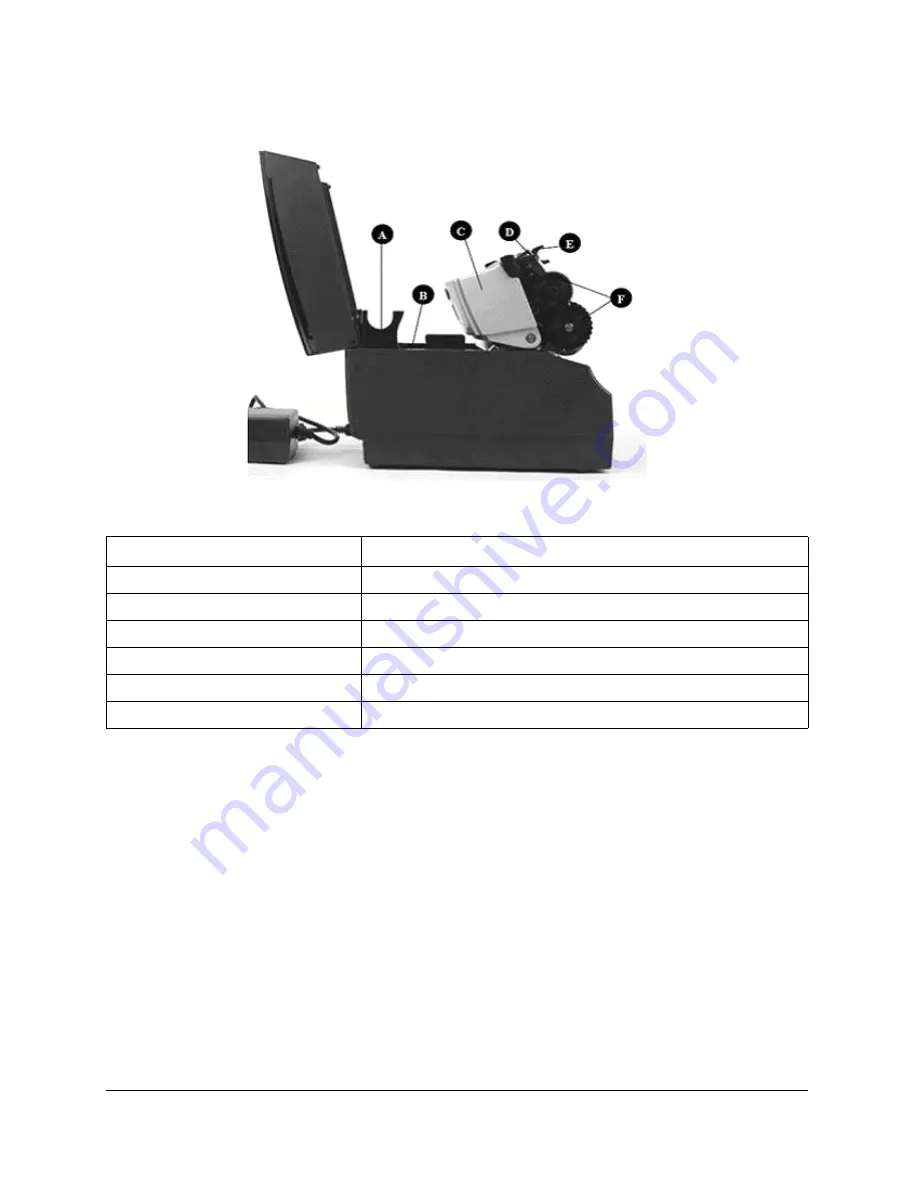
G e t t i n g S t a r t e d
2-3
Inside the Printer
Figure 2-2: Side View
Device
Use
A – Large roll spindle slot
Holds large roll media
B – Standard roll spindle slot
Holds standard roll media
C – Cast metal user interface cover
Contains user interface buttons
D – Printhead
Printing mechanism
E – Printhead bracket
Holds the printhead
F – Ribbon drive gear
Feeds ribbon through the printer