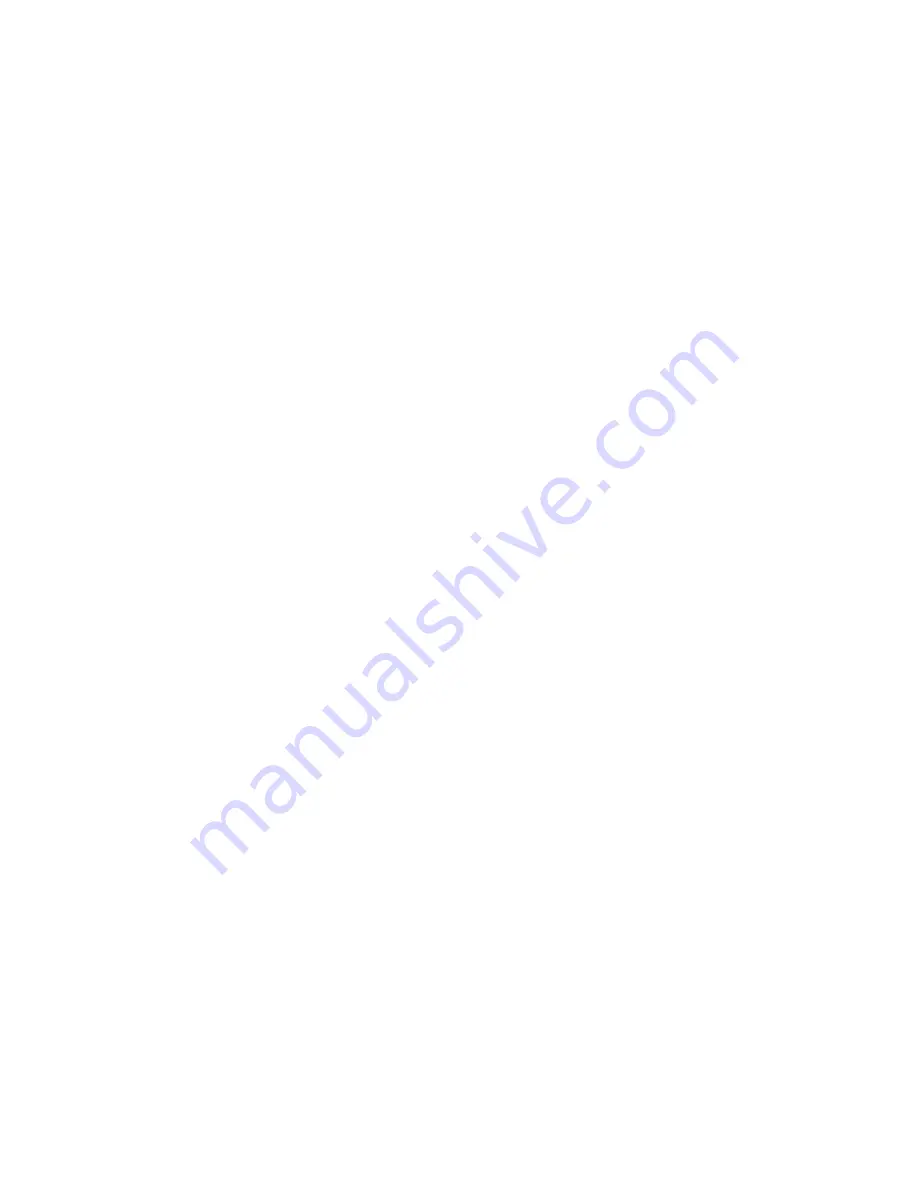
44
7. Inspection of Disassembled Hardware
Step 1
Remove lube jets, then clean and wash all gearbox housings (101B), (102), and (101A)
with solvent and blow dry with clean high pressure air.
Step 2
Make certain to flush out all lube passages and blow dry with clean high pressure air.
Reinstall lube jets into housings immediately.
Step 3
Inspect all bearing locations for critical size requirements (see Table 7.1). If any
dimensions are found to be out of tolerance replace that housing or bearing.
Step 4
Inspect all bearings for damage, if any damage is found replace the bearings with new
items.
Step 5
Inspect all shaft bearing surfaces for scratches, burns, dents, or dings. If bearing
surfaces on shafts are burned and/or scared the shaft should be replaced. Scratches
nicks or dings on shafting should be lightly stoned and polished to remove high spots.
Step 6
Check shaft run-outs for trueness. Replace shaft if it is bent.
Step 7
Inspect all shafts with gears. If gears are missing teeth, or are burned, replace gear or
integral gear shaft as required. If gears show abnormal wear patterns, or have nicks and
dings on the gear teeth, lightly stone or hone and polish nicks and dings from gear teeth.
If abnormal wear pattern is evident this could indicate a bent shaft.
Step 8
Inspect the bearing thrust faces on the idler shaft (A140). If thrust faces are burned or
scored, replace the shaft. Check the thrust surface on the lower spur gear for
abnormalities or replace the shaft assembly.
Step 9
Inspect the thrust face on the lower idler spur gear that is pressed onto the idler shaft
(A140). If the thrust face on this gear is burned or scored replace this gear. If there are
nicks or dings in the thrust face lightly stone or hone and polish these areas back to the
original surface.
Step 10
Inspect the internal lube pump (A160) o-ring seal groove. If there are any nicks or dings
in this area, polish or hone them back to the original surface. If this cannot be
accomplished replace the lube pump (A160). If your gearbox had a catastrophic lube
failure due to the lube pump (A160) you should replace the lube pump as a complete
assembly.
Step 11
Inspect the gearbox seal. If the carbon seal nose is nicked, scratched, or dinged,
disassemble the seal and try to lap the seal nose back into tolerance. The flatness
specification is two light bands or .00002” flatness minimum. If this cannot be achieved
replace the carbon seal nose. Check the constant force spring inside the seal retainer. If
it is cracked, bent or deformed other than the cone shape, it should be replaced. Contact
your customer service representative for part numbers on this seal.
Step 12
Inspect all the sleeves and spacers that were disassembled from the high speed shaft,
Process End. If there are any nicks or dings in the sleeves or spacers lap the locating
surfaces back into tolerance. The specification for these sleeves and spacers is two light
bands flatness or .00002” flatness and parallel conditions between the faces of the
sleeves or spacers of .0003” maximum. If these specifications cannot be maintained then
replace the sleeves or spacers with new hardware.
Step 13
Inspect the process seals. If the carbon seal nose is nicked, scratched or dinged,
disassemble the seals and lap the seal nose back into tolerance. Specification for
Summary of Contents for LMC 341F
Page 32: ...28 Figure 5 1 Compressor Cross Section and Clearances ...
Page 69: ...65 SINGLE SEAL ARRANGEMENT ...
Page 70: ...66 DOUBLE SEAL ARRANGEMENT ...
Page 71: ...67 TANDEM SEAL ARRANGEMENT ...
Page 73: ...69 Phoenix Compressor Gearbox Cross Sectional View ...
Page 74: ...70 ...
Page 75: ...71 PHOENIX GEARBOX MODULE DRAWING GB01AY01 ...
Page 76: ...72 ...
Page 77: ...73 ...
Page 78: ...74 ...
Page 79: ...75 ...
Page 80: ...76 ...
Page 81: ...77 ...