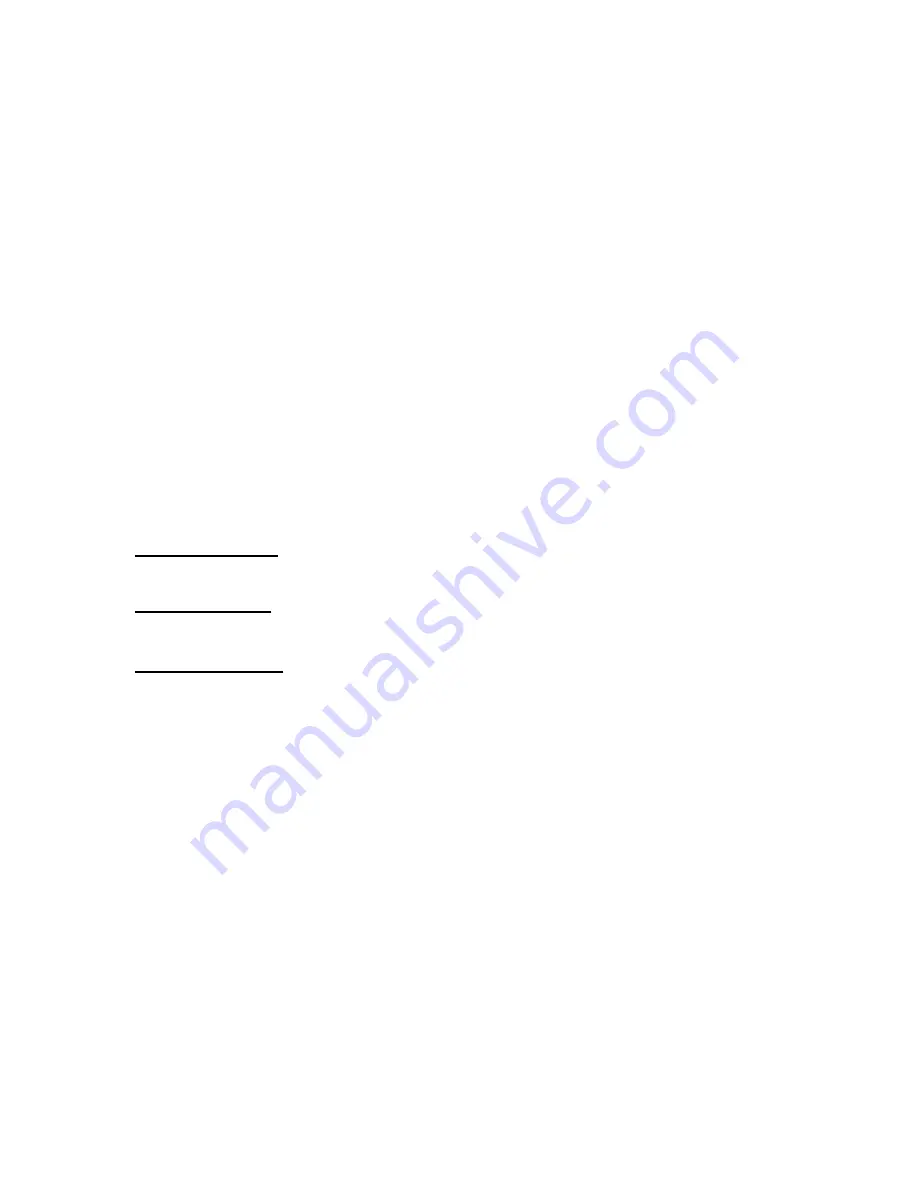
25
shroud height in relation to the diffuser cover (15) and to determine the correct thickness of the
impeller spacer (158C).
In the 3rd assembly, once the correct impeller spacer (158C) is determined, the impeller spacer
(158C), the o-ring (936G) between the impeller spacer (158C) and the impeller (2), and the impeller
(2) are assembled for the final time to complete the assembly.
5a.
Assemble the gearbox, less the gearbox mechanical seal and mating ring, the process
mechanical seal(s) and mating ring(s), the seal housing (30), the diffuser cover (15), and impeller
(2). Ensure end float is within recommended limits; i.e., 0.015” +/- 0.002”.
5b.
With the diffuser cover (15) removed from the seal housing (30), set the diffuser cover bottom
side up on a work bench. Set the impeller (2) in the recessed portion of the diffuser cover and
measure the distance from the outside flat surface of the diffuser cover to the front or blade side
of the impeller shroud as close to the outside edge of the shroud, as possible. The impeller
should be recessed into the diffuser cover a minimum of 0.025”. If the dimension is less than
0.025”, contact Sundyne Compressors in Arvada, Colorado.
5c.
Place the gearbox upside down on a workbench or gearbox stand so the end of the high speed
shaft (A130) protrudes upward. All checks from this step on, should take place with the high
speed shaft resting down on its upper thrust washer or upper thrust tilt pad bearings.
5d.
Assemble the seal component stack-up onto the high speed shaft (A130) without using the
mechanical seals, O-Rings, seal housing (30), or diffuser cover (15). With the high speed shaft
(A130) extending upward, slide on the gearbox mating ring (51D), and then the following parts:
For double seals
,
assemble the upper shaft sleeve (50B), the process mating ring (51C), the
lower shaft sleeve (50A), the impeller spacer (15C) and the impeller (2).
For single seals
, assemble the shaft sleeve (50), the process mating ring (51A), the impeller
spacer (158C), and the impeller (2).
For tandem seals
, assemble the upper shaft sleeve (50B), the upper process mating ring (51C),
the lower shaft sleeve (50A), the lower process mating ring (51A), the impeller spacer (158C), and
the impeller (2).
5e.
To install the impeller (2):
-Check the shaft OD pilot fits and the impeller bore pilot fits and ensure that they are clean and free of
burrs. Clean up, deburr and polish, as needed, to prevent damage to each during assembly.
-Heat the impeller in an oven heated to 350ºF for 30-60 minutes.
-Apply a very small amount of anti-seize compound onto the shaft pilot fits to ease the installation and
removal of the impeller and to prevent galling.
-Lower the heated impeller onto the shaft on top of the stacked up parts, place a soft metal washer
over the impeller, install the impeller bolt (Item #3), and torque per Table 8.1. A soft metal washer is
placed between the impeller and the impeller bolt to prevent damage to the end surfaces of each
part.
-Allow the impeller to cool. This process can be accelerated by blowing shop air past the heated
wheel.
5f.
During the cooling process, retorque the impeller bolt (3) 3-4 separate times to 50 ft. Ibs. When
the impeller is cool, retorque one final time per Table 8.1.
5g.
Once the impeller is installed and cool, recheck the stacked components to ensure that they are
all tight and cannot rotate in relation to one another.
Summary of Contents for LMC 341F
Page 32: ...28 Figure 5 1 Compressor Cross Section and Clearances ...
Page 69: ...65 SINGLE SEAL ARRANGEMENT ...
Page 70: ...66 DOUBLE SEAL ARRANGEMENT ...
Page 71: ...67 TANDEM SEAL ARRANGEMENT ...
Page 73: ...69 Phoenix Compressor Gearbox Cross Sectional View ...
Page 74: ...70 ...
Page 75: ...71 PHOENIX GEARBOX MODULE DRAWING GB01AY01 ...
Page 76: ...72 ...
Page 77: ...73 ...
Page 78: ...74 ...
Page 79: ...75 ...
Page 80: ...76 ...
Page 81: ...77 ...