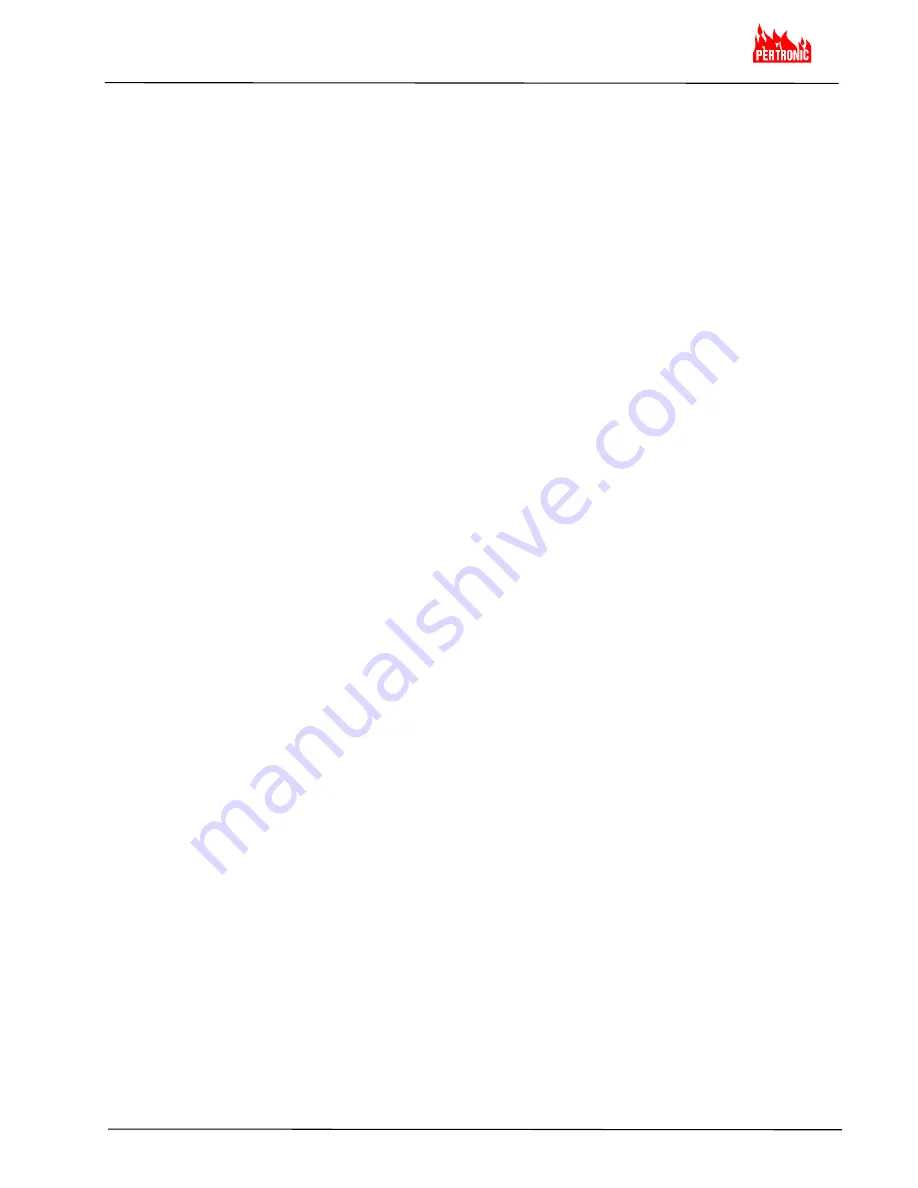
FAAST 7100X
INSTALLATION AND MAINTENANCE INSTRUCTIONS
© Pertronic Industries Ltd
22
FAAST XS (7100X) Installation Guide Iss 1.0, 201606
SECTION F : SYSTEM TEST AND COMMISSIONING:
F1. Required
Items:
ensure the following items are available:
a) FAAST System Pipe Layout Report:- allows the measured values to be referenced to the values calculated in
PipeIQ.
b) FAAST System Bill of Materials Report
c) As-built Installation Drawings
d) Smoke Pen or other source of smoke with a particulate life cycle
of greater than 120 seconds
e) Timer or stop-watch - to measure the maximum Transport Time
f) Blue-Tak or similar to block holes during Flow tests
g) Locally Required Forms
F2.
Commissioning and Handover
(reference: FIA Code of Practice for ASDs, Issue 3, Feb 2012)
F2a Commission
Testing
The Commissioning Tests to be performed depend on the ASD system application but should be carried out only
when the building is in its normal, intended running state. Appropriate commissioning tests should also be
performed after modifications and/or additions to the ASD system.
Commissioning
The commissioning process has several stages which should be performed, recorded and checked as necessary:
• Inspection of Installation – verify conformity to design, definition of system including mechanical and electrical
installation.
• Power Up/Configuration – required checks and configuration
• Commissioning Tests – include mechanical, functional and performance testing.
• Signalling - verify the connections between the ASD and other connected systems (e.g. FAP, BMS).
• System Check - verify the detector settings are appropriate for the site, as suggested in Table 7 : Sensitivity
Class vs Detection Requirements (refer P24)
• System Handover – include relevant documentation and recorded drawings.
F2b Inspection of Installation
Inspect the installation to confirm that it has been designed and installed correctly for the application and conforms
to the design documentation - in particular;
•
ASD used to replace point-type detectors (Class C) - ensure the installation (particularly Sample Point spacing)
conforms to the relevant standard (eg. NZS4512:2010) and the ASD Sensitivity/Alarm thresholds are correctly
set to ensure that the sensitivity of individual holes meets the minimum performance requirements for individual
points. Note that this may require reference to the approval compliance notes for the particular ASD system and
should also take into account any potential automatic adjustments of the Sensitivity/Threshold settings, which
may occur after commissioning.
•
ASD used for high and enhanced sensitivity (Class A/B) - ensure that the installation conforms to the design
specification - if necessary, measure the air velocities in the protected area to ensure that the design spacing is
appropriate.
•
ASD used as a Primary Sampling System - ensure the pipe and sample points are installed correctly at the Air
Handling Unit (AHU) within the airflow. If monitoring more than one AHU, it is important to ensure different
running speeds do not cause an unbalanced airflow in the pipe, which may affect ASD performance.
•
ASD used for other installations (cabinet, duct work or other specialist protection) - confirm that the ASD system
is in accordance with the design.
Perform a thorough inspection of the mechanical and electrical installation - include;
•
pipe network including correct supports.
•
clear identification of Sampling Points.
•
no obstructions to Sampling Points or remote capillaries.
•
all internal and external electrical wiring has been installed correctly.
•
power supplies are correctly rated and provide the correct emergency battery standby period.
•
correct hole position and sizes.
Before the ASD is powered up, it is very important to check that the pipe is clear of any foreign articles eg. swarf,
dust, etc that will impede or stop the ASD performance.
F2c Power
Up/Configuration
It is very important that the ASD manufacturer’s technical documentation is followed during system set-up. If there
is any doubt refer back to the manufacturer for clarification.
The system should be powered up in accordance with the manufacturer’s recommendations. Prior to carrying out
any functional and performance tests the ASD equipment should be configured for:
• Fire signal Alarm thresholds and detector sensitivity settings to give required sampling point sensitivity.
• Alarm and Fault delay periods.
• Airflow
parameters.
• any other defined parameters.