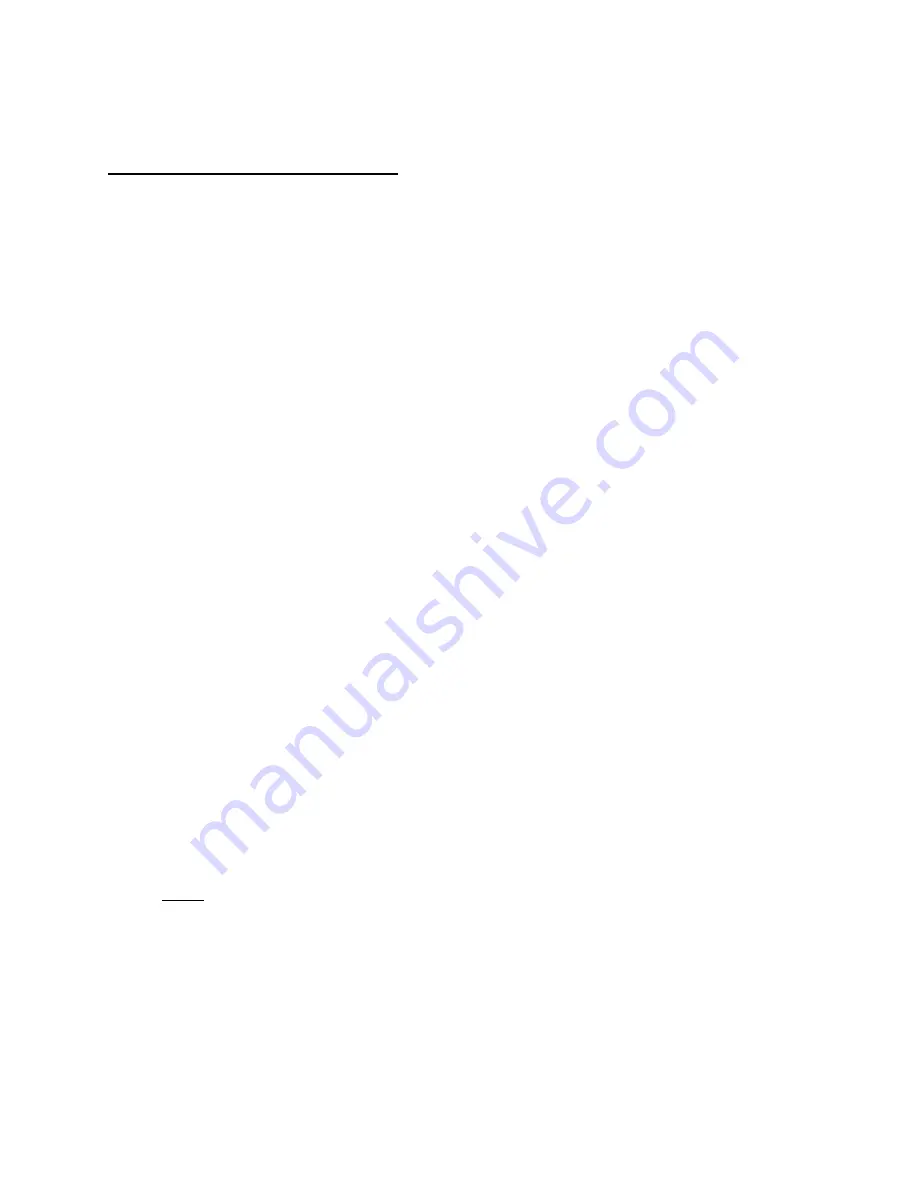
7
Step 10:
Use block valves on both suction and discharge pipes to isolate the compressor during
shutdown, minimize process leakage, and reduce the likelihood of backflow through the
compressor, which can cause reverse rotation.
Seal Environment Control System
For the seal used with the compressor, always maintain the environment shown on the specification
sheet for your unit. For some arrangements and applications, you may need a system to control the seal
environment. For many applications, you can obtain a standard system from the factory. Make sure that
the system is installed properly and that the ports are open or plugged, as applicable.
See Outline
drawing in the Final Data Package.
Always be sure to leave port 1 free to drain leakage from the
gearbox oil seal and vent the gas seal.
You must vent case drain port 1 to atmospheric pressure and allow it to gravity drain properly. Otherwise
oil could contaminate the outboard gas seal. This port can be attached to a flare line, but should not have
back-pressure in excess of 5 psi.
A.
GAS BUFFER SYSTEM – A gas buffer system must be used with double gas seals to prevent
process gas leakage out of the compressor. The buffer must be a cooled, dry, filtered gas, which
is compatible with the process gas and the compressor metallurgy. The buffer is introduced into
seal port 7 at a pressure range of 40 to 80 psi (2.8 to 5.6 kg/cm
2
) greater than compressor
suction pressure (max. of 160 psig – 11.2 kg/cm
2
) and at an average temperature no higher than
250°F (121°C). Part of the buffer flows across the lower seal into the process gas and part flows
across the upper seal and is vented from port 1. A buffer flow of 1.0 to 2.0 scfm (0.028 to 0.056
Nm
3
/min) must be maintained through the seal cavity, and should be regulated by a valve or
orifice on port 2. It is also acceptable to provide a buffer into port 2 and regulate by a valve or
orifice out of port 7. The buffer system must be in operation prior to starting the compressor.
Refer to compressor specification sheet for specific buffer requirements.
A buffer gas may also be used between tandem seals to reduce process leakage when buffer
contamination of the process gas is not permissible. Contact the factory for buffer pressure and
flow requirements.
B.
LIQUID BUFFER SYSTEM – A liquid buffer system is used with double liquid seals and is
functionally identical to a gas buffer. The buffer liquid is introduced into port 7 or 2, allowed to flow
through the seal cavity, and out the opposing port.
Buffer flow should be 0.5 to 3 gpm (2 to 12 liters/min) with an inlet temperature of 60° to 120°F
(16° to 49°C), and inlet pressure a minimum of 20 psi (1.4 kg/cm
2
) above process suction
pressure.
If a closed loop buffer system is used, the buffer must be cooled prior to returning to port 7.
Otherwise, heat generated by seal friction will build up in the buffer, resulting in shorter seal life. If
an open loop system is used, an orifice or valve on port 2 should be used to regulate flow to
proper value.
NOTE The compressor casing of units with double liquid seals must be drained prior to starting.
C.
SEAL FLUSH – An optional seal flush system is available for use with single or tandem gas seal
arrangements when the process gas is contaminated with dust, dirt, or any other types of solid
particles. A clean, cool gas, either from external sources or cooled, filtered gas throttled from the
discharge is introduced into port 5 or 6 at a pressure slightly higher than suction pressure. Thus,
only clean gas will contact the seal face minimizing erosion and seal deterioration.
A flush is not required with a double gas seal due to the flushing action of the buffer leakage
across the lower seal.
Summary of Contents for LMC 341F
Page 32: ...28 Figure 5 1 Compressor Cross Section and Clearances ...
Page 69: ...65 SINGLE SEAL ARRANGEMENT ...
Page 70: ...66 DOUBLE SEAL ARRANGEMENT ...
Page 71: ...67 TANDEM SEAL ARRANGEMENT ...
Page 73: ...69 Phoenix Compressor Gearbox Cross Sectional View ...
Page 74: ...70 ...
Page 75: ...71 PHOENIX GEARBOX MODULE DRAWING GB01AY01 ...
Page 76: ...72 ...
Page 77: ...73 ...
Page 78: ...74 ...
Page 79: ...75 ...
Page 80: ...76 ...
Page 81: ...77 ...