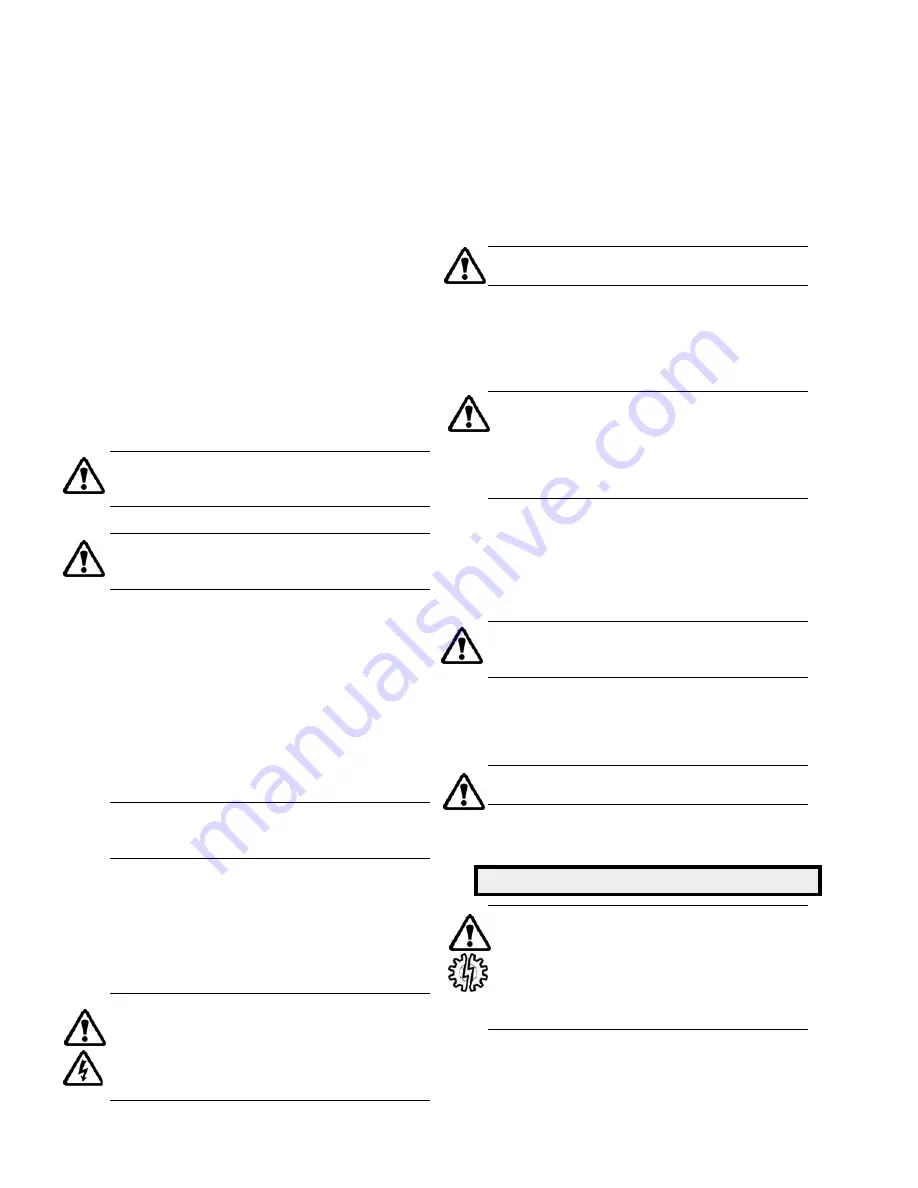
2
Wearing Personal Protective
Equipment
To ensure safety, protective equipment must be
worn at all times when installing, performing
maintenance, or repairing equipment. The
following safety recommendations must be
adhered to for optimum safety:
•
Safety glasses, with the minimum
requirement of side shields, must be worn
at all times.
•
Steel-toed shoes must be worn when
lifting equipment greater than 15 pounds
(7 kg) or if pallet jacks or forklifts are
operated.
•
Hearing protection is strongly
recommended at all times when noise
levels exceed 85 dB during an eight (8.0)
hour period.
Note: Chemical resistant gloves must be used
if chemicals are utilized (refer to Using
Chemicals for additional information).
Note: A dust mask respirator must be worn if
chemicals have warning labels
regarding fumes, dust, or mists.
When using more than one piece of protective
equipment, consider their compatibility. For
example, safety glasses will not interfere with
hearing protection equipment. Be sure to clean
all pieces of personal protective equipment
immediately after each use.
Using Forklifts
Any persons operating a forklift must have an
active recognized operator license.
Note: Before initializing forklift operation,
verify that the lift is in a safe operating
position.
Ensuring Electrical Safety
All electrical sources must be powered-off
before installation, service, or repair of
equipment occurs.
Note: Sundyne recommends that a Lock-
out/Tag-out program be followed prior
to altering the equipment. Locks or
tags must be provided to warn
employees that equipment is
temporarily unavailable.
Once all work has been completed, the person
installing the lock or tag must remove it
according to company procedure.
Testing Equipment
Prior to performing a test on newly installed,
maintained, or repaired equipment; all personnel
in the immediate area must be warned.
Note: Follow company procedures prior to
equipment testing at all times.
Using Chemicals
Any chemicals to be used must be accompanied
by a relevant material safety data sheet (MSDS),
in accordance with government legislation. If
applicable, use chemical proof gloves.
Note: An eye wash station (or equivalent)
should be available in the event of
injury. If any hazardous or flammable
chemicals pass through the equipment,
a complete decontamination of the
equipment is required.
Protection from Falling
Fall protection and associated preventative
measures are required when working on
equipment located six feet or higher from the
ground.
Note: Follow company fall prevention
procedures prior to working on
equipment.
Preventative Machine Guards
Preventative guards must remain in place on all
equipment.
Note: Only remove the guards while
performing maintenance or repair.
Replace the guards immediately after working
on the equipment and prior to start up.
EXPLOSION/FIRE HAZARD
Note: Never use an acetylene torch, open
flame, or heat to attempt to remove
parts that have seized together in
Sundyne equipment. Any residual
process gas or liquid that is flammable
can result in an explosion or fire with
potential for serious injury or death.
Summary of Contents for LMC 341F
Page 32: ...28 Figure 5 1 Compressor Cross Section and Clearances ...
Page 69: ...65 SINGLE SEAL ARRANGEMENT ...
Page 70: ...66 DOUBLE SEAL ARRANGEMENT ...
Page 71: ...67 TANDEM SEAL ARRANGEMENT ...
Page 73: ...69 Phoenix Compressor Gearbox Cross Sectional View ...
Page 74: ...70 ...
Page 75: ...71 PHOENIX GEARBOX MODULE DRAWING GB01AY01 ...
Page 76: ...72 ...
Page 77: ...73 ...
Page 78: ...74 ...
Page 79: ...75 ...
Page 80: ...76 ...
Page 81: ...77 ...