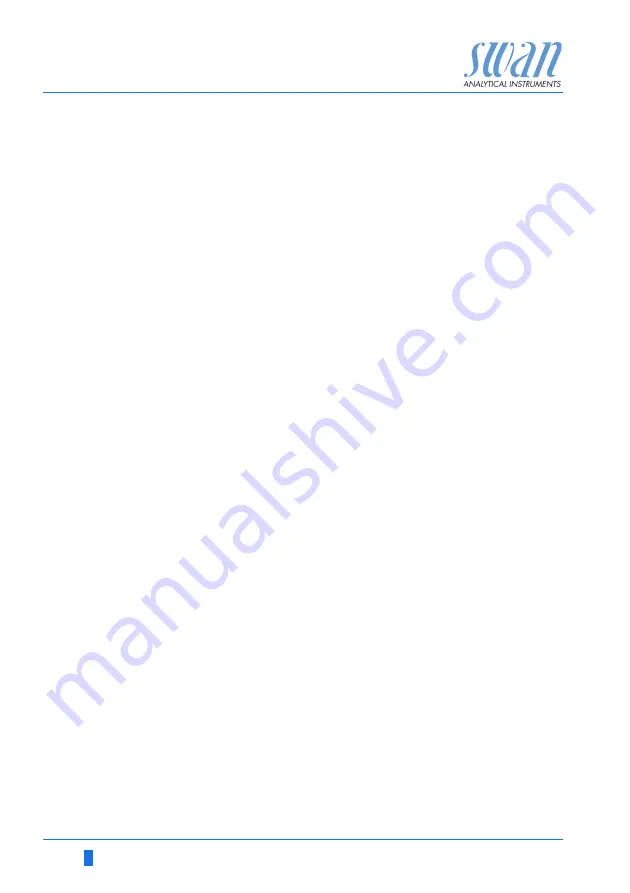
70
A-96.250.871 / 120417
AMI CACE
Program List and Explanations
5.3.4
Input:
The functions of the relays and signal outputs can be de-
fined depending on the position of the input contact, i.e. no function,
closed or open.
5.3.4.1
Active:
Define when the input should be active:
5.3.4.2
Signal Outputs:
Select the operation mode of the signal outputs
when the relay is active:
5.3.4.3
Output/Control:
(relay or signal output):
5.3.4.4
Fault:
5.3.4.5
Delay:
Time which the instrument waits, after the input is deactivat-
ed, before returning to normal operation.
Range: 0–6‘000 Sec
No:
Input is never active.
When closed Input is active if the input relay is closed
When open:
Input is active if the input relay is open
Continuous:
Signal outputs continue to issue the measured
value.
Hold:
Signal outputs issue the last valid measured value.
Measurement is interrupted. Errors, except fatal
errors, are not issued.
Off:
Set to 0 or 4 mA respectively. Errors, except fatal
errors, are not issued.
Continuous:
Controller continues normally.
Hold:
Controller continues on the last valid value.
Off:
Controller is switched off.
No:
No message is issued in pending error list and the
alarm relay does not close when input is active.
Message E024 is stored in the message list.
Yes
Message E024 is issued and stored in the mes-
sage list. The Alarm relay closes when input is
active.
Summary of Contents for AMI CACE
Page 1: ...AMI CACE Version 6 20 and higher A 96 250 871 120417 Operator s Manual...
Page 79: ...AMI CACE Index A 96 250 871 120417 77 Terminals 20 22 23 26 U USB Interface 27 W Wire 18...
Page 80: ...78 A 96 250 871 120417 AMI CACE Notes 12 Notes...