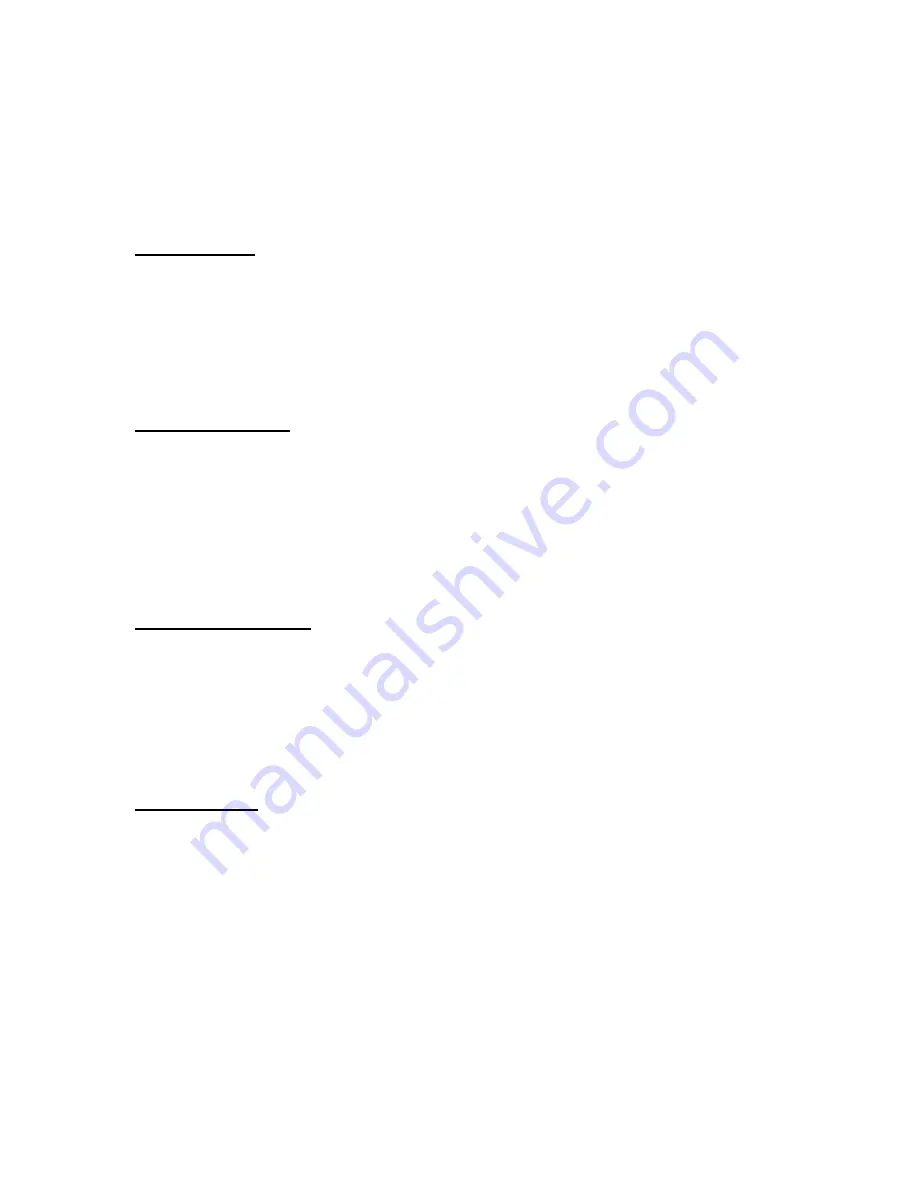
57
11. Operation
Some form of control is required for the majority of SUNDYNE compressor applications. The purpose
of control is twofold: 1) to achieve the desired performance as required by process conditions and 2)
to protect the compressor from mechanical damage due to surge or overload conditions.
This section is a general guideline on controls. A control system should be selected only after
completion of a detailed analysis of the specific installation.
Surge Control
It is recommended that a surge control system be installed whenever there is any chance
that the process flow could decrease appreciably from design flow. In most surge control
systems, a flow sensor is placed in the suction line to the compressor. The signal from this
sensor is input to a controller which controls a valve in the bypass loop. When the minimum
safe flow is reached, this valve opens and the flow through the compressor is kept above the
surge point. Again, the recycled gas must be cooled to prevent heat build-up. Both pneumatic
and electrical surge control systems are available.
Suction Throttling
Suction throttling is generally the most economical control method with a constant speed
drive. Throttling the control valve on the suction side causes a reduction of inlet pressure to
the compressor. Although the compressor creates the same compression ratio as if it were
unthrottled, the discharge pressure is reduced. The net result is to lower the total head output
to the system. The reduction of inlet pressure correspondingly decreases inlet gas density,
and thus, power consumption. Suction throttling also has the advantage of slightly lowering
the compressor surge point.
Discharge Throttling
Discharge throttling is control by means of a valve placed at the compressor discharge. A
constant speed compressor will always operate on its design head-flow curve. For a given
system operating point, the compressor will operate at the system flow rate, thus producing
more head than the system requires. This excess head is throttled by the discharge valve.
Since the throttling occurs downstream of the compressor, there are no power savings by this
method. Discharge throttling offers no real advantages over suction throttling, but is
nonetheless an acceptable control method.
Speed Control
Speed control is the most efficient means of compressor control. To operate at points below
the design head-flow curve, the driver speed may be reduced accordingly. This creates an
infinite “family” of head-flow curves on which the compressor may operate. Since consumed
horsepower, assuming constant inlet conditions, varies as the cube of the speed, substantial
power savings can be realized. Also, the compressor surge point is lowered proportional to
the speed decrease. This method is used mainly on turbine driven units although variable
speed motors or mechanical drives are available. Since the main lube oil pump in the
SUNDYNE compressor is driven by the gearbox input shaft, provision must be made so the
speed is not reduced to a point where adequate lube oil pressure is no longer present.
Summary of Contents for LMC 341F
Page 32: ...28 Figure 5 1 Compressor Cross Section and Clearances ...
Page 69: ...65 SINGLE SEAL ARRANGEMENT ...
Page 70: ...66 DOUBLE SEAL ARRANGEMENT ...
Page 71: ...67 TANDEM SEAL ARRANGEMENT ...
Page 73: ...69 Phoenix Compressor Gearbox Cross Sectional View ...
Page 74: ...70 ...
Page 75: ...71 PHOENIX GEARBOX MODULE DRAWING GB01AY01 ...
Page 76: ...72 ...
Page 77: ...73 ...
Page 78: ...74 ...
Page 79: ...75 ...
Page 80: ...76 ...
Page 81: ...77 ...