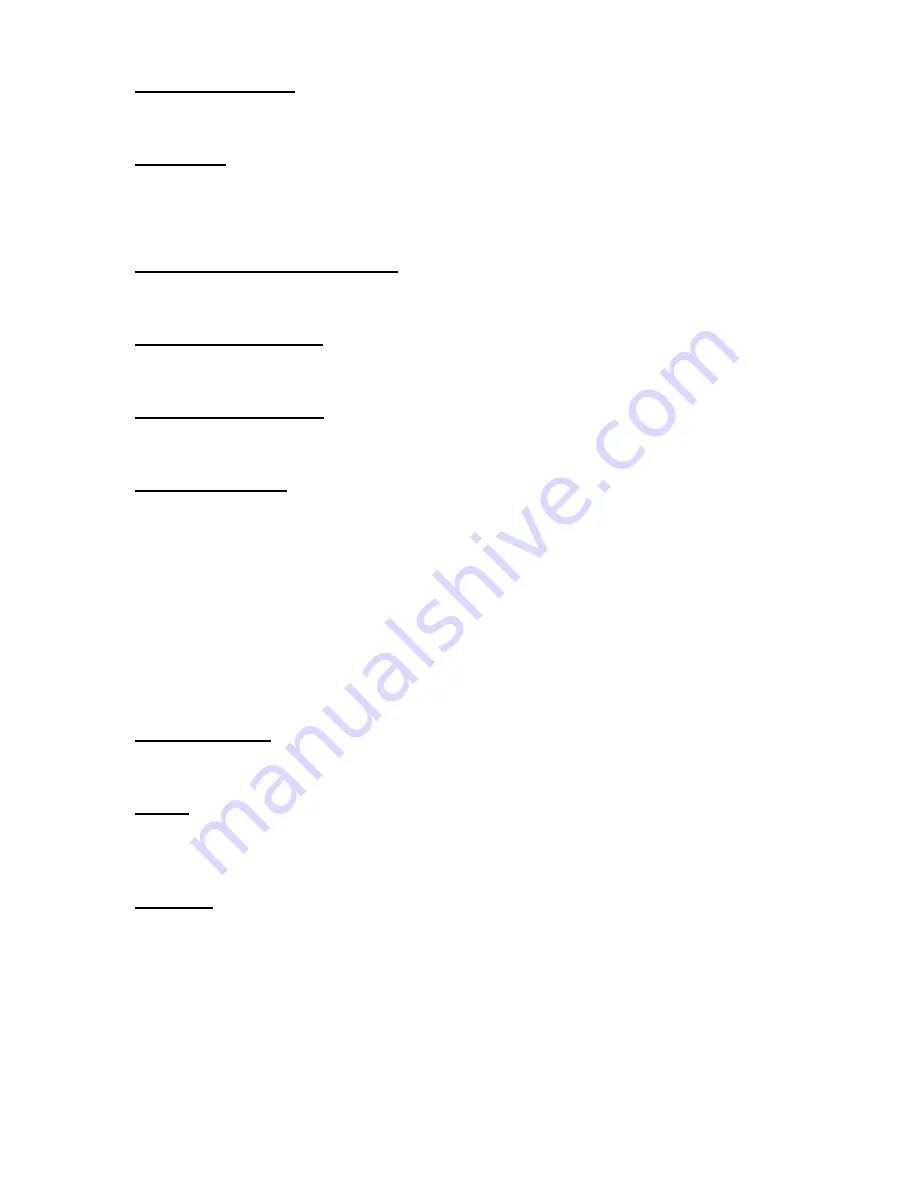
63
Driver Instructions
Carefully follow the installation and starting instructions provided by the manufacturer of the driver.
This is included in the final data package.
Auxiliaries
1. Check the utility connections.
2. Verify that the auxiliary piping conforms to Sundyne’s drawings.
3. Verify the connections of the switches, the instruments, and the set points.
4. Calibrate the flow instruments and the other transmitters.
Environmental Control System
Install a system to control the environment of the seal, if required, and verify that port 1 is
properly vented. Drain the compressor casing. (Maximum back pressure = 10 psig)
Pressurize Fluid Loop
Pressurize double seal buffer fluid loop or external seal flush, if required, prior to admitting fluid into
compressor casing.
Check Driver Rotation
Make sure that the gear shaft rotates in the direction indicated by the arrow stamped on the gearbox
of the compressor.
Start Compressor
1. Suction throttling (preferred method): Start the compressor with the discharge valve open while
throttling the suction valve, to bring the compressor to the design operating point. See
specification sheets for the inlet conditions and flow rate.
2. Discharge throttling: Start the compressor with the suction valve completely open while throttling
the discharge valve, to bring the compressor to the design operating point.
3. Variable speed (as applicable): Start the compressor with the suction valve and the discharge
valve open. Check the pressure in the system. If it exceeds the surge point of the compressor (see
the specification sheet and the performance curve), you will need a bypass to protect the
compressor from surging during ramp-up to speed. Never operate the compressor above the
maximum design speed.
Heat Exchanger
If a heat exchanger for the gearbox is installed, adjust the cooling flow to keep the temperature of the
gearbox sump at 120°-180°F (49°-82°C).
Check
Check the following items. Each of these parameters significantly affects the performance of the
system. Head rise, Flow rate, Power consumption, Inlet pressure, Temperature; and Molecular
weight.
Coupling
There are two types of connections between the motor and gearbox; a splined shaft or a coupling.
For splined connections, the splined shaft must be lubricated with the supplied spline grease and the
two
o-rings installed prior to the mounting the motor. It is recommended that the input shaft be rotated by
hand prior to mounting the motor. If the unit has a coupling, be sure coupling gap is correct and
bolting between coupling halves is tight. The instruction manual contains coupling set-up information.
Summary of Contents for LMC 341F
Page 32: ...28 Figure 5 1 Compressor Cross Section and Clearances ...
Page 69: ...65 SINGLE SEAL ARRANGEMENT ...
Page 70: ...66 DOUBLE SEAL ARRANGEMENT ...
Page 71: ...67 TANDEM SEAL ARRANGEMENT ...
Page 73: ...69 Phoenix Compressor Gearbox Cross Sectional View ...
Page 74: ...70 ...
Page 75: ...71 PHOENIX GEARBOX MODULE DRAWING GB01AY01 ...
Page 76: ...72 ...
Page 77: ...73 ...
Page 78: ...74 ...
Page 79: ...75 ...
Page 80: ...76 ...
Page 81: ...77 ...