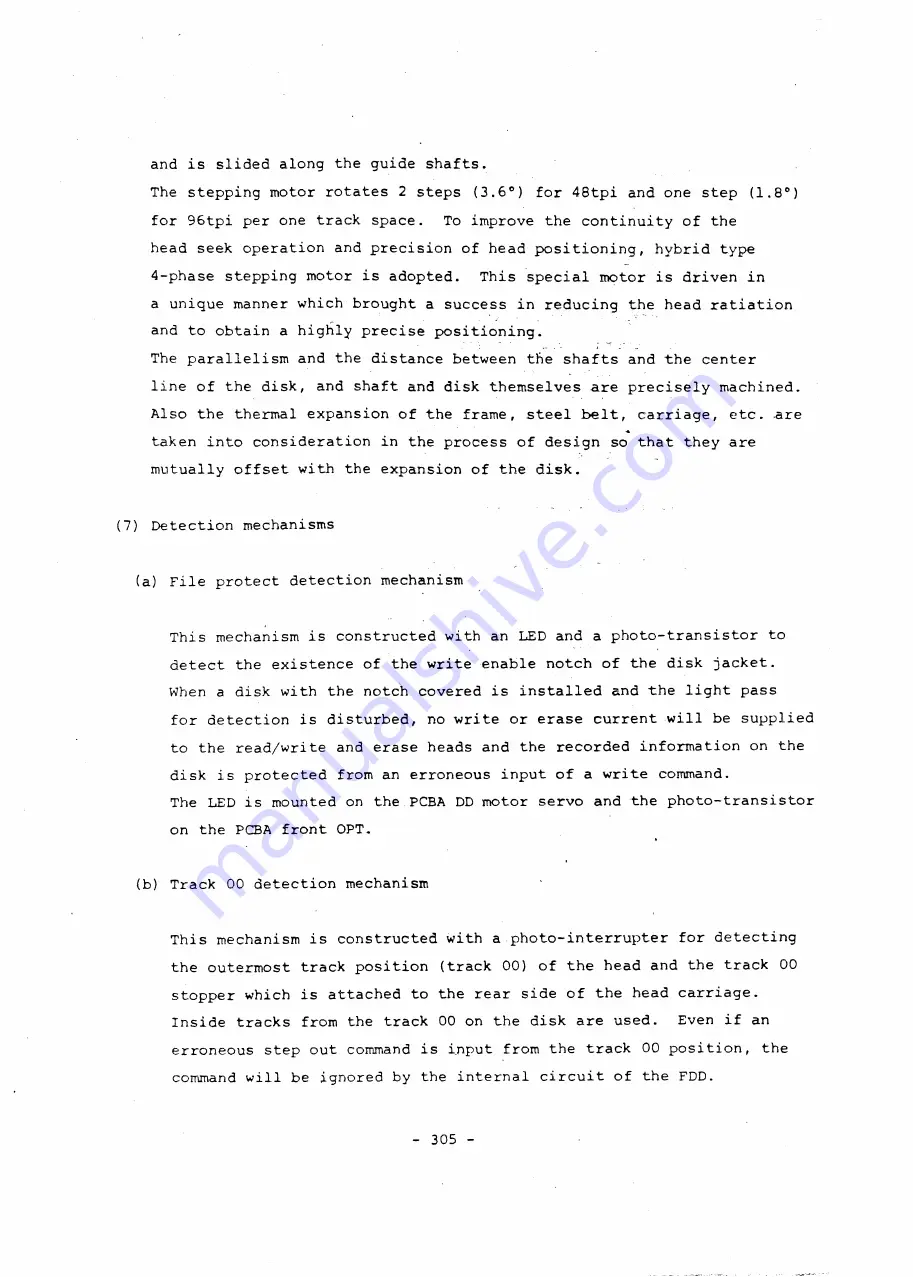
and is slided along the guide shafts.
The stepping motor rotates 2 steps (3.6°) for 48tpi and one step (1.8°)
for 96tpi per one track space.
To improve the continuity of the
head seek operation and precision of head positioning,
hybrid type
4-phase stepping motor is adopted.
This special motor is driven in
a unique manner which brought a success in reducing the head ratiation
and to obtain a highly precise positioning.
The parallelism and the distance between the shafts and the center
line of the disk,
and shaft and disk themselves are precisely machined.
Also the thermal expansion of the frame, steel b e l t ,
carriage,
etc. are
taken into consideration in the process of design so that they are
mutually offset with the expansion of the disk.
(7) Detection mechanisms
(a) File protect detection mechanism
This mechanism is constructed with an LED and a photo-transistor to
detect the existence of the write enable notch of the disk jacket.
When a disk with the notch covered is installed and the light pass
for detection is disturbed, no write or erase current will be supplied
to the read/write and erase heads and the recorded information on the
disk is protected from an erroneous input of a write command.
The LED is mounted on the PCBA DD motor servo and the photo-transistor
on the PCBA front OPT.
(b) Track 00 detection mechanism
This mechanism is constructed with a photo-interrupter for detecting
the outermost track position (track 00)
of the head and the track 00
stopper which is attached to the rear side of the head carriage.
Inside tracks from the track 00 on the disk are used.
Even if an
erroneous step out command is input from the track 00 position,
the
command will be ignored by the internal circuit of the FDD.
305
Summary of Contents for FD-55 Series
Page 7: ...SECTION 3 THEORY OF OPERATION 300...
Page 8: ...3 1 CONSTRUCTION AND FUNCTION 3 1 1 General Block Diagram Fig 301 General block diagram 301...
Page 23: ...Fig 308 Control circuit block diagram 316...
Page 40: ...SECTION 4 MAINTENANCE 4000...
Page 56: ...J4 J12 Option J9 J5 Top view of the FDD Fig 401 Types of connectors 4016...
Page 95: ...Note Refer to item 4 2 1 as to handling of the set screw 4057...
Page 102: ...k Key in Cl SET TMAX L Confirm as in item j 4064...
Page 104: ...Notch B position TP6 voltage 0 5V Max LED indicator Fig 422 Check of file protect sensor 4066...
Page 125: ...k Eject the level disk and release the Invert and ADD modes of the oscilloscope 4087...
Page 136: ...Fig 431 Adjustment track alignment 4098...
Page 153: ...Fig 436 Adjustment of index sensor 4115...
Page 172: ...Fig 440 Replacement of head pad 4134...
Page 176: ...Plate Fig 441 CSS Ass y and shift lever position 4138...
Page 177: ...SECTION 5 DRAWINGS PARTS LIST 500...
Page 179: ...r Fig 501 External view No l 502...
Page 181: ...PCBA DD motor servo Fig 503 External view No 3...
Page 182: ...Fig 504 External view No 4 505...
Page 183: ...Partis nrnnber of the FDD Fig 505 Extemal view No 5 506...
Page 188: ...Fig 506 Mechanical section break down 511...
Page 199: ...PCBA DD MOTOR SERVO PARTS LOCATION Type S i 522A...
Page 200: ...PCBA DD TOR SERVO PARTS LOCATION Type TO 522B...
Page 201: ...PCBA DD MOTOR SERVO PARTS LOCATION Type G 522C...
Page 202: ...PCBA DD MOTOR SERVO PARTS LOCATION Type T 522D...
Page 204: ...523B PCBA DO MOTOR SERVO SCHEMATIC Type K...
Page 205: ...o 523C i 1 PACB DD HOTOR SERVO SCHEMATIC Type G...
Page 206: ...CV 5 3 3 H 2SV 523D PC DD M o t o r SERVO SCHEMATIC Type T...
Page 207: ...PCBA MFD CONTROL B PARTS LOCATION PCB ISSUE A G 524A...
Page 208: ......
Page 209: ...PCBA FRONT OPT PARTS LOCATION 525 PO I...
Page 210: ......
Page 211: ......
Page 212: ......
Page 213: ......
Page 214: ......
Page 215: ......
Page 216: ......