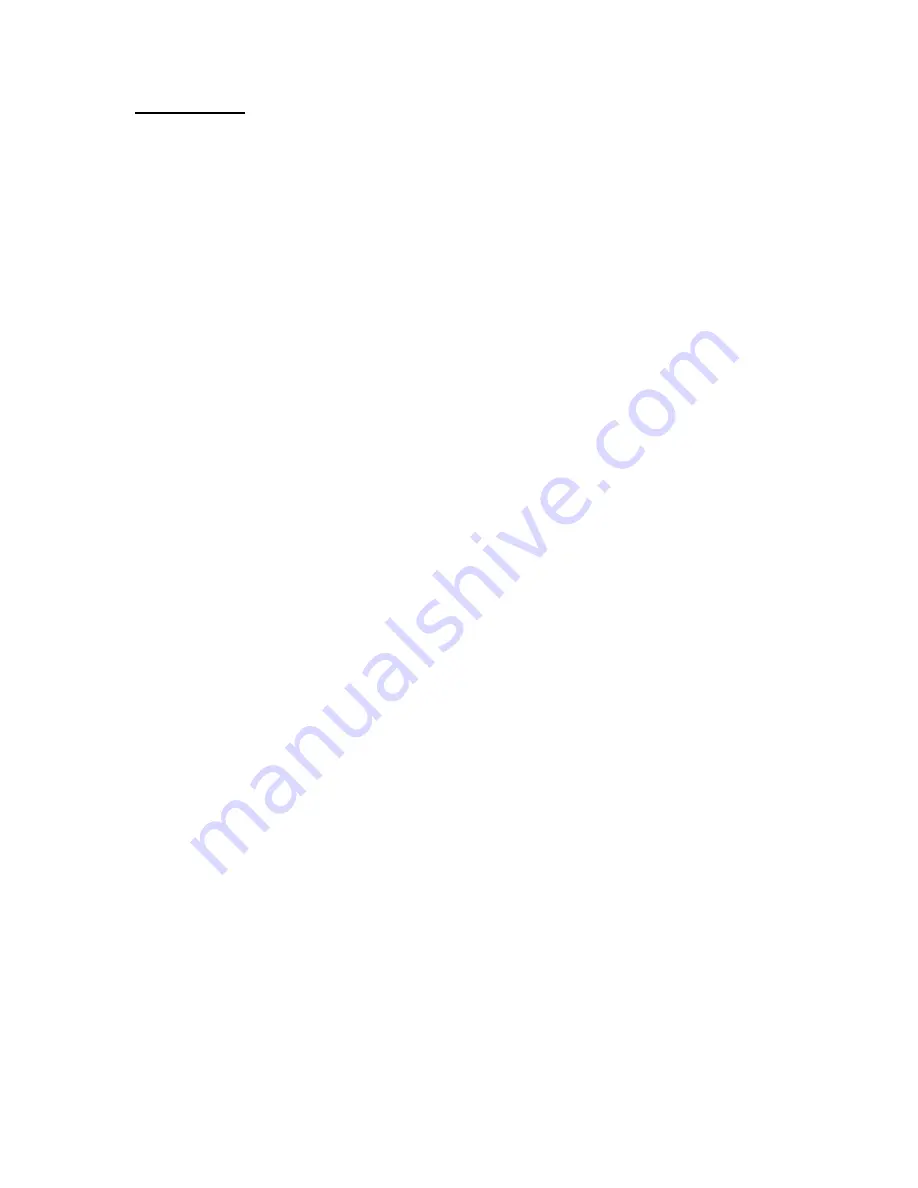
58
Flow Bypass
Flow bypass requires a recycle line from the compressor discharge to suction. The
compressor is operated at the desired flow or discharge pressure and the excess flow not
required by the process is recycled through the bypass. A cooler is required in the loop to
cool the recycled gas to normal suction temperature. This method is generally less efficient
than other methods discussed, but may be warranted in some special situations.
Other aspects which should be considered in compressor operation are:
Series Compressor Control - Inlet throttling on the first stage is the most practical method of
controlling compressor in series. It is necessary to throttle only the first stage, which in turn
acts as a throttle for the second stage. Inlet throttling between stages offers no advantages
and should be avoided. Efficiency gains by variable speed control of series units will seldom
justify its cost and complexity.
Surge control on series units consists of a flow sensor and controller in the suction line of the
first stage. This sends a signal to the control valve in a bypass loop around both
compressors. It must be determined which compressor surges at the lowest inlet flow to the
first unit so the flow controller can be set such that neither compressor will surge. A more
complex system which offers maximum machine protection consists of separate bypass
loops for each unit which are operated by separate flow controllers.
Parallel Compressor Control - The control of two or more compressors operating in parallel
would appear to be relatively simple. More than likely, though no two compressors ever
operate identically across their flow range. To produce identical discharge pressures, one
compressor could be operating at a different flow than the unit in parallel with it. As a result,
the control system would have to include a separate flow controller for each unit. Either
suction or discharge throttling may be used, but again, suction throttling is the preferred
method. If variable speed drivers are used, extreme care must be taken to insure that the
speeds can be precisely controlled. In any case, check valves must be installed in the
discharge line of each compressor to prevent possible back flow due to any slight imbalance
in the characteristics of the compressors. Separate surge control systems for each
compressor should be considered for maximum unit protection.
12. Spare Parts
1. General
Assemblies, subassemblies and components of the Sundyne compressor are illustrated on
the exploded and cross sectional views in Reference D. Refer to your Sundyne Compressor
Specification Sheet for those options applicable to your compressor. The corresponding parts
lists, keyed to each part by item number, identify detail parts by part name, quantity and
location. A complete bill of materials list for the compressor and gearbox end is included in
the final data package. Refer to the unit outline drawing for a list of the major kit bills of
material.
2.
Recommended Spare Parts
Refer to your final data package for recommended spare parts identified for your particular
unit. These are provided as guidelines only.
Summary of Contents for LMC 341F
Page 32: ...28 Figure 5 1 Compressor Cross Section and Clearances ...
Page 69: ...65 SINGLE SEAL ARRANGEMENT ...
Page 70: ...66 DOUBLE SEAL ARRANGEMENT ...
Page 71: ...67 TANDEM SEAL ARRANGEMENT ...
Page 73: ...69 Phoenix Compressor Gearbox Cross Sectional View ...
Page 74: ...70 ...
Page 75: ...71 PHOENIX GEARBOX MODULE DRAWING GB01AY01 ...
Page 76: ...72 ...
Page 77: ...73 ...
Page 78: ...74 ...
Page 79: ...75 ...
Page 80: ...76 ...
Page 81: ...77 ...